Detailed Project Report on thermo and vacuum forming of solid surfaces
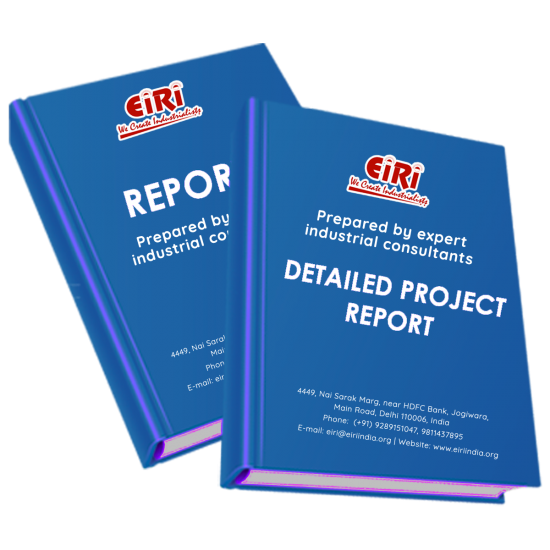
- More than 40 years of experience
- Managed by expert industrial consultants
- ISO 9001-2015 Certified
- Registered under MSME, UAM No: DL01E0012000
- 24/5 Research Support
Get your quesries resolved from an industry expert. Ask your queries before report or book purchase. - Custom Research Service
Speak to the our consultant to design an exclusive study to serve your research needs. - Quality Assurance
All reports are prepared by highly qualified consultants & verified by a panel of experts. - Information Security
Your personal & confidential information is safe & secure.
THERMO AND VACUUM FORMING OF SOLID SURFACES
[CODE NO.4181]
What is Vacuum Forming
Vacuum forming is a manufacturing method used to shape plastic materials. During the vacuum forming process, a sheet of plastic is heated and then pulled around a single mold using suction.
Vacuum forming is used for a wide range of manufacturing applications, ranging from small custom parts produced on desktop devices to large parts manufactured on automated industrial machinery.
Thermoforming is a manufacturing process where a sheet of plastic is heated to become pliable, then shaped or contoured using a mold, and trimmed to create a final part or product. Vacuum forming and pressure forming are both different types of thermoforming processes. The main difference between pressure forming and vacuum forming is the number of molds that are used.
Vacuum forming is the simplest type of plastic thermoforming that uses one mold and vacuum pressure to obtain the desired part geometry. It is ideal for parts that only need to be precisely formed on one side, such as contoured packaging for food or electronics.
There are two basic types of molds—male or positive (which are convex) and female or negative, which are concave. With male molds, the sheet of plastic is placed over the mold to contour the inside dimensions of the plastic part. With female molds, the thermoplastic sheet is placed inside the mold to form the outer dimensions of the part precisely.
Male mold, defined by positive or convex features
Female mold, defined by negative or concave features
In pressure forming, a heated sheet of plastic is pressed (hence the name) between two molds instead of being pulled into place around a single mold using suction. Pressure forming is ideal for manufacturing plastic parts or pieces that need to be more precisely shaped on both sides and/or require a deeper draw (they need to extend farther/deeper into a mold), such as appliance casings that need to look aesthetically pleasing on the exterior and snap into place or fit a precise size on the interior side.
How Does Vacuum Forming Work
The step-by-step vacuum forming process works as follows:
Clamp: A sheet of plastic is placed in an open frame and clamped into place.
Heat: The plastic sheet is softened using a heat source until it reaches the appropriate forming temperature and becomes pliable.
Vacuum: The framework containing the heated, pliable sheet of plastic is lowered over a mold and pulled into place via a vacuum on the other side of the mold. Female (or convex) molds need to have tiny holes drilled into crevices so that the vacuum can effectively pull the thermoplastic sheet into the appropriate form.
Cool: Once the plastic has been formed around/into the mold, it needs to cool. For larger pieces, fans and/or cool mist are sometimes used to speed up this step in the production cycle.
Release: After the plastic has cooled, it can be removed from the mold and released from the framework.
Trim: The completed part will need to be cut out of the excess material, and edges may need to be trimmed, sanded, or smoothed.
Vacuum forming is a relatively quick process with the heating and vacuuming steps typically taking only a few minutes. However, depending on the size and intricacy of the parts being manufactured, cooling, trimming, and creating molds can take considerably longer.
The Pros and Cons of Vacuum Forming
Many manufacturers, designers, and other professionals choose vacuum forming because it offers a blend of design flexibility at a relatively low cost compared to other manufacturing methods. The benefits of vacuum forming include:
Affordability
Particularly for smaller production runs (250-300 units per year), vacuum forming is typically more affordable than other manufacturing methods, such as plastic injection molding. The affordability of vacuum forming is largely due to the lower cost for tooling and prototyping. Depending on the surface area of the parts being manufactured and the dimensions of the clamp frame, tooling for injection molding can cost two to three times more than the amount for tooling for plastic thermoforming or vacuum forming.
