Understanding the Legal and Regulatory Requirements for Starting a Manufacturing Business in India
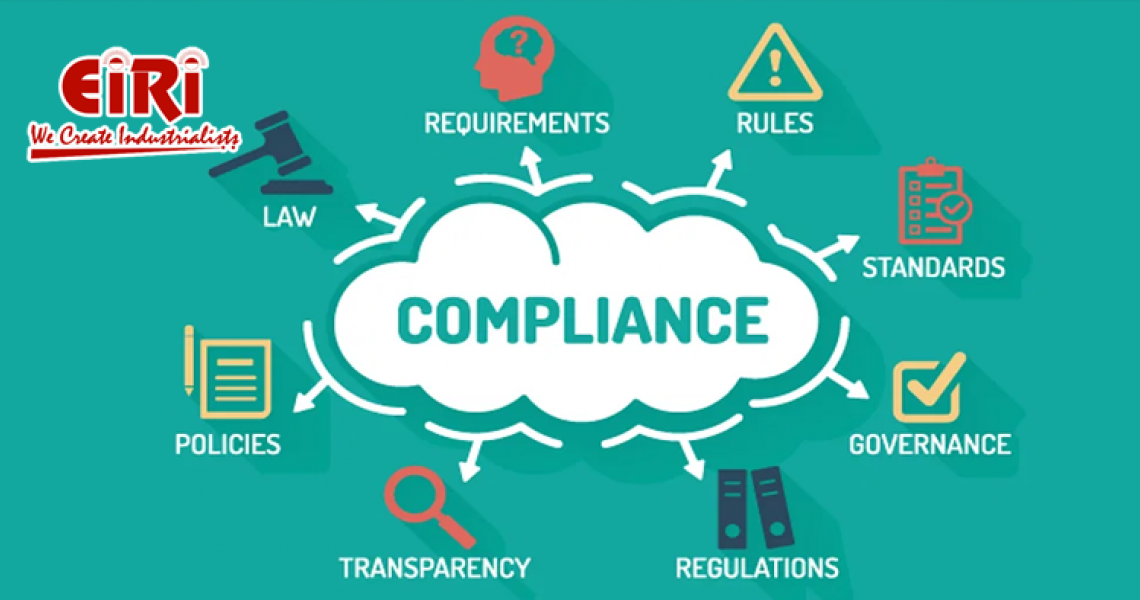
Starting a manufacturing business in India requires a thorough understanding of the legal and regulatory requirements. It is essential to comply with the laws and regulations set by the government to ensure smooth operations and avoid any legal complications.
In India, manufacturing businesses are governed by various laws, including but not limited to the Companies Act, 2013, Factories Act, 1948, Goods and Services Tax (GST) Act, 2017, and Industrial Disputes Act, 1947. These laws cover aspects such as company registration, factory establishment and operation, taxation, labor rights, environmental regulations, intellectual property rights protection, and more.
Step 1: Choosing the Right Business Structure
When starting a business, choosing the right business structure is a critical decision that can impact various aspects of your operations, legal obligations, and financial liability. In India, entrepreneurs have several options to consider, including sole proprietorship, partnership, private limited company, and public limited company. Understanding the features and implications of each structure is essential to make an informed choice. In this section, we will explore these business structures and help you determine which one is best suited for your needs.
Sole Proprietorship:
A sole proprietorship is the simplest and most common form of business structure. In this setup, an individual owns and operates the business. It offers the advantage of complete control and decision-making authority. However, the sole proprietor is personally liable for the business's debts and legal obligations. Registering a sole proprietorship requires minimal formalities, making it an attractive option for small-scale businesses and freelancers.
Partnership:
Partnership is a business structure formed by two or more individuals who share ownership, responsibilities, and profits. In a partnership, the partners contribute capital, skills, or resources to the business. The partnership can be registered or unregistered, but registering is recommended for legal protection and clarity on rights and responsibilities. In a partnership, the partners have joint liability, meaning they are collectively responsible for the business's debts and obligations.
