Starting a Radiator/Engine Coolant Manufacturing Business: A Comprehensive Guide
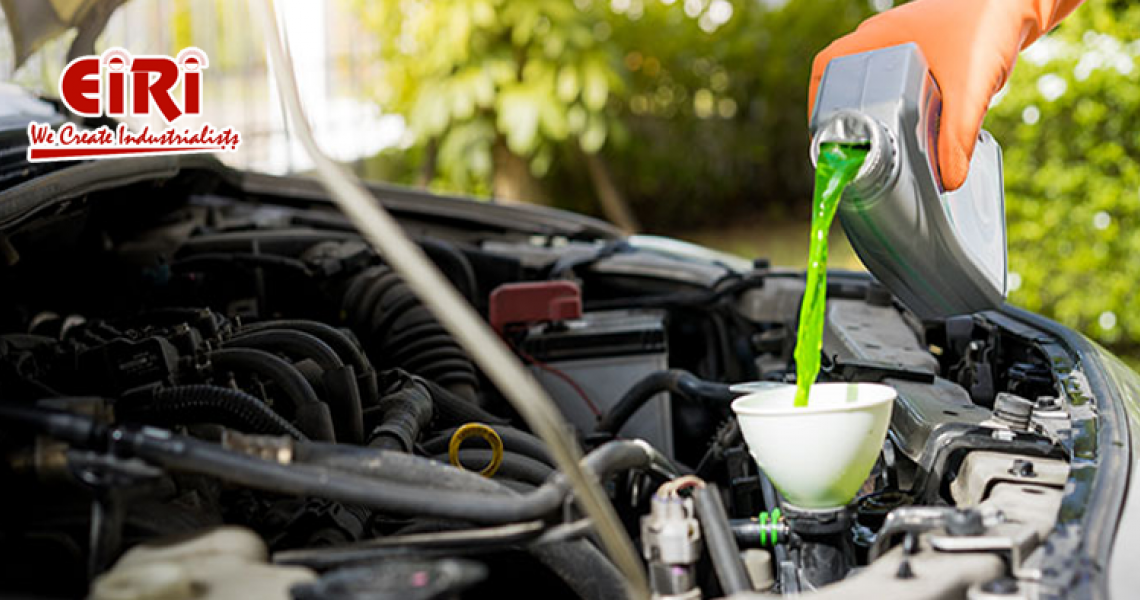
As the automotive and industrial sectors continue to expand, the demand for radiator and engine coolant products has been steadily increasing. Radiators and engine coolants play a critical role in maintaining the optimal performance and efficiency of engines, making them indispensable components in various industries. With a surge in automobile sales and the rising need for efficient thermal management in industrial machinery, the radiator and engine coolant manufacturing business presents a promising and lucrative opportunity for entrepreneurs. In this comprehensive guide, we will delve into the key aspects of starting a radiator/engine coolant manufacturing venture, exploring the market demand, production processes, market analysis, and potential growth prospects in the industry.
As of 2021, the global automotive radiator market was valued at approximately $10.4 billion, and it is projected to reach $14.7 billion by 2026
As of 2021, the global automotive radiator market was valued at approximately $10.4 billion, and it is projected to reach $14.7 billion by 2026, with a compound annual growth rate (CAGR) of 5.6%. The rising demand for vehicles, coupled with advancements in radiator technology, contributes to this growth. On the other hand, the engine coolant market is expected to reach $8.4 billion by 2028, with a CAGR of 4.9%. The growing automotive sector, coupled with increasing awareness of engine efficiency and environmental concerns, drives this demand.
Market Research and Analysis for a Radiator/Engine Coolant Manufacturing Business
Before venturing into the radiator/engine coolant manufacturing business, conducting thorough market research and analysis is crucial for understanding the industry landscape, identifying potential opportunities, and making informed decisions. A comprehensive market study will provide valuable insights into customer preferences, competitor analysis, industry trends, and the overall demand for radiator and engine coolant products.
Market Overview:
The automotive and industrial sectors are the primary consumers of radiator and engine coolant products. The automotive industry, in particular, is witnessing significant growth due to increased vehicle production and the adoption of electric and hybrid vehicles. With the growing focus on reducing carbon emissions and improving fuel efficiency, there is a rising demand for advanced cooling solutions, including high-performance radiators and engine coolants.
In the industrial sector, the use of heavy machinery and equipment is expanding rapidly, necessitating effective thermal management solutions to ensure optimal performance and prevent overheating. This has fueled the demand for efficient engine coolants and radiators that can withstand high temperatures and harsh operating conditions.
Competitor Analysis:
Analyzing the existing players in the radiator/engine coolant manufacturing market is essential for understanding the competitive landscape and identifying potential gaps and opportunities. Look into established radiator and engine coolant manufacturers, their product offerings, distribution channels, and customer feedback to assess their strengths and weaknesses. By understanding what competitors are offering and how they are meeting customer needs, you can strategize your market entry and differentiation plan.
Customer Analysis:
Understanding customer preferences and requirements is key to developing radiator and engine coolant products that meet market demands. Consider conducting surveys, focus groups, and interviews to gather insights from potential customers and industry experts. Identify the specific needs of different customer segments, such as automotive manufacturers, industrial equipment operators, and aftermarket consumers, and tailor your product offerings accordingly.