Turnaround Time
Vacuum forming has a faster turnaround time than other traditional manufacturing methods because tooling can be made faster. Production time for vacuum forming tooling is typically half as long as the amount of time required producing tooling for injection molding. When 3D printers are used to create molds, turnaround time can be even faster. By increasing production process efficiency, vacuum forming enables businesses to get new designs in the hands of consumers faster.
Flexibility
Vacuum forming gives designers and manufacturers the flexibility to test out new designs and build prototypes without massive overhead or lag times. Molds can be made out of wood, aluminum, structural foam, or 3D printed plastics, so they can be changed out and/or modified more easily compared to other manufacturing processes.
Dick Teal used vacuum forming to test out prototypes of John Deere snowmobile parts in the late 1970s and early ’80s, largely because it made tooling inexpensive. In the book, John Deere Snowmobiles: Development, Production, Competition and Evolution, 1971-1983, the authors explain that “a win-win situation was created with lower cost parts and less investment in manufacturing tooling.”
Vacuum forming also gives designers the ability to offer more color options and customization to customers. This gives many businesses the freedom to offer one-of-a-kind designs and produce custom products, such as dental retainers, to clients at an affordable price point.
Manufacturing Sterile and Food-Grade Materials
Manufacturers often use vacuum forming to produce food-grade containers and parts for the medical industry because it is compatible with plastics that can be sterilized or kept free of contaminants. For example, high-density polyethylene (HDPE) is frequently used to vacuum form food storage containers.
HDPE’s resistance to acidic compounds makes it a viable material for vacuum forming cleaning product containers as well. Medical-grade plastics are used in vacuum forming to create parts that can withstand sterilization processes and meet stringent medical and/or pharmaceutical guidelines.
The Limitations of Vacuum Forming
While vacuum forming offers a number of benefits, it does have some limitations. Vacuum forming is only viable for parts with relatively thin walls and simple geometries. The finished parts may not have a consistent wall thickness, and concave parts with a deep draw are difficult to produce using vacuum forming.
In addition, while vacuum forming is often the most cost-effective choice for small to mid-range production quantities, other plastic manufacturing processes can be more affordable for very large production runs.
There are many different types of plastics that are used in vacuum forming and these are some of the more common ones:
1. Acrylonitrile Butadiene Styrene (ABS)
2. Acrylic – Perspex (PMMA)
3. Co-Polyester (PETG)
4. Polystyrene (HIPS)
5. Polycarbonate (PC/LEXAN/MAKROLON)
6. Polypropylene (PP)
7. Polyethelene (HDPE)
Each of the vacuum forming materials listed above has a set of characteristics which come from their atomic makeup, properties and range of additives. The ideal characteristics for vacuum forming materials are easy to form with a low forming temperature, thermal strength and good flow, high impact strength, and low levels of shrinkage when cooling.
Some of the materials are classed as “Hygroscopic”. These materials need to be pre-dried in an oven before forming, otherwise they absorb moisture. This excess moisture could pit the surface of the sheet and cause moisture blisters: ultimately resulting in a reject part.
CHARACTERSTICS
Attractive: Thermoformed plastic parts can be produced in a nearly unlimited variety of base materials, finishes, colors and textures.
Molded-In Styling Features: Logos, model designations, and other text and images can be formed right into the surface of the part. This eliminates the time and labor of adding these features, and they are a permanent feature of the part.
Durable yet Flexible: No material is more resilient than the thermoplastic resins that are available today. A vacuum formed part will not rust, it will not rot, it will not chip, and it can withstand considerable impact and return to its original shape!
Lightweight: Thermoformed plastic parts can be made from loll, density plastic with very thin walls to create a strong and durable, yet relatively lightweight part. Thermoformed plastic is considerably lighter—yet as stronger or even stronger—than molded fiberglass or sheet metal.
Less Expensive than Other Processes: Compared to sheet metal or handlayed fiberglass, thermoformed plastic parts can be much cheaper. And tooling for thermoforming is many times less expensive than tooling for other plastic processes, such as injection, rotational or blow molding.
Fast Time-to-Market: Tooling for thermoformed parts can be designed, engineered and fabricated in weeks, putting thermoformed parts into the assembly stream much faster than other processes.
Design Flexibility: The tooling used to thermoform parts can quickly and economically be modified to create different versions of a part for different configurations of a basic product.
Seamless: Thermoformed parts, panels and housings are elegantly simple, consisting of a single, seamless sheet of plastic formed to the exact dimensions, color, finish and texture needed by the OEM.
Thermoformed plastic is the logical upgrade from sheet metal or fiberglass when parts, panels, housings and enclosures are needed that must be durable and attractive, yet lightweight and affordable.
Upgrade from Sheet Metal: Manufacturers using sheet metal for product housings can affordably upgrade to thermoformed plastic to create a more contemporary exterior for their product.
Upgrade from Molded Fiberglass: Products with fiberglass exteriors can be significantly reduced in weight and cost by upgrading to thermoformed plastic.
