Detailed Project Report on Silicone Oil
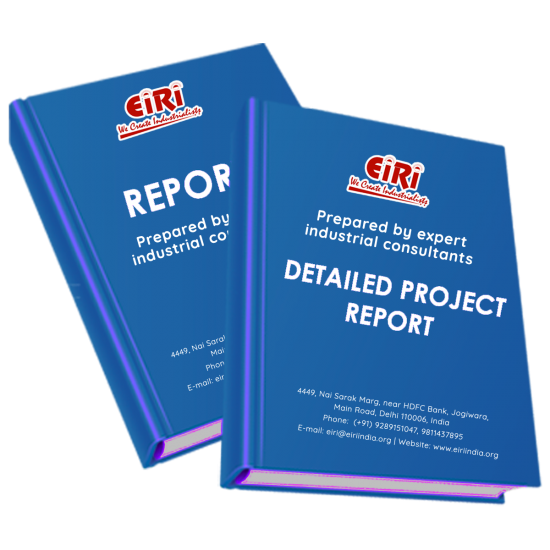
- More than 40 years of experience
- Managed by expert industrial consultants
- ISO 9001-2015 Certified
- Registered under MSME, UAM No: DL01E0012000
- 24/5 Research Support
Get your quesries resolved from an industry expert. Ask your queries before report or book purchase. - Custom Research Service
Speak to the our consultant to design an exclusive study to serve your research needs. - Quality Assurance
All reports are prepared by highly qualified consultants & verified by a panel of experts. - Information Security
Your personal & confidential information is safe & secure.
SILICONE OIL
[CODE NO.4147]
Polydimethylsiloxanes (PDMS) belong to a group of polymeric organosilicon compounds which are commonly referred to as "silicones". This report covers PDMS fluids of viscosities 10 to 100,000 centistokes (cs). These are clear, colourless and odourless liquids that have non detectable vapour pressure and are insoluble in water. PDMS will strongly sorb to particulate matter in aquatic systems.
PDMS have a wide range of industrial and domestic applications especially as antifoaming agents, in personal care products, as textile treatment, polishing or release agents. The worldwide production is estimated to be 150,000 tons a year.
Bulk amounts of PDMS waste from industrial use are predominantly recycled or incinerated. Used PDMS fluids contained in consumer waste and certain industrial waste streams are discharged diffusely and can be expected to enter waste water.
PDMS removal during wastewater treatment approaches 100% because of sorption onto sludge solids. Levels of PDMS in effluents range from non-detectable to ppb levels. Surface water levels of PDMS are generally below detection. Sewage sludge concentrations of up to several hundred ppm have been measured. Biodegradation on sludge solids during conventional aerobic and anaerobic treatment has not been observed. PDMS introduced into wastewater treatment systems will enter the environment as a component of sludge.
Sludge disposal include soil amendment, landfill, incineration and ocean disposal. PDMS introduced to the soil environment as a result of sludge amendment of soil is expected to abioticaly degrade to lower molecular siloxanols and possibly volatile oligomers. The breakdown products can bind to soil humic matter, can volatilise and can undergo photoinduced degradation or potentially biodegrade. The fate of PDMS in landfills has not been investigated but processes similar to those that occur in soil may also happen. PDMS combustion products include CO,, H,O, and amorphous silica.
PDMS will be sorbed to aquatic sediments as a result of small amounts discharged to surface waters from wastewater treatement plants or where ever waste water is discharged without treatment and where sludge ocean disposal is practiced. Sediment concentrations can range from trace levels to low ppm levels in areas of high industrial discharge. The fate of PDMS in sediments has not been fully investigated.
Bioconcentration of PDMS in aquatic organisms does not occur and bioaccumulation through the food chain in aquatic and terrestrial organisms has not been demonstrated.
No aquatic toxicity has been ascribed to PDMS.
PDMS of all viscosities display a very low acute toxicity via oral, dermal, inhalational, intraperitoneal, intradermal or subcutaneous routes of administration. Irritancy to the eye is low and no skin sensitising potential has been detected.