Market Trends and Emerging Opportunities:
Stay abreast of the latest trends and developments in the radiator and engine coolant industry to identify emerging opportunities. Some key trends include:
- Shift Towards Environmentally Friendly Coolants: With increasing environmental concerns, there is a growing preference for eco-friendly and biodegradable engine coolants that have minimal impact on the environment.
- Adoption of Advanced Cooling Technologies: Advancements in cooling technologies, such as graphene-based coolants and phase-change materials, are gaining traction due to their enhanced thermal properties.
- Rising Demand for Electric Vehicle Cooling Solutions: The rapid growth of the electric vehicle market creates opportunities for specialized cooling systems designed to efficiently manage the heat generated by electric drivetrains and batteries.
- Expansion of Aftermarket Sales: The aftermarket for radiator and engine coolant products presents a significant growth area, with vehicle owners seeking reliable and cost-effective replacements for their cooling systems.
Market Entry Strategy:
Based on the market research findings, develop a comprehensive market entry strategy that outlines how you plan to position your radiator/engine coolant products in the market. Consider factors such as pricing, distribution channels, promotional activities, and customer support services. Identify potential partners, suppliers, and distributors who can help you reach your target market effectively.
Setting Up Your Radiator/Engine Coolant Manufacturing Facility
Once you have conducted thorough market research and analysis for your radiator/engine coolant manufacturing business, the next crucial step is setting up a well-equipped and efficient manufacturing facility. Establishing a state-of-the-art production plant requires careful planning, investment, and adherence to industry standards to ensure the production of high-quality radiator and engine coolant products.
Here is a step-by-step guide to help you set up your manufacturing facility:
Location Selection:
Choose a suitable location for your manufacturing facility. Consider factors such as proximity to raw material suppliers, access to transportation networks, availability of skilled labor, and compliance with local regulations and zoning laws. The location should also be convenient for distribution to target markets.
Factory Design and Layout:
Design an efficient factory layout that optimizes the flow of production processes and minimizes the need for unnecessary material handling. Plan the arrangement of machinery, workstations, storage areas, and utilities to ensure smooth operations and maximize space utilization.
Raw Material Sourcing:
Identify reliable suppliers for the raw materials required in coolant production, such as ethylene glycol, water, additives, and corrosion inhibitors. Establish strong relationships with suppliers to ensure a steady supply of high-quality materials at competitive prices.
Equipment and Machinery:
Invest in modern and technologically advanced production equipment and machinery to enhance the efficiency and productivity of your manufacturing process. Some essential machinery for coolant production includes mixing tanks, reactors, distillation units, and packaging machinery.
Quality Control Measures:
Implement stringent quality control measures at every stage of the manufacturing process to maintain the consistency and reliability of your radiator and engine coolant products. Regularly test and analyze the raw materials and finished products to meet industry standards and customer expectations.
Workforce and Training:
Recruit skilled and trained personnel for your manufacturing facility. Provide comprehensive training to your employees to ensure they understand the production processes, safety protocols, and quality control procedures.
Compliance and Safety:
Comply with all regulatory requirements and safety standards to create a safe and environmentally responsible manufacturing environment. Obtain necessary licenses and permits from local authorities to operate your coolant manufacturing facility legally.
Packaging and Labeling:
Design attractive and informative packaging for your radiator and engine coolant products. Ensure that the packaging meets industry standards and effectively conveys essential product information and safety instructions to customers.
Distribution and Marketing:
Develop a well-structured distribution network to deliver your products to retailers and end consumers efficiently. Implement marketing strategies to promote your coolant products, such as online advertising, trade shows, and partnerships with automotive and industrial equipment suppliers.
Continuous Improvement:
Regularly assess and optimize your manufacturing processes to increase efficiency and reduce production costs. Seek feedback from customers and incorporate their suggestions for product improvement.
By following these steps, you can establish a robust and competitive radiator/engine coolant manufacturing facility that meets the growing demand for high-quality coolant products in the market. Remember that continuous improvement and customer satisfaction are key to long-term success in the coolant manufacturing industry.
The Process of Manufacturing High-Quality Radiators and Engine Coolants
The manufacturing of high-quality radiators and engine coolants is a complex and crucial process that requires precision, adherence to standards, and a deep understanding of the chemical formulations involved. Radiators play a vital role in cooling the engines of various vehicles and industrial machinery, while engine coolants help maintain the engine's temperature and prevent overheating. In this article, we will explore the step-by-step process of producing top-notch radiators and engine coolants, with a focus on the production process, coolant formulation, and quality control measures.
Radiator Production Process:
The manufacturing of radiators involves several stages, starting with the selection of high-grade materials such as aluminum, copper, or brass for the core and tank components. The core is assembled by welding or soldering the tubes and fins together, creating a network for heat transfer. The tank is then connected to the core, and the entire unit is pressure tested to ensure leak-proof performance. After the assembly, the radiator undergoes painting or coating to enhance its durability and resistance to corrosion.