Private Limited Company:
A private limited company is a separate legal entity distinct from its shareholders. It offers limited liability protection, meaning the shareholders' personal assets are generally protected from the company's debts and obligations. A private limited company requires a minimum of two directors and shareholders. It has more compliance requirements compared to sole proprietorship and partnership, but it offers advantages such as credibility, scalability, and easier access to funding. Registering a private limited company with the Registrar of Companies (ROC) is mandatory.
Public Limited Company:
A public limited company is similar to a private limited company, but it can offer shares to the public and is subject to more stringent regulatory requirements. It requires a minimum of seven shareholders and three directors. A public limited company can raise capital by issuing shares to the public through initial public offerings (IPOs). It offers limited liability protection to its shareholders but entails higher compliance and disclosure obligations. Registering a public limited company with the ROC is mandatory.
Choosing the right business structure depends on various factors, including the nature of your business, long-term goals, scalability, liability protection, and funding requirements. It is advisable to consult with legal and financial professionals to assess your specific needs and make an informed decision. Additionally, consider factors such as tax implications, governance, and ease of doing business when evaluating different business structures.
Step 2: Registering Your Business with Relevant Authorities
Once you have decided on the appropriate business structure for your manufacturing business, the next crucial step is to register your business with the relevant authorities in India. Proper registration ensures that your business is legally recognized, compliant with regulations, and eligible for various benefits and services. In this section, we will explore the key registrations you need to consider for your manufacturing business.
Registrar of Companies (RoC) Registration:
For private limited companies and public limited companies, registering with the Registrar of Companies (RoC) is mandatory. The RoC is responsible for maintaining a registry of companies in India. The registration process involves submitting the necessary documents, including the company's memorandum and articles of association, director information, and address proof. The RoC issues a Certificate of Incorporation, which serves as proof of your company's legal existence.
Goods and Services Tax (GST) Registration:
Goods and Services Tax (GST) is a unified tax system that replaced various indirect taxes in India. As a manufacturer, you are required to register for GST if your annual turnover exceeds the specified threshold. GST registration enables you to collect and remit taxes on your goods and services. It also allows you to claim input tax credits on your purchases. The registration process involves submitting the necessary documents and obtaining a unique GST identification number (GSTIN).
Import Export Code (IEC) Registration:
If your manufacturing business involves importing or exporting goods, obtaining an Import Export Code (IEC) registration is essential. The IEC is a 10-digit unique identification number issued by the Directorate General of Foreign Trade (DGFT). It is mandatory for any person or entity engaged in import or export activities. The registration process involves submitting the required documents, such as address proof, identity proof, and bank details, to the DGFT.
Other Registrations and Licenses:
Depending on the nature of your manufacturing business, you may need additional registrations and licenses. For example, if your business involves handling hazardous materials, you may need to obtain licenses from the respective authorities. You may also need environmental clearances, trade licenses, and industry-specific permits. It is important to research and identify the specific registrations and licenses applicable to your industry and comply with the necessary requirements.
It is advisable to consult with professionals or engage the services of a business registration consultant to navigate the registration process smoothly. They can guide you through the documentation requirements, assist in filling out the necessary forms, and ensure compliance with the applicable laws and regulations.
Remember, timely registration with the relevant authorities is crucial to avoid legal complications and enjoy the benefits and protections offered to registered businesses. It also establishes credibility and enhances your business's reputation. By completing the necessary registrations, you can focus on growing your manufacturing business while ensuring compliance with the legal and regulatory framework.
Step 3: Acquiring Necessary Licenses and Permits
In addition to registering your manufacturing business, you will need to acquire certain licenses and permits to operate legally and ensure compliance with regulatory requirements. These licenses and permits demonstrate that your business adheres to safety standards, environmental regulations, and other industry-specific guidelines. Let's explore some of the key licenses and permits you may need to obtain.
Factory License:
A Factory License is a mandatory requirement for manufacturing units in India. It is issued under the provisions of the Factories Act, 1948. This license ensures that your manufacturing facility meets the prescribed safety standards and provides a safe working environment for your employees. The licensing process involves submitting an application along with necessary documents, such as building plans, machinery details, and safety measures implemented within the premises.
