Detailed Project Report on aluminium extrusion
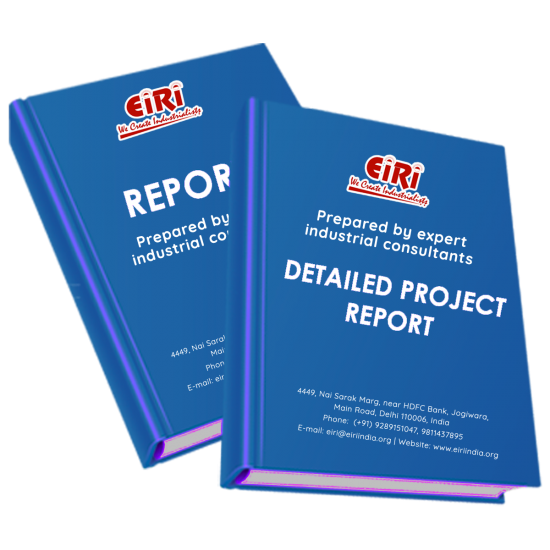
- More than 40 years of experience
- Managed by expert industrial consultants
- ISO 9001-2015 Certified
- Registered under MSME, UAM No: DL01E0012000
- 24/5 Research Support
Get your quesries resolved from an industry expert. Ask your queries before report or book purchase. - Custom Research Service
Speak to the our consultant to design an exclusive study to serve your research needs. - Quality Assurance
All reports are prepared by highly qualified consultants & verified by a panel of experts. - Information Security
Your personal & confidential information is safe & secure.
ALUMINIUM EXTRUSION
[CODE NO.3785]
Extrusion is a plastic deformation process in which a block of metal (billet) is forced to flow by compression through the die opening of a smaller cross-sectional area than that of the original billet Extrusion is an indirect-compression process. Indirect-compressive forces are developed by the reaction of the workpiece (billet) with the container and die; these forces reach high values. The reaction of the billet with the container and die results in high compressive stresses that are effective in reducing the cracking of the billet material during primary breakdown from the billet. Extrusion is the best method for breaking down the cast structure of the billet because the billet is subjected to compressive forces only.
Extrusion can be cold or hot, depending on the alloy and the method used. In hot extrusion, the billet is preheated to facilitate plastic deformation
Factors Affecting Extrusion
Shape is a determining factor in the part's cost and ease with which it can be extruded. In extrusion a wide variety of shapes can be extruded, but there are limiting factors to be considered. These include size, shape, alloy, extrusion ratio, tongue ratio, tolerance, finish, factor, and scrap ratio. If a part is beyond the limits of these factors, it cannot be extruded successfully.
The size, shape, alloy, extrusion ratio, tongue ratio, tolerance, finish, and scrap ratio are interrelated in the extrusion process as are extrusion speed, temperature of the billet, extrusion pressure and the alloy being extruded.
In general, extrusion speed varies directly with metal temperature and pressure developed within the container. Temperature and pressure are limited by the alloy used and the shape being extruded. For example, lower extrusion temperatures will usually produce shapes with better quality surfaces and more accurate dimensions. Lower temperatures require higher pressures. Sometimes, because of pressure limitations, a point is reached where it is impossible to extrude a shape through a given press.
The preferred billet temperature is that which provides acceptable surface and tolerance conditions and, at the same time, allows the shortest possible cycle time. The ideal is billet extrusion at the lowest temperature which the process will permit. An exception to this is the so-called press-quench alloys, most of which are in the 6000 series. With these alloys, solution heat-treat temperatures within a range of 930°-980° F must be attained at the die exit to develop optimum mechanical properties.
At excessively high billet temperatures and extrusion speeds, metal flow becomes more fluid. The metal, seeking the path of least resistance, tends to fill the larger voids in the die face, and resists entry into constricted areas. Under those conditions, shape dimensions tend to fall below allowable tolerances, particularly those of thin projections or ribs.
Another result of excessive extrusion temperatures and speeds is tearing of metal at thin edges or sharp corners. This results from the metal's decrease in tensile strength at excessively high-generated temperatures. At such speeds and temperatures, contact between the metal and the die bearing surfaces is likely to be incomplete and uneven, and any tendency toward waves and twists in the shape is intensified.
As a rule, an alloy's higher mechanical properties means a lower extrusion rate. Greater friction between the billet and the liner wall results in a longer time required to start the billet extruding. The extrusion ratio of a shape is a clear indication of the amount of mechanical working that will occur as the shape is extruded.
Extrusion Ratio = area of billet/area of shape.
When the extrusion ratio of a section is low, portions of the shape involving the largest mass of metal will have little mechanical work performed on it. This is particularly true on approximately the first ten feet of extruded metal. Its metallurgical structure will approach the as-cast (coarse grain) condition. This structure is mechanically weak and shapes with an extrusion ratio of less than 10:1 may not be guaranteed as to mechanical properties.
As might be expected, the situation is opposite when the extrusion ratio is high. Greater pressure is required to force metal through the smaller openings in the die and extreme mechanical working will occur. Normally acceptable extrusion ratios for hard alloys are limited to 35:1 and for soft alloys, it is 100:1. The normal extrusion ratio range for hard alloys is from 10:1 to 35:1, and for soft alloys is 10:1 to 100:1. These limits should not be considered absolute since the actual shape of the extrusion can affect results. The higher the extrusion ratio, the harder the part is to extrude which is the result of the increased resistance to metal flow. Hard alloys require maximum pressure for extrusion and are even more difficult because of their poor surface characteristics which demand the lowest possible billet temperature.
Difficulty factor is also used to determine a part's extrusion performance. Factor is the perimeter of the shape divided by the weight per foot. Factor = Perimeter of Shape/ Weight per Foot. Weight per foot is of primary importance because of the consideration for profitable press operation. As might seem obvious, a lighter section normally requires a smaller press to extrude it. However, other factors may demand a press of greater capacity such as a large, thin wall hollow shape. Though it has low weight per foot it may take more press tonnage to extrude it. The same reasoning applies to the factor as with the extrusion ratio. A higher factor makes the part more difficult to extrude consequently affecting press production.
The tongue ratio also plays an important role in determining a part's extrusion performance. The tongue ratio of an extrusion is determined as follows: square the smallest opening to the void, calculate the total area of the shape, and then divide the opening squared by the area.. The higher the ratio, the more difficult the part will be to extrude.
In order to help us understand your needs and requirements and service you better, the following is a check list of things to consider when submitting items to an extruder for quoting or new business:
Advantages of the extrusion process:
There are several advantages of the modern extrusion process
1. A variety of shapes are possible, especially with hot extrusion.
2. Grain structure and strength properties are enhanced in cold and warm extrusion.
3. Fairly close tolerances are possible, especially in cold extrusion.
4. Little or no wasted material is created. However, a limitation is that the cross section of the extruded part must be uniform throughout its length.
COST ESTIMATION
Plant Capacity 20 MT/Day
Land & Building (15000 sq.mt.) Rs. 11.07 Cr
Plant & Machinery Rs. 8.95 Cr
Working Capital for 2 Months Rs. 14.97 Cr
Total Capital Investment Rs. 35.62 Cr
Rate of Return 47%
Break Even Point 43%
- INTRODUCTION
- FACTORS AFFECTING EXTRUSION
- ADVANTAGES OF THE EXTRUSION PROCESS
- TYPES OF EXTRUDED PROFILES
- CLASSIFICATION OF ALUMINIUM EXTRUSION
- (A) DIRECT (FORWARD) EXTRUSION
- (B) INDIRECT (BACKWARD) EXTRUSION
- (C) HOT EXTRUSION
- (D) COLD EXTRUSION AND WARM EXTRUSION
- PROPERTIES
- PROPERTIES OF ALUMINIUM
- WEIGHT
- STRENGTH
- LINEAR EXPANSION
- MACHINING
- FORMABILITY
- CONDUCTIVITY
- JOINING
- REFLECTIVITY
- SCREENING EMC
- CORROSION RESISTANCE
- NON-MAGNETIC MATERIAL
- ZERO TOXICITY
- USES AND APPLICATION
- USES
- APPLICATION
- B.I.S. SPECIFICATION
- PROCESS FLOW CHART
- MANUFACTURING PROCESS
- THE STEPS IN THE EXTRUSION PROCESS ARE AS FOLLOWS
- DESCRIPTION OF PROCESS
- MANUFACTURING PROCESS OF ALUMINIUM INGOT
- (1) SCRAP PRETREATMENT
- METHODS OF PRETREATMENT
- (A) COMMINUTION
- (B) CLEANING
- METHODS OF CLEANING
- (I) MECHANICAL CLEANING
- (II) PYROMETALLURGICAL CLEANING
- (III) HYDROMETALLURGICAL CLEANING
- (C) SORTING
- METHODS OF SORTING
- (I) MAGNETIC SEPARATION
- (II) AIR SEPARATOR
- (III) EDDY CURRENT
- (IV) DENSE MEDIA SEPARATOR
- (V) HAND SORTING
- (VI) HOT CRUSH
- (VII) INNOVATIVE SORTING SOLUTIONS
- (D) DECOATING
- (2) CHARGING AND FLUXING
- CLASSIFICATION OF FLUXES FOR MELTING ALUMINUM
- (A) COVER FLUXES
- (B) DROSSING FLUXES
- (C) CLEANING FLUXES
- (D) WALL CLEANING FLUXES
- (E) DEGASSING FLUXES
- (F) GRAIN REFINERS
- (G) SILICON MODIFIERS
- (H) DEMAGGING FLUXES
- (3) MELTING PROCESS
- TEMPERATURE CONTROL
- SKIMMING
- ALLOYING
- (4) DEGASSING (MELT TREATMENT)
- (5) INGOT CASTING
- (6) QUALITY CONTROL
- (5) EMISSIONS AND CONTROLS
- (A) SCRAP PRETREATMENT EMISSIONS
- (B) SMELTING/REFINING EMISSIONS
- (6) SHIPMENT
- EXTRUSION PROCESS
- (1) BILLET PREHEATING
- TABLE 1 TYPICAL BILLET TEMPERATURES OF SOFT AND MEDIUM-GRADE LUMINUM ALLOYS
- TABLE 2 TYPICAL BILLET TEMPERATURES OF HARD ALUMINUM ALLOYS
- (2) EXTRUSION
- (3) QUENCHING
- (4) STRETCHING
- (5) CUTOFF
- (6) ARTIFICIAL AGING
- TABLE 3 TYPICAL HEAT TREATMENT PARAMETERS OF SOME 6XXX ALLOYS
- (7) INSPECTION AND TESTING
- EXTRUSION MATERIALS INSPECTION
- ALUMINUM ALLOY CHECK
- EXTRUSION DYE CHECK
- ADDITIVES CHECK
- EXTRUSION VISUAL INSPECTION
- VISUAL DEFECTS CHECK
- COLOR AND GLOSSINESS CHECK
- DIMENSIONAL INSPECTION
- COATING AND FINISHING CHECK
- WEIGHT AND DENSITY CHECK
- EXTRUSION PERFORMANCE INSPECTION
- TENSILE TEST
- WELDABILITY CHECK
- WORKABILITY CHECK
- CORROSION RESISTANCE
- FLAMMABILITY TESTING
- HARDNESS TEST
- WEATHERING RESISTANCE TESTING
- ABRASION RESISTANCE
- CHEMICAL RESISTANCE
- PLANT AND MACHINERY
- EXTRUSION PRESS
- DESCRIPTION OF EXTRUSION PRESS
- PROCESS FLOW CHART
- (A) FOR INGOT
- (B) FOR EXTRUSION
- MARKET OVERVIEW OF ALUMINIUM EXTRUSION
- ALUMINIUM EXTRUSIONS - THE PROS AND CONS
- INDIAN ALUMINIUM EXTRUSION INDUSTRY
- THE PLAYERS
- THE FUTURE
- SPREADING AWARENESS
- TOP TEN ALUMINIUM EXTRUSION COMPANIES IN INDIA
- JINDAL ALUMINIUM
- MAAN ALUMINIUM
- HINDALCO
- THE SUPERFINE GROUP
- GLOBAL ALUMINIUM
- ALOM GROUP
- CENTURY EXTRUSIONS
- GALCO
- SALCO
- EAGLE EXTRUSION PRIVATE LIMITED
- GLOBAL MARKET POSITION OF ALUMINIUM EXTRUSION
- INCREASING ADOPTION OF PRE-ENGINEERED BUILDINGS
- PLANT LAYOUT
- CUSTOMER LIST OF ALUMINIUM EXTRUSION
- SUPPLIERS OF ALUMINIUM EXTRUSION SECTIONS
- SUPPLIERS OF ALUMINIUM PROFILE
- SUPPLIERS OF RAW MATERIALS
- SUPPLIERS OF ALUMINIUM SCRAP
- SUPPLIERS OF SILICON POWDER
- SUPPLIERS OF IRON POWDER
- SUPPLIERS OF COPPER POWDER
- SUPPLIERS OF MAGNESIUM POWDER
- SUPPLIERS OF NICKEL POWDER
- SUPPLIERS OF ZINC POWDER
- SUPPLIERS OF LEAD POWDER
- SUPPLIERS OF TIN POWDER
- SUPPLIERS OF PACKING MATERIAL
- SUPPLIERS OF PICKLING CHEMICALS
- SUPPLIERS OF DEGREASING CHEMICAL
- SUPPLIERS OF OIL AND GREASE
- SUPPLIERS OF PLANT AND MACHINERY
- SUPPLIERS OF CRUCIBLE FURNACE
- SUPPLIERS OF INGOT CASTING MACHINE
- SUPPLIERS OF SILICON CARBIDE CRUCIBLE
- SUPPLIERS OF SHEREDDER
- SUPPLIERS OF DE-COATER
- SUPPLIERS OF MAGENETIC SEPARATOR
- SUPPLIERS OF CASTING LADDLE
- SUPPLIERS OF SPECROMETER
- SUPPLIERS OF POROSITY TESTING MACHINE
- SUPPLIERS OF ALUMINIUM EXTRUSION PLANT
- SUPPLIERS OF DG SETS
- SUPPLIERS OF EOT CRANE
- SUPPLIERS OF POWER TRANSFORMERS
- SUPPLIERS OF ELECTRICAL PANEL
- SUPPLIERS OF ELECTRIC MOTOR
- SUPPLIERS OF COOLING TOWER
- SUPPLIERS OF EFFULENT TREATMENT PLANT (ETP PLANT)
- SUPPLIERS OF AIR POLLUTION CONTROL EQUIPMENTS
- SUPPLIERS OF AIR CONDITIONING EQUIPMENTS
- SUPPLIERS OF AIR COMPRESSORS
- SUPPLIERS OF PLATFORM WEIGHING MACHINE
- SUPPLIERS OF MATERIAL HANDLING EQUIPMENTS
- SUPPLIERS OF FIRE FIGHTING EQUIPMENTS
- SUPPLIERS OF SHOT BLASTING MACHINE
- SUPPLIERS OF JIGS AND FIXTURE
- SUPPLIERS OF SUBMERSIBLE WATER PUMP
APPENDIX – A:
01. PLANT ECONOMICS
02. LAND & BUILDING
03. PLANT AND MACHINERY
04. OTHER FIXED ASSESTS
05. FIXED CAPITAL
06. RAW MATERIAL
07. SALARY AND WAGES
08. UTILITIES AND OVERHEADS
09. TOTAL WORKING CAPITAL
10. TOTAL CAPITAL INVESTMENT
11. COST OF PRODUCTION
12. TURN OVER/ANNUM
13. BREAK EVEN POINT
14. RESOURCES FOR FINANCE
15. INSTALMENT PAYABLE IN 5 YEARS
16. DEPRECIATION CHART FOR 5 YEARS
17. PROFIT ANALYSIS FOR 5 YEARS
18. PROJECTED BALANCE SHEET FOR (5 YEARS)
How to Make Project Report?
Detailed Project Report (DPR) includes Present Market Position and Expected Future Demand, Technology, Manufacturing Process, Investment Opportunity, Plant Economics and Project Financials. comprehensive analysis from industry covering detailed reporting and evaluates the position of the industry by providing insights to the SWOT analysis of the industry.
Each report include Plant Capacity, requirement of Land & Building, Plant & Machinery, Flow Sheet Diagram, Raw Materials detail with suppliers list, Total Capital Investment along with detailed calculation on Rate of Return, Break-Even Analysis and Profitability Analysis. The report also provides a birds eye view of the global industry with details on projected market size and then progresses to evaluate the industry in detail.
We can prepare detailed project report on any industry as per your requirement.
We can also modify the project capacity and project cost as per your requirement. If you are planning to start a business, contact us today.
Detailed Project Report (DPR) gives you access to decisive data such as:
- Market growth drivers
- Factors limiting market growth
- Current market trends
- Market structure
- Key highlights
Overview of key market forces propelling and restraining market growth:
- Up-to-date analyses of market trends and technological improvements
- Pin-point analyses of market competition dynamics to offer you a competitive edge major competitors
- An array of graphics, BEP analysis of major industry segments
- Detailed analyses of industry trends
- A well-defined technological growth with an impact-analysis
- A clear understanding of the competitive landscape and key product segments
Need Customized Project Report?
- Ask for FREE project related details with our consultant/industry expert.
- Share your specific research requirements for customized project report.
- Request for due diligence and consumer centric studies.
- Still haven't found what you're looking for? Speak to our Custom Research Team
About Engineers India Research Institute:
Note: We can also prepare project report on any subject based on your requirement and country. If you need, we can modify the project capacity and project cost based on your requirement.
Our Clients
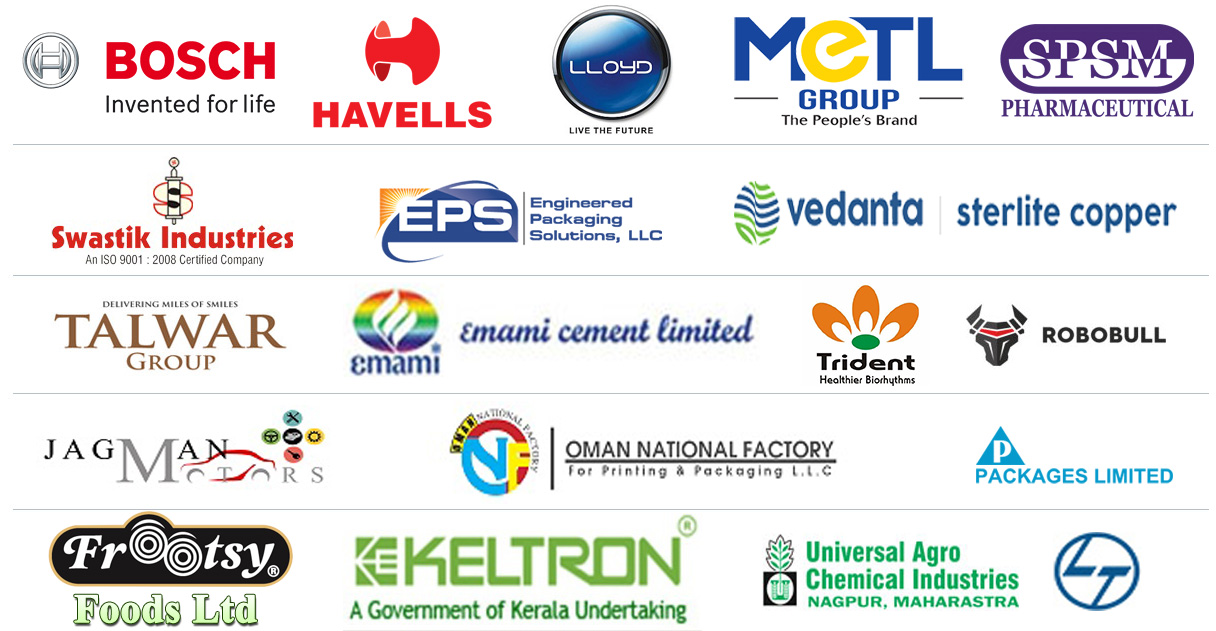
Our Approach
- Our research reports comprehensively cover Indian markets (can be modified as per your country), present investigation, standpoint and gauge for a time of five years*.
- The market conjectures are produced on the premise of optional research and are cross-accepted through associations with the business players
- We use dependable wellsprings of data and databases. What's more, data from such sources is handled by us and incorporated into the report
Why buy EIRI reports?
- Our project reports include detailed analysis that help to get industry Present Market Position and Expected Future Demand.
- Offer real analysis driving variables for the business and most recent business sector patterns in the business
- This report comprehends the present status of the business by clarifying a complete SWOT examination and investigation of the interest supply circumstance
- Report gives investigation and top to bottom money related correlation of real players/competitors
- The report gives gauges of key parameters which foresees the business execution