Engine Coolant Formulation and Blending Techniques:
Engine coolants, also known as antifreeze or radiator fluid, are formulated using a base fluid, typically ethylene glycol or propylene glycol, and a mixture of water and additives. The formulation is crucial as it affects the coolant's performance in maintaining engine temperature and preventing corrosion. Blending techniques are employed to achieve the desired concentration of coolant mix, ensuring optimal freezing and boiling points. Additives are added to improve heat transfer, prevent foaming, and protect against rust and corrosion.
Quality Control in Radiator Manufacturing:
Quality control is of utmost importance in radiator production to ensure that each unit meets the required standards and performs efficiently. Radiators undergo rigorous testing, including pressure tests, leak tests, and heat transfer efficiency assessments. The size and design of the radiator are carefully inspected to ensure compatibility with the intended application. Quality control measures also involve visual inspections to identify any defects or imperfections in the manufacturing process.
Quality Control in Engine Coolant Production:
Similarly, engine coolants also undergo stringent quality control measures to ensure their effectiveness and safety. Coolant formulations are thoroughly tested to meet industry standards and comply with environmental regulations. Key quality control tests include pH levels, freeze point analysis, boiling point analysis, and stability tests. These tests help confirm that the coolant will function correctly under various conditions and offer the necessary protection to the engine.
The process of manufacturing high-quality radiators and engine coolants requires attention to detail, advanced blending techniques, and strict adherence to quality control standards. It is essential to work with skilled technicians and engineers who have a deep understanding of coolant formulation and radiator production. By maintaining the highest standards of production and quality control, manufacturers can deliver efficient, durable, and reliable radiators and engine coolants that meet the demands of diverse automotive and industrial applications.
Cost Analysis and Financial Planning for a Radiator/Engine Coolant Manufacturing Venture
Starting a radiator/engine coolant manufacturing venture requires careful financial planning and a comprehensive cost analysis to ensure a profitable and sustainable business. This section will delve into the key financial aspects that entrepreneurs need to consider before embarking on this manufacturing journey.
Initial Investment:
The first step in financial planning is estimating the initial investment required to set up the manufacturing facility. The costs involved include acquiring or leasing the production space, purchasing machinery and equipment for radiator production and coolant blending, and obtaining the necessary permits and licenses. Additionally, funds will be needed for raw material procurement, staff salaries, and initial marketing expenses.
Machinery and Equipment Costs:
The cost of machinery and equipment can be significant, as specialized machinery is needed for the efficient production of radiators and engine coolants. For example, radiator core assembly machines, tank brazing equipment, and coolant blending machines are essential for the manufacturing process. It is crucial to invest in high-quality machinery to ensure productivity and product quality.
Raw Material Sourcing:
The cost of raw materials plays a crucial role in the financial viability of the venture. For radiator manufacturing, the cost of materials such as aluminum, copper, and brass for the core and tanks needs to be considered. In coolant production, the prices of ethylene glycol or propylene glycol and various additives will impact the overall cost. Developing strategic partnerships with reliable suppliers can help manage material costs.
Labor Costs:
Labor costs are an essential aspect of the financial plan. Skilled technicians and engineers are required to operate the machinery, perform quality control tests, and manage the production process efficiently. It is essential to determine the number of employees needed and factor in their salaries, benefits, and training expenses.
Overhead Expenses:
Overhead expenses encompass various costs, such as rent, utilities, maintenance, insurance, and administrative expenses. Careful consideration of these costs is essential to estimate the total operational expenses accurately.
Marketing and Distribution:
An allocation for marketing and distribution expenses should be included in the financial plan. Effective marketing strategies are necessary to promote the products and reach potential customers. Distribution costs will vary based on the chosen distribution channels and geographic coverage.
Conclusion: Taking Your Radiator/Engine Coolant Manufacturing Business to Success
Starting a radiator/engine coolant manufacturing business presents exciting opportunities in the automotive and industrial sectors. The growing demand for high-quality radiators and engine coolants, driven by the expanding automotive market and increasing awareness of engine efficiency, makes this venture promising and rewarding.
To ensure success, entrepreneurs must meticulously plan the financial aspects, prioritize quality control measures, and implement efficient production processes. Investing in state-of-the-art machinery and sourcing top-notch raw materials are essential steps toward delivering superior products to the market.
As you embark on this journey, consider seeking expert guidance and market insights to streamline your business operations. At Engineers India Research Institute (EIRI), we offer comprehensive project reports and consultancy services that can guide you through each step of setting up your radiator/engine coolant manufacturing facility. Our team of experienced professionals can help you analyze the market, develop a robust business plan, and ensure compliance with regulatory standards.
If you are looking for project reports, market research, or technology books on the radiator and coolant manufacturing industry, feel free to reach out to us.
Together, we can turn your vision into reality and build a successful and sustainable manufacturing venture in the radiator/engine coolant domain. Contact us today for project consultation and support to kick-start your journey towards business excellence.
Remember, the road to success is paved with determination, innovation, and continuous improvement. With the right strategies and a passion for excellence, your radiator/engine coolant manufacturing business can thrive and contribute to the automotive and industrial sectors while achieving remarkable success in this dynamic industry.