DI-CALCIUM PHOSPHATE Manufacturing from HCL Route
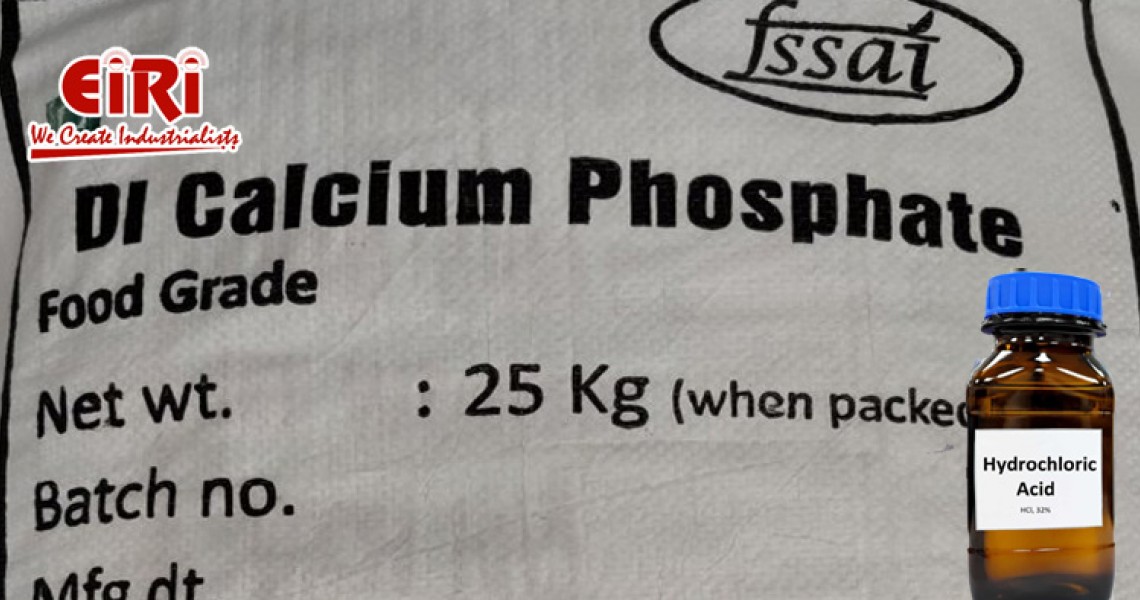
Di-calcium phosphate (DCP) is a vital compound in numerous industries, from agriculture to food and pharmaceuticals. As a major source of calcium and phosphorus, DCP plays a key role in animal nutrition, human supplements, and as a functional additive in various products. The process of manufacturing DCP has evolved over the years, with different methods being employed to maximize efficiency and product quality. One such method, known as the HCL route, uses hydrochloric acid in the production process and is gaining recognition for its efficiency and eco-friendliness. This article explores the significance of DCP, the advantages of using the HCL route, the step-by-step production process, and the future of DCP manufacturing.
Understanding DI-CALCIUM PHOSPHATE: What You Need to Know
Di-calcium phosphate (DCP) is a chemical compound composed of calcium and phosphate. It is widely used in the agricultural industry as a feed additive for livestock, providing essential nutrients like calcium and phosphorus. These minerals are crucial for bone development and overall health in animals, making DCP a highly valuable ingredient in animal feed formulations. Apart from agriculture, DCP is also used in the food industry as a dietary supplement for humans and as a leavening agent in baking. It is commonly added to products like breakfast cereals, noodles, and enriched flour to enhance calcium intake.
The benefits of di-calcium phosphate go beyond nutrition. Its versatile properties, such as its solubility, stability, and non-toxic nature, make it an important component in the pharmaceutical industry. It is used in the production of tablets as a binding agent and also functions as an excipient, helping to deliver active pharmaceutical ingredients effectively. In addition, DCP finds applications in toothpaste, where it serves as a polishing agent and aids in maintaining oral health.
Calcium phosphate compounds like DCP come in various forms, but DCP stands out due to its unique balance of calcium and phosphate content, typically 23% calcium and 18% phosphorus. This balance allows it to be highly effective as a supplement in both animal and human nutrition.
The HCL Route: A Game-Changer in DI-CALCIUM PHOSPHATE Production
The manufacturing of di-calcium phosphate can be achieved through different methods, but the HCL route has emerged as a game-changer. The HCL (hydrochloric acid) route involves the reaction of phosphate rock with hydrochloric acid, followed by purification processes to produce high-quality DCP. This method offers several advantages over traditional production methods, such as higher yields, more efficient use of raw materials, and reduced environmental impact.
One of the major advantages of the HCL route is its cost-effectiveness. Hydrochloric acid is a widely available and relatively inexpensive chemical, making it a cost-efficient choice for manufacturers. Moreover, the HCL process enables the extraction of phosphate from lower-grade rock, which would otherwise be unsuitable for other production routes. This contributes to the conservation of phosphate resources and allows for more sustainable production.
The HCL route is also more environmentally friendly compared to other methods, particularly the sulfuric acid route. By using hydrochloric acid, the production process generates fewer by-products and emissions, leading to lower environmental impact. Additionally, the waste products generated in the HCL route can be more easily managed and treated, further enhancing its sustainability profile.
Step-by-Step Process of DI-CALCIUM PHOSPHATE Manufacturing Using HCL
The production of di-calcium phosphate using the HCL route involves several stages, each critical to ensuring product quality and efficiency. The following is a step-by-step overview of the process:
Raw Material Preparation
The primary raw material for DCP production is phosphate rock, which contains phosphorus in the form of calcium phosphate. Before the production process begins, the phosphate rock is ground into a fine powder to increase its surface area, allowing for more efficient reactions during the process.
Reaction with Hydrochloric Acid
In the first stage of the HCL route, the finely ground phosphate rock is reacted with hydrochloric acid. This reaction produces phosphoric acid and calcium chloride as the primary products. The chemical equation for the reaction is as follows:
Ca3(PO4)2+6HCl→2H3PO4+3CaCl2Ca3(PO4)2+6HCl→2H3PO4+3CaCl2
This step is crucial, as it converts the insoluble calcium phosphate into soluble phosphoric acid, which can be further processed to produce DCP.
Purification of Phosphoric Acid
The phosphoric acid produced in the reaction is then purified to remove impurities such as calcium chloride and other by-products. This purification is typically done using filtration and solvent extraction methods to ensure a high-purity final product.
Precipitation of Di-Calcium Phosphate
Once the phosphoric acid is purified, it is reacted with calcium hydroxide (slaked lime) to precipitate di-calcium phosphate. The chemical reaction is as follows:
2H3PO4+3Ca(OH)2→CaHPO4⋅2H2O+Ca3(PO4)22H3PO4+3Ca(OH)2→CaHPO4⋅2H2O+Ca3(PO4)2
This step results in the formation of DCP, which is then filtered and washed to remove any remaining impurities.
Drying and Granulation
The precipitated DCP is then dried to remove excess moisture, ensuring that the final product is in the desired solid form. In some cases, the dried DCP is granulated to improve its handling and distribution properties, making it easier to transport and incorporate into animal feed or other products.
Quality Control
Throughout the manufacturing process, strict quality control measures are implemented to ensure that the final product meets the required specifications for purity, composition, and particle size. This is essential to guarantee the safety and efficacy of the DCP in its various applications.
Advantages of Using the HCL Route for DICALCIUM PHOSPHATE Manufacturing
The HCL route for di-calcium phosphate production offers several advantages over traditional methods, making it an attractive choice for manufacturers. Some of the key benefits include:
- Cost-Effective Production: The use of hydrochloric acid as a key reagent is more cost-effective compared to other chemicals like sulfuric acid. Additionally, the ability to use lower-grade phosphate rock in the HCL route helps to reduce raw material costs.
- Higher Yield Rates: The HCL route is known for its high yield of di-calcium phosphate, as it allows for more efficient extraction of phosphorus from the phosphate rock. This translates into higher production volumes and better utilization of resources.
- Eco-Friendly Methods: The environmental benefits of the HCL route are significant. The process generates fewer emissions and by-products, and the waste materials produced are easier to manage and treat. This makes the HCL route a more sustainable option for DCP production.
- Industrial Efficiency: The HCL route is a highly efficient process, requiring fewer steps and less energy compared to other production methods. This contributes to faster production times and lower operational costs, making it a more efficient choice for large-scale industrial manufacturing.
Challenges and Solutions in the DI-CALCIUM PHOSPHATE Manufacturing Process from HCL Route
While the HCL route offers numerous advantages, it also presents some challenges that manufacturers must address to ensure smooth production. These challenges include:
- Handling of Hydrochloric Acid: Hydrochloric acid is a corrosive chemical, and its handling requires stringent safety measures to protect workers and equipment. Manufacturers must invest in corrosion-resistant materials and proper safety protocols to mitigate the risks associated with HCL use.
- Quality Control: Ensuring consistent quality in DCP production can be challenging due to variations in the composition of phosphate rock and the chemical reactions involved. Implementing robust quality control systems and regular testing is essential to maintain product standards.
- Waste Management: The by-products of the HCL route, such as calcium chloride, need to be carefully managed to prevent environmental contamination. Developing effective waste treatment and disposal methods is crucial for minimizing the environmental impact of the production process.
The Future of DI-CALCIUM PHOSPHATE Production: Trends and Innovations in the Industry
As the demand for di-calcium phosphate continues to grow, the industry is evolving to meet the challenges of sustainability, efficiency, and innovation. Some of the key trends shaping the future of DCP production include:
- Sustainable Production: There is increasing pressure on manufacturers to adopt more sustainable practices in DCP production. This includes reducing energy consumption, minimizing waste, and using renewable raw materials. The HCL route is already a step in this direction, but further innovations in green chemistry and eco-friendly processes are expected to emerge in the coming years.
- Innovative Manufacturing Techniques: Advances in chemical engineering and process optimization are leading to new methods of DCP production that are more efficient and cost-effective. These innovations are helping manufacturers to reduce production costs and improve the quality of their products.
- Market Growth: The global demand for DCP is expected to continue growing, driven by the increasing need for animal feed, food additives, and pharmaceutical products. As a result, manufacturers are expanding their production capacities and exploring new markets to capitalize on this growth.
Conclusion: Embrace the Benefits of DI-CALCIUM PHOSPHATE Manufacturing Through the HCL Route Today!
The HCL route for di-calcium phosphate manufacturing offers a cost-effective, efficient, and environmentally friendly solution for meeting the growing demand for DCP in various industries. With its higher yield rates, lower production costs, and reduced environmental impact, the HCL route is poised to become the preferred method for DCP production in the future. By embracing the advantages of this innovative production process, manufacturers can unlock new