Bezels and Fronts: Housings for CRTs, touch screens or liquid crystal, flat panel or plasma displays are excellent candidates for thermoformed plastic.
Consoles and Instrument Panels: A panel that requires precise openings for gauges and controls, but also needs to be attractive and rugged, can be cost-effectively produced via thermoforming.
Three-Dimensional Housings and Enclosures: Exteriors of business machines, office equipment, medical and diagnostic units, electrical and electronic devices, and other consumer and commercial products are excellent applications for thermoformed plastic.
Doors, Hatches, Covers and Movable Panels: Panels that face the user, and need to be durable and attractive, are ideal candidates for thermoforming. They can be affordably produced with indentations and cutouts for hinges, latches, handles, brackets and other hardware.
Panels with Undercuts and Returns: Parts with edges that turn under, or panels with sections that wrap back, can be produced through an advanced the process called “pressure forming”.
Twin-Wall Panels: When a double-walled panel is needed, it can be produced in a single, affordable process via what’s known as “twin-sheet thermoforming”.
WideRange of Colors and Finishes: Parts can be thermoformed with an inherent color in the resin, or the formed part can be painted and/or screen printed, and the surface can be hot stamped or given other finishes.
EMI/RFI Shielding: For electrical or electronic equipment that require housings with EMI and/or RFI shielding, it can be applied to required specifications in a secondary operation.
Insulation: Thermal or acoustic insulation can be affordably applied to the backside of a thermoformed part.
Thermoforming (or vacuum forming) is the process of heating a two-dimensional sheet of plastic, vacuum drawing it into a mold, and giving it an entirely new, permanent, three-dimensional form.
Read on to learn more about these 7 different types of thermoplastics used for vacuum forming, their individual properties and the specific applications to which they are most suited.
COST ESTIMATION
Plant Capacity 200 sq.ft./Day
Land & Building (650 sq.mt.) Rs. 1.06 Cr
Plant & Machinery Rs. 1.77 Cr
Working Capital for 2 Months Rs. 89 Lac
Total Capital Investment Rs. 3.82 Cr
Rate of Return 28%
Break Even Point 63%
- INTRODUCTION
- WHAT IS VACUUM FORMING
- MALE MOLD, DEFINED BY POSITIVE OR CONVEX FEATURES
- FEMALE MOLD, DEFINED BY NEGATIVE OR CONCAVE FEATURES
- HOW DOES VACUUM FORMING WORK
- THE PROS AND CONS OF VACUUM FORMING
- AFFORDABILITY
- TURNAROUND TIME
- FLEXIBILITY
- MANUFACTURING STERILE AND FOOD-GRADE MATERIALS
- THE LIMITATIONS OF VACUUM FORMING
- CHARACTERSTICS
- 1. ACRYLONITRILE BUTADIENE STYRENE (ABS)
- 2. ACRYLIC – PERSPEX (PMMA)
- 3. CO-POLYESTER (PETG)
- 4. POLYSTYRENE (HIPS)
- 5. POLYCARBONATE (PC / LEXAN / MAKROLON)
- 6. POLYPROPYLENE (PP)
- 7. POLYETHELENE (HDPE)
- USES AND APPLICATIONS
- AUTOMOTIVE AND TRANSPORTATION
- INDUSTRIAL
- PACKAGING AND DISPLAYS
- FOOD PACKAGING
- CONSUMER GOODS
- MEDICAL
- CUSTOM PARTS AND SPECIAL EFFECTS
- B.I.S. SPECIFICATION
- PROCESS FLOW DIAGRAM
- PRODUCTION PROCESS
- MAIN STEPS
- 1. MAKE THE MOULD
- 2. CLAMPING
- 3. HEATING
- 4. SHEET LEVEL
- 5. PRE-STRETCH
- 6. VACUUM
- 7. PLUG ASSIST
- 8. COOLING AND RELEASE
- 9. FINISHING AND TRIMMING
- TYPES OF VACUUM FORMING MACHINES
- MARKET OVERVIEW
- RECENT DEVELOPMENTS
- FURTHER KEY FINDINGS FROM THE REPORT SUGGEST:
- PLANT LAYOUT
- PRINCIPLES OF PLANT LAYOUT
- MAJOR PROVISIONS IN ROAD PLANNING FOR MULTIPURPOSE SERVICE ARE:
- PLANT LOCATION FACTORS
- 1. RAW-MATERIAL SUPPLY:
- 2. MARKETS:
- 3. POWER AND FUEL SUPPLY:
- 4. WATER SUPPLY:
- 5. CLIMATE:
- 6. TRANSPORTATION:
- 7. WASTE DISPOSAL:
- 8. LABOR:
- 9. REGULATORY LAWS:
- 10. TAXES:
- 11. SITE CHARACTERISTICS:
- 12. COMMUNITY FACTORS:
- 13. VULNERABILITY TO WARTIME ATTACK:
- 14