The potential routes of human exposure are by ingestion and dermal contact. PDMS are not absorbed through the skin, or from the gastrointestinal tract, from which it is rapidly excreted unchanged in the faeces.
Inhalation exposure normally does not occur due to the very low vapour pressure. Spray applications may give rise to the potential for aerosol exposure. The available toxicological data do not indicate any adverse effects.
Repeated dosage studies with PDMS of different viscosities demonstrated no significant adverse effects to a variety of mammalian species after oral, dermal or inhalative administration. In chronic studies, no adverse effects attributable to the treatment with PDMS were seen with rats, mice, dogs or monkeys.
In vitro genotoxicity studies with bacteria and mammalian cells provided no indications that POMS have a mutagenic or clastogenic potential.
Limited studies with rats and rabbits displayed no clear evidence of a teratogenic effect of PDMS. Oral administration of PDMS to rats prior to mating had no effects on fertility, gestation, peri- and postnatal development. Long term dermal treatment of male monkeys with PDMS did not affect their reproductive performance.
No suppressive or stimulating influence of PDMS on the immune system has been demonstrated in studies on mice. In a study on man there was no evidence of dermal absorption of PDMS after repeated applications.
Overall, the available data indicate that PDMS do not present a health hazard for man. The safety of PDMS has been recognised by their widespread uses in many applications involving human exposure (e.g. food additives, personal care products) for more than 30 years.
Polydimethylsiloxane (PDMS), also known as dimethylpolysiloxane or dimethicone, belongs to a group of polymeric organosilicon compounds that are commonly referred to as silicones. PDMS is the most widely used silicon-based organic polymer due to its versatility and properties leading to many applications.
It is particularly known for its unusual rheological (or flow) properties. PDMS is optically clear and, in general, inert, non-toxic, and non-flammable. It is one of several types of silicone oil (polymerized siloxane). Its applications range from contact lenses and medical devices to elastomers; it is also present in shampoos (as it makes hair shiny and slippery), food (antifoaming agent), caulking, lubricants and heat-resistant tiles.
Silicones are synthetic polymers having an inorganic skeleton of alternate silicone and oxygen atoms, the silicone valences not taken up by oxygen being saturated with organic grpoupe and other groups. They occupy an intermediate position between inorganic and organic compounds. Because of this dual nature they have many properties which have made them very useful in many applications. Silicones are produced in several forms including fluids, rubbers and resins. Silicones emulsions are formed from silicone fluids and water with the help of a suitable emulsifier, and find various applications.
The term silicone denotes a polymer with the structural formula (RnSiO(4-n)1/2)m where n is between 0 and 3 and m is 2 or more. It contains a repeating silicone oxygen chain having organic groups R, attached to a significant portion of the silicone atom by silicone carbon bonds. In commercial silicones most of the R groups are methyl, longer alkyl, fluoroalky, phenyl, vinyl and a few others. Silicone fluids the Si-O chain is unbanked.
Silicone fluids are generally, dimethyl polysiloxane, methyl hydrogen polysiloxane or silicones consisting of copolymers of dimethyl siloxane with methyl phenyl, methyl-hydrogen, diphenyl, methyl-alkyl and other siloxanes. Linear poly-dimethyl siloxanes or dimethyl polysiloxanes are the most important of all the silicones. These fluids with hexamethyl disiloxane. For relating low viscosity fluids are manufacured by reacting dimethyl silicone fluids the process is run for several hours at 180oC in glass lined kettles with acid chloride catalysts or at lower temperature with sulphuric acid. Alkaline catalysts are used for the production of high viscosity fluids or gums. Silicone fluids have m.wt. of 2000 to 15000 and viscosities from 10 to 10,000 cps.