Pollution Control Board Consent Certificate:
As a manufacturing business, you need to comply with environmental regulations and obtain a Pollution Control Board (PCB) Consent Certificate. This certificate is issued by the State Pollution Control Board (SPCB) or Pollution Control Committee (PCC). It ensures that your manufacturing processes and emissions are within permissible limits and do not harm the environment. The application process involves providing details of your manufacturing activities, pollution control measures, and undertaking regular audits and compliance reports.
Fire Safety Certificate:
Ensuring fire safety measures in your manufacturing unit is essential to protect lives and property. Obtaining a Fire Safety Certificate is mandatory under the Fire Services Act and rules applicable in your state. The certificate is issued by the local fire department after conducting inspections to verify compliance with fire safety norms. It involves assessing fire extinguishing systems, emergency exits, fire alarms, and other safety measures in your facility.
Other Industry-Specific Licenses and Permits:
Depending on the nature of your manufacturing business, you may need additional industry-specific licenses and permits. For example, if you are involved in food processing, you may require a Food Safety and Standards Authority of India (FSSAI) license. If you are manufacturing pharmaceutical products, you may need approvals from the Drug Control Department. It is important to research and identify the specific licenses and permits applicable to your industry and comply with the necessary requirements.
Acquiring these licenses and permits requires thorough knowledge of the regulatory framework, adherence to safety standards, and proper documentation. It is advisable to engage the services of a consultant or expert in regulatory compliance to ensure a smooth and hassle-free process.
Remember, acquiring the necessary licenses and permits is not just a legal requirement but also a commitment to maintaining high standards of safety, environmental sustainability, and compliance. It instills confidence in your customers, suppliers, and stakeholders, and enhances the reputation and credibility of your manufacturing business.
Step 4: Complying with Labor Laws and Employment Regulations
As an employer in India, it is crucial to comply with labor laws and employment regulations to ensure fair and lawful employment practices. These laws are in place to protect the rights and welfare of workers and promote a harmonious work environment. Let's explore some key aspects of labor laws and employment regulations that you need to consider for your manufacturing business.
Labor Laws in India:
Labor laws in India govern various aspects of employment, including working conditions, wages, social security, and industrial relations. Some of the key labor laws applicable to manufacturing businesses include the Factories Act, Minimum Wages Act, Employees' Provident Funds and Miscellaneous Provisions Act, and the Employees' State Insurance Act. It is essential to understand and comply with these laws to ensure fair treatment of employees and avoid legal complications.
Employee State Insurance (ESI) Registration:
Under the Employees' State Insurance Act, if you employ more than a specified number of employees, you are required to register for the Employee State Insurance (ESI) scheme. This scheme provides social security benefits such as medical care, sickness benefits, maternity benefits, and disability benefits to employees. Registration involves submitting necessary documents, including employee details and salary information, to the regional office of the Employees' State Insurance Corporation (ESIC).
Provident Fund (PF) Registration:
The Employees' Provident Fund (EPF) is a social security scheme that aims to provide retirement benefits to employees. As an employer, you are required to register for the Provident Fund (PF) scheme and contribute a portion of the employee's salary to the fund. The registration process involves obtaining a unique Employer Identification Number (EPF Code) and registering with the Employees' Provident Fund Organization (EPFO).
Compliance with Employment Contracts and Benefits:
It is important to have clear and legally compliant employment contracts that outline the terms and conditions of employment, including wages, working hours, leave policies, and other benefits. Ensure that you provide employees with the required benefits such as paid leave, medical insurance, and other statutory benefits as per labor laws.
Ensuring Health and Safety of Employees:
Compliance with health and safety regulations is essential to provide a safe and healthy working environment for your employees. This includes maintaining proper safety measures, providing protective equipment, implementing safety training programs, and adhering to occupational health guidelines. Regular audits and inspections should be conducted to identify and address any potential risks or hazards.
Maintaining Employment Records:
As an employer, you are required to maintain various employment records, including attendance records, salary records, leave records, and other relevant documentation. These records should be accurate, up-to-date, and readily accessible for compliance purposes and any statutory inspections.
