Paper Bags Manufacturing Business - An Overview
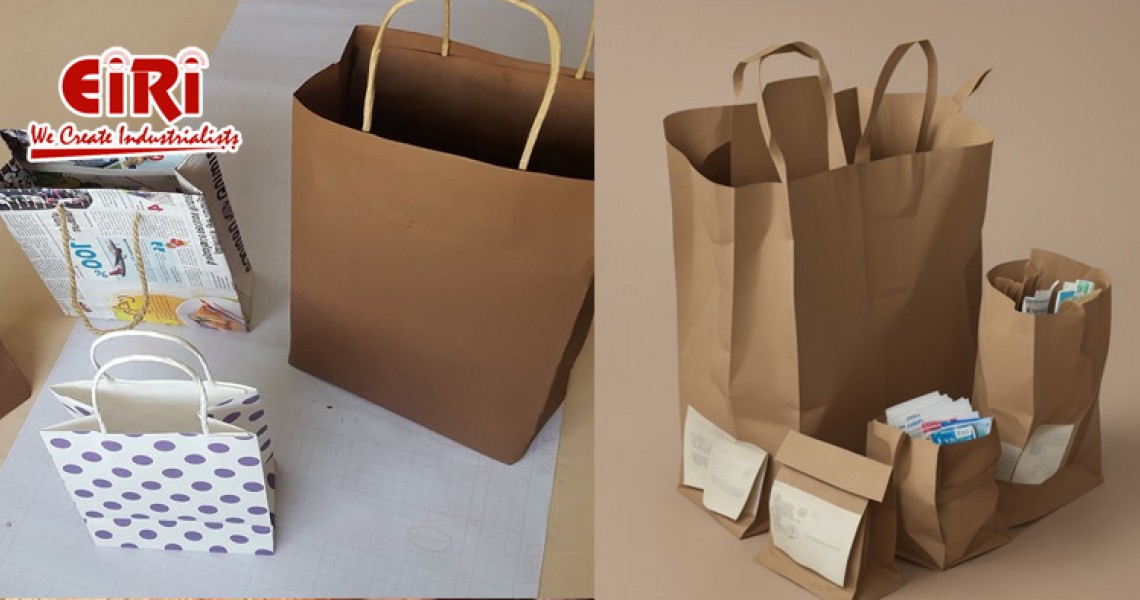
The paper bag manufacturing business is gaining significant momentum due to the growing environmental awareness and increasing restrictions on plastic bag usage worldwide. As consumers and businesses shift towards sustainable practices, paper bags have emerged as a preferred alternative, offering both ecological benefits and a practical solution for packaging needs. This article delves into the various aspects of starting and operating a paper bag manufacturing business, including market overview, manufacturing process, equipment needed, and potential challenges.
Market Overview of Paper Bags Business
The global market for paper bags is expanding rapidly, driven by the increasing demand for eco-friendly packaging solutions. Governments across the globe are implementing stringent regulations against the use of plastic bags, thereby boosting the demand for paper bags. The market is segmented based on product type, application, and end-user industry. Key product types include flat paper bags, multi-wall paper sacks, and handle paper bags, which are used in industries ranging from retail and food & beverage to pharmaceuticals and cosmetics. The growing trend towards sustainability and the rising popularity of recyclable and biodegradable materials are major factors propelling the growth of the paper bag industry.
Manufacturing Process
The manufacturing process of paper bags involves several stages, from sourcing raw materials to producing the final product. Here’s a step-by-step overview of the process:
- Raw Material Sourcing: The primary raw material for paper bag manufacturing is kraft paper, which is chosen for its strength and durability. Other materials include adhesives, inks, and handles (if required).
- Printing: If the bags require branding or custom designs, printing is the first step. The kraft paper is fed into a printing machine, where designs, logos, or text are printed using eco-friendly inks.
- Cutting: The printed paper is then cut into the required dimensions. Cutting machines ensure precision and uniformity in size.
- Folding and Gluing: The cut paper is folded into the desired bag shape. Automatic folding machines are used to create creases and folds. Adhesive is applied to the edges to secure the folds and form the bag.
- Bottom Formation: The bottom of the bag is formed and glued. This step ensures that the bag can hold items securely without tearing.
- Handle Attachment: If handles are required, they are attached at this stage. Handles can be made from paper, jute, or other eco-friendly materials.
- Quality Control: Finished bags undergo quality control checks to ensure they meet the required standards in terms of strength, durability, and appearance.