Dimethyl silicone fluids are colourless, odorless and nontoxic and are resistant to oxidation and chemicals. They have good lubricating action. They reduce surface tension and have water repellent properties, together with foam inhibition. Inclusion of phenyl groups into the silicone structure increase their thermal and oxidative stability, while lowering the pour point. Thus methyl phenyl silicone fluids have higher viscosity, temperature coefficient and lower pour point and lower flash points than dimethyl silicone fluids of the same viscosity. Fluids with chlorinated phenyl groups attached to silicone, e.g. methyl alkyl fluids where alkyl is octyl to tetradecyl are good lubricants but have higher viscosity temperature coefficients and poorer oxidative stability than methyl fluids.
In general, the dimethyl silicone fluids are soluble in aliphatic and aromatic hydrocarbons and chlorinated hydrocarbons. Lower m. wt. fluids are more soluble than higher fluids. They are insoluble in methanol, ethanol, acetone, ethylene, gylcol, polyglycol ethers, gylcerol cyclohexanol and water. Methyl-phenyl silicones are more soluble than the corresponding dimethyl silicones.
COST ESTIMATION
Plant Capacity 34 MT/Day
Land & Building (12,000 sq.mt.) Rs. 10.23 Cr
Plant & Machinery Rs. 4.70 Cr
Working Capital for 2 Months Rs. 19.40 Cr
Total Capital Investment Rs. 34.80 Cr
Rate of Return 53%
Break Even Point 32%
- INTRODUCTION
- PROPERTIES AND CHARACTERISTICS
- IDENTITY
- PHYSICAL AND CHEMICAL PROPERTIES AND STABILITY
- PHYSICAL PROPERTIES
- TABLE: PHYSICAL DATA FOR PDMS
- WATER SOLUBILITY
- ADSORPTION AND DESORPTION
- CHEMICAL PROPERTIES AND STABILITY
- ANALYTICAL METHODS
- TRACE ANALYSIS IN ENVIRONMENTAL SAMPLES
- MECHANICAL PROPERTIES
- CHEMICAL COMPATIBILITY
- USES AND APPLICATION
- INDUSTRIAL APPLICATIONS WITH PREDOMINANTLY OCCUPATIONAL
- EXPOSURE
- INDUSTRIAL APPLICATIONS WITH POTENTIAL FOR OCCUPATIONAL
- AND CONSUMER EXPOSURE
- INDUSTRIAL APPLICATION WITH ENVIRONMENTAL EXPOSURE
- CONSUMER APPLICATIONS
- FOOD APPLICATIONS
- SURFACTANTS AND ANTIFOAMING AGENTS
- HYDRAULIC FLUIDS AND RELATED APPLICATIONS
- SOFT LITHOGRAPHY
- STEREO LITHOGRAPHY
- MEDICINE AND COSMETICS
- SKIN
- HAIR
- CONTACT LENSES
- FLEA TREATMENT FOR PETS
- FOODS
- CONDOM LUBRICANT
- SILICONE FLUIDS AND SILICONE EMULSION
- TYPES OF SILICONE FLUIDS
- SUPER LOW VISCOSITY SILICONE FLUIDS
- LOW VISCOSITY SILICONE FLUIDS
- STANDARD VISCOSITY SILICONE FLUIDS
- HIGH VISCOSITY SILICONE FLUIDS
- SUPER HIGH VISCOSITY SILICONE FLUIDS
- PURE SILICONE 350CST NSF HI FOOD GRADE
- THERE ARE BASICALLY TWO TYPES
- B.I.S. SPECIFICATION
- FIRST AID AND SAFE HANDLING OF SILICONE OIL
- FIRST AID
- FIRE FIGHTING
- MANAGEMENT OF SPILLAGE AND WASTE
- DISPOSAL
- TYPES OF SILICONE EMULSION
- DETAILS OF SILICONE FLUIDS
- ENVIRONMENTAL FATE AND EFFECTS:
- LOW HYDROGEN SILICONE OIL
- GENERAL PROPERTIES:
- PRODUCT FEATURES:
- APPLICATION:
- PACKAGING AND STORAGE:
- QUATERNIZED AMINO SILICONE OIL
- MAIN COMPOSITION:
- GENERAL PROPERTIES:
- PRODUCT FEATURES:
- APPLICATION:
- 1. PADDING PROCESS:
- 2. IMPREGNATION PROCESS:
- PACKAGING AND STORAGE:
- GLOBAL MARKET OVERVIEW OF SILICONE OIL
- PRESENT MANUFACTURERS/SUPPLIERS
- MANUFACTURING PROCESS OF POLY DIMETHYL SILOXANE (SILICONE OIL)
- POLY DIMETHYL SILOXANE AND ITS ASSAY
- SYNONYMS
- DEFINITION
- CHARACTERISTICS
- IDENTIFICATION
- PURITY
- TESTS
- PURITY TESTS
- VISCOSITY:
- CALIBRATION OF THE VISCOMETER
- METHOD OF ASSAY
- PRINCIPLE
- APPARATUS
- REAGENTS
- PROCEDURE
- WHERE
- FORMULATING, HANDLING & USE FOR SILICONE EMULSION
- USE AND HANDLING TIPS
- EMULSIFIER TYPES
- HOW SURFACTANTS WORK
- MICROBIAL CONTAMINATION – EMULSIONS
- APPLYING RELEASE AGENTS TO NEW MOLDS
- DILUTION LEVELS FOR RELEASE AGENTS
- RELEASE AGENTS FOR HIGH-TEMPERATURE APPLICATIONS
- RUST INHIBITORS FOR DILUTED RELEASE AGENT EMULSIONS
- APPLYING AMINO SILICONE SOFTENERS TO FABRIC
- FORMULATION OF SILICONE EMULSION
- USING DC-203 SILICONE FLUID
- FORMULATION OF SILICONE EMULSION
- OTHER FORMULATION OF SILICONE EMULSIONS
- SILICONE OIL EMULSION (MOULD RELEASING AGENT)
- FORMULATION - 1:-
- FORMULATION - 2:-
- FORMULATION OF SILICONE EMULSION (MOULD RELEASE AGENT)
- FOR RUBBER INDUSTRIES
- FOR PLASTIC INDUSTRIES
- FOR PU FOAM
- MORE FORMULATION OF SILICONE EMULSION
- PROCESS
- FORMULATION OF SILICONE EMULSION FOR PU
- FORMULATION NO. 1
- FORMULATION NO. 2
- ANTICAKING AGENTS
- PROCESS FLOW DIAGRAM FOR SILICONE EMULSION
- PACKAGING HANDLING AND REMOVAL METHOD OF SILICONE EMULSION
- MATERIAL SAFETY DATA SHEET FOR SILICONE EMULSION
- SECTION II: HAZARDS IDENTIFICATION
- EMERGENCY OVERVIEW
- POTENTIAL HEALTH EFFECTS:
- SECTION III: COMPOSITION/INFORMATION ON INGREDIENTS
- SECTION IV: FIRST AID MEASURES
- SECTION V: FIRE FIGHTING MEASURES
- SECTION VI: ACCIDENTAL RELEASE MEASURES
- SECTION VII: HANDLING AND STORAGE
- SECTION VIII: EXPOSURE CONTROLS/PERSONAL PROTECTION
- SECTION IX: PHYSICAL & CHEMICAL PROPERTIES
- SECTION X: STABILITY AND REACTIVITY
- SECTION XI: TOXICOLOGICAL INFORMATION
- SECTION XII: ECOLOGICAL INFORMATION
- SECTION XIII: DISPOSAL CONSIDERATIONS
- SECTION XIV: TRANSPORT INFORMATION
- SECTION XV: REGULATORY INFORMATION
- SECTION XVI: OTHER INFORMATION
- PRINCIPLES OF PLANT LAYOUT
- MAJOR PROVISIONS IN ROAD PLANNING FOR MULTIPURPOSE
- SERVICE ARE:
- PLANT LOCATION FACTORS
- PRIMARY FACTORS
- 1. RAW-MATERIAL SUPPLY:
- 2. MARKETS:
- 3. POWER AND FUEL SUPPLY:
- 4. WATER SUPPLY:
- 5. CLIMATE:
- 6. TRANSPORTATION:
- 7. WASTE DISPOSAL:
- 8. LABOR:
- 9. REGULATORY LAWS:
- 10. TAXES:
- 11. SITE CHARACTERISTICS:
- 12. COMMUNITY FACTORS:
- 13. VULNERABILITY TO WARTIME ATTACK:
- 14. FLOOD AND FIRE CONTROL:
- EXPLANATION OF TERMS USED IN THE PROJECT REPORT
- 1. DEPRECIATION:
- 2. FIXED ASSETS:
- 3. WORKING CAPITAL:
- 4. BREAK-EVEN POINT:
- 5. OTHER FIXED EXPENSES:
- 6. MARGIN MONEY:
- 7. TOTAL LOAD:
- 8. LAND AREA/MAN POWER RATIO:
- PROJECT IMPLEMENTATION SCHEDULES
- INTRODUCTION
- PROJECT HANDLING
- PROJECT SCHEDULING
- PROJECT CONSTRUCTION SCHEDULE
- TIME SCHEDULE
- SUPPLIERS OF RAW MATERIALS [GLOBAL]
- SUPPLIERS OF RAW MATERIALS
- SUPPLIERS OF SILICON OILS
- SUPPLIERS OF CARBOPOL
- SUPPLIERS OF PROPYLENE GLYCOL
- SUPPLIERS OF PACKAGING MATERIALS
- SUPPLIERS OF SODIUM HYDROXIDE
- SUPPLIERS OF PLANT AND MACHINERY (GLOBAL)
- SUPPLIERS OF PLANT AND MACHINERY
- SUPPLIERS OF COLLOID MILL
- SUPPLIERS OF STAINLESS STEEL STORAGE VESSEL
- SUPPLIERS OF FILTER
- SUPPLIERS OF PACKAGING MACHINES
- SUPPLIERS OF LABORATORY EQUIPMENT
APPENDIX – A:
01. PLANT ECONOMICS
02. LAND & BUILDING
03. PLANT AND MACHINERY
04. OTHER FIXED ASSESTS
05. FIXED CAPITAL
06. RAW MATERIAL
07. SALARY AND WAGES
08. UTILITIES AND OVERHEADS
09. TOTAL WORKING CAPITAL
10. TOTAL CAPITAL INVESTMENT
11. COST OF PRODUCTION
12. TURN OVER/ANNUM
13. BREAK EVEN POINT
14. RESOURCES FOR FINANCE
15. INSTALMENT PAYABLE IN 5 YEARS
16. DEPRECIATION CHART FOR 5 YEARS
17. PROFIT ANALYSIS FOR 5 YEARS
18. PROJECTED BALANCE SHEET FOR (5 YEARS)
How to Make Project Report?
Detailed Project Report (DPR) includes Present Market Position and Expected Future Demand, Technology, Manufacturing Process, Investment Opportunity, Plant Economics and Project Financials. comprehensive analysis from industry covering detailed reporting and evaluates the position of the industry by providing insights to the SWOT analysis of the industry.
Each report include Plant Capacity, requirement of Land & Building, Plant & Machinery, Flow Sheet Diagram, Raw Materials detail with suppliers list, Total Capital Investment along with detailed calculation on Rate of Return, Break-Even Analysis and Profitability Analysis. The report also provides a birds eye view of the global industry with details on projected market size and then progresses to evaluate the industry in detail.
We can prepare detailed project report on any industry as per your requirement.
We can also modify the project capacity and project cost as per your requirement. If you are planning to start a business, contact us today.
Detailed Project Report (DPR) gives you access to decisive data such as:
- Market growth drivers
- Factors limiting market growth
- Current market trends
- Market structure
- Key highlights
Overview of key market forces propelling and restraining market growth:
- Up-to-date analyses of market trends and technological improvements
- Pin-point analyses of market competition dynamics to offer you a competitive edge major competitors
- An array of graphics, BEP analysis of major industry segments
- Detailed analyses of industry trends
- A well-defined technological growth with an impact-analysis
- A clear understanding of the competitive landscape and key product segments
Need Customized Project Report?
- Ask for FREE project related details with our consultant/industry expert.
- Share your specific research requirements for customized project report.
- Request for due diligence and consumer centric studies.
- Still haven't found what you're looking for? Speak to our Custom Research Team
About Engineers India Research Institute:
Note: We can also prepare project report on any subject based on your requirement and country. If you need, we can modify the project capacity and project cost based on your requirement.
Our Clients
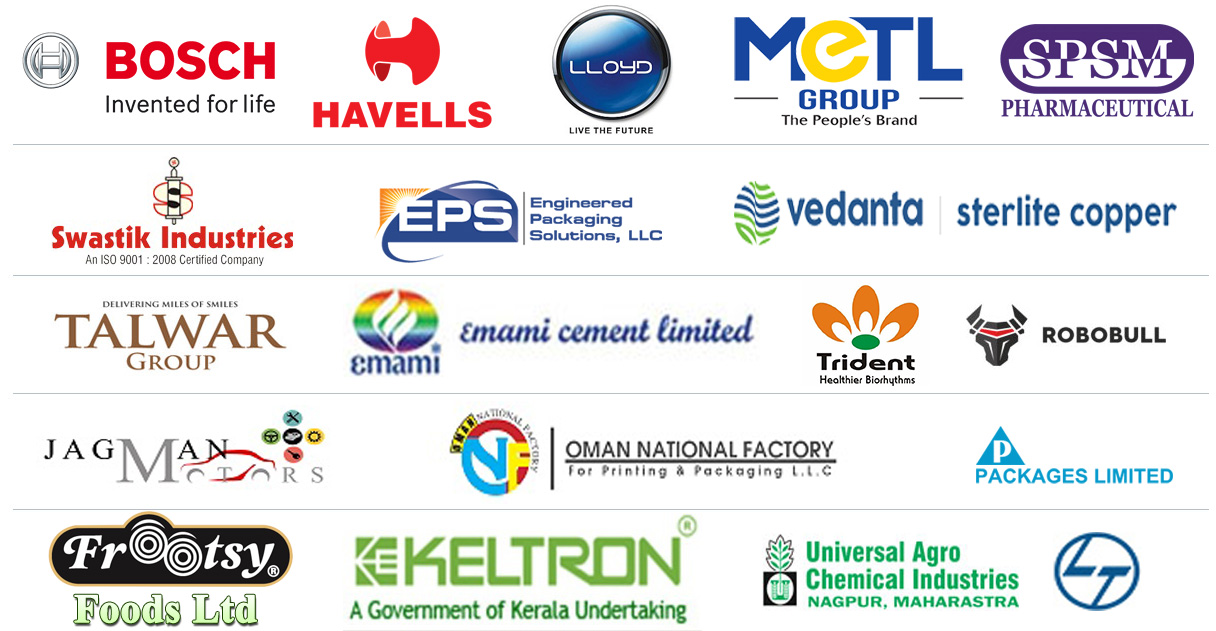
Our Approach
- Our research reports comprehensively cover Indian markets (can be modified as per your country), present investigation, standpoint and gauge for a time of five years*.
- The market conjectures are produced on the premise of optional research and are cross-accepted through associations with the business players
- We use dependable wellsprings of data and databases. What's more, data from such sources is handled by us and incorporated into the report
Why buy EIRI reports?
- Our project reports include detailed analysis that help to get industry Present Market Position and Expected Future Demand.
- Offer real analysis driving variables for the business and most recent business sector patterns in the business
- This report comprehends the present status of the business by clarifying a complete SWOT examination and investigation of the interest supply circumstance
- Report gives investigation and top to bottom money related correlation of real players/competitors
- The report gives gauges of key parameters which foresees the business execution