Complying with labor laws and employment regulations not only ensures legal compliance but also promotes a positive work culture, fosters employee loyalty, and safeguards the rights and well-being of your workforce. Non-compliance can result in penalties, legal disputes, and damage to your business reputation.
It is advisable to seek professional advice or consult with labor law experts to ensure proper compliance with labor laws and employment regulations. They can assist you in understanding the specific requirements applicable to your manufacturing business and guide you through the registration processes and ongoing compliance obligations.
In conclusion, complying with labor laws and employment regulations is essential for your manufacturing business in India. This involves adhering to labor laws, obtaining necessary registrations such as ESI and PF, ensuring compliance with employment contracts and benefits, maintaining health and safety standards, and keeping accurate employment records. By prioritizing labor law compliance, you create a supportive and legally compliant work environment, benefiting both your employees and your business.
Step 5: Ensuring Compliance with Environmental Regulations
Environmental regulations play a crucial role in the manufacturing industry to protect the environment and promote sustainable practices. As a responsible manufacturer, it is essential to understand and comply with the environmental regulations applicable to your operations. Let's explore some key aspects of ensuring compliance with environmental regulations in the manufacturing industry.
Environmental Regulations in the Manufacturing Industry:
The manufacturing industry is subject to various environmental regulations aimed at minimizing the impact of industrial activities on the environment. These regulations govern areas such as air quality, water pollution, waste management, noise pollution, and the use of hazardous substances. Familiarize yourself with the relevant environmental laws and regulations in your jurisdiction to understand your compliance obligations.
Conducting Environmental Impact Assessments (EIA):
Before establishing or expanding a manufacturing facility, it may be necessary to conduct an Environmental Impact Assessment (EIA). An EIA evaluates the potential environmental impacts of the proposed project and identifies measures to mitigate adverse effects. This assessment helps ensure that the project complies with environmental regulations and minimizes its environmental footprint.
Obtaining Hazardous Waste Management Authorization:
Manufacturing processes often generate hazardous waste that must be managed and disposed of appropriately to prevent environmental harm. Depending on the nature and volume of hazardous waste generated, you may need to obtain a Hazardous Waste Management Authorization from the regulatory authorities. This authorization outlines the requirements for proper storage, transportation, treatment, and disposal of hazardous waste.
Implementing Pollution Control Measures:
To minimize environmental pollution, it is essential to implement appropriate pollution control measures. This may include installing pollution control equipment such as air scrubbers, wastewater treatment systems, and noise reduction measures. Regular monitoring of emissions and effluents can help ensure compliance with permissible limits set by environmental authorities.
Waste Management and Recycling:
Efficient waste management and recycling practices are vital for reducing the environmental impact of manufacturing operations. Implementing waste segregation, recycling programs, and responsible disposal methods can help minimize the amount of waste sent to landfills and conserve natural resources. Ensure compliance with waste management regulations, including proper labeling, storage, transportation, and disposal of different types of waste.
Continuous Compliance Monitoring and Reporting:
Maintaining compliance with environmental regulations requires ongoing monitoring and reporting of relevant parameters. This may involve regular monitoring of emissions, effluents, noise levels, and waste generation. Maintain accurate records of monitoring data and submit periodic reports to the appropriate environmental authorities as required by the regulations.
By ensuring compliance with environmental regulations, your manufacturing business not only meets its legal obligations but also contributes to sustainable development and social responsibility. Non-compliance can result in penalties, legal consequences, reputational damage, and adverse environmental impacts.
It is advisable to engage environmental consultants or experts who can provide guidance on compliance with environmental regulations specific to your manufacturing operations. They can assist in conducting environmental assessments, developing pollution control measures, implementing waste management practices, and ensuring compliance with reporting requirements. Ensuring compliance with environmental regulations is vital for the manufacturing industry. This involves understanding and adhering to applicable environmental regulations, conducting Environmental Impact Assessments (EIAs), obtaining Hazardous Waste Management Authorization, implementing pollution control measures, and practicing responsible waste management and recycling. By prioritizing environmental compliance, your manufacturing business can operate sustainably, protect the environment, and contribute to a greener future.