- Packaging: The final product is packaged and prepared for distribution.
Equipment Needed for Paper Bag Manufacturing
Setting up a paper bag manufacturing unit requires a range of specialized machines and equipment to ensure efficient and high-quality production. Each piece of machinery plays a crucial role in the production process, from printing and cutting to folding, gluing, and attaching handles. Here is an in-depth look at the key equipment needed:
Printing Machine
The printing machine is an essential piece of equipment in the paper bag manufacturing process, especially if the bags need to be branded or customized with logos, designs, or text. This machine can handle various printing techniques such as flexographic, offset, or digital printing, depending on the specific requirements. Flexographic printing is commonly used due to its efficiency and ability to print on uneven surfaces like kraft paper. The machine applies eco-friendly inks to the paper, ensuring that the final product is both attractive and environmentally sustainable. High-quality printing machines ensure crisp, clear, and vibrant prints, which are critical for brand visibility and appeal.
Cutting Machine
Once the paper is printed, it needs to be cut into the required sizes and shapes for the bags. The cutting machine ensures precision and uniformity in the dimensions of the paper, which is vital for the consistency and quality of the final product. There are various types of cutting machines, including rotary cutters and guillotine cutters, each suited to different production needs. These machines are equipped with advanced sensors and controls to handle high-speed cutting with minimal wastage. Accurate cutting is crucial as it directly impacts the folding and gluing processes, ensuring that the bags have the correct dimensions and structure.
Folding and Gluing Machine
The folding and gluing machine is responsible for shaping the cut paper into the desired bag form. This machine automatically folds the paper along pre-determined lines and applies adhesive to the edges to secure the folds. Advanced folding and gluing machines can handle various bag designs and sizes, making them versatile for different production requirements. They are equipped with precise control systems to ensure uniformity and accuracy in the folding process. The gluing mechanism must apply just the right amount of adhesive to ensure strong bonds without causing excess glue to spill over, which could compromise the bag’s appearance and functionality.
Bottom Formation Machine
The bottom formation machine is critical for creating the base of the bag, ensuring it can hold items securely. This machine folds and glues the bottom of the bag, forming a sturdy base that can withstand weight and pressure. A well-formed bottom is essential for the structural integrity of the bag, particularly for those intended to carry heavy or bulky items. The machine uses precision mechanisms to create strong, clean folds and applies adhesive uniformly to ensure durability. This step is particularly important for bags used in retail and grocery stores, where the ability to hold various items without tearing is crucial.
Handle Attaching Machine
For paper bags that require handles, the handle attaching machine plays a pivotal role. This machine attaches handles to the bags, which can be made from paper, jute, or other eco-friendly materials. The machine can handle various handle designs, including flat, twisted, or die-cut handles, providing flexibility in production. The attachment process must be robust to ensure the handles are securely fastened and can support the weight of the bag’s contents. This machine operates with precision to align and attach handles consistently, enhancing the usability and aesthetic appeal of the bags.
Quality Control Equipment
Quality control equipment is essential to ensure that the finished bags meet the required standards in terms of strength, durability, and appearance. This equipment tests various aspects of the bags, including tensile strength, load-bearing capacity, and resistance to tearing. Advanced quality control systems can also check for defects in printing, cutting, folding, and gluing, ensuring that each bag is of high quality before it reaches the customer. Implementing rigorous quality control measures helps in maintaining consistency, reducing wastage, and enhancing customer satisfaction by delivering reliable and durable products.
Setting up a paper bag manufacturing unit involves investing in a variety of specialized machines and equipment. Each machine plays a critical role in ensuring the efficiency and quality of the production process, from printing and cutting to folding, gluing, and attaching handles. Advanced machinery, coupled with stringent quality control measures, ensures the production of high-quality paper bags that meet the demands of consumers and businesses alike. By investing in the right equipment, manufacturers can optimize their production processes, minimize wastage, and deliver eco-friendly packaging solutions that cater to the growing market demand for sustainable products.
Conclusion
The paper bag manufacturing business is poised for significant growth in the coming years, driven by the global shift towards sustainable packaging solutions. By investing in the right machinery, ensuring high production efficiency, and staying abreast of market trends, entrepreneurs can capitalize on this growing demand. While challenges exist, the potential rewards make this a viable and lucrative business opportunity for those willing to navigate the complexities of the industry. With a focus on quality, innovation, and sustainability, the paper bag manufacturing business can contribute to a greener future while achieving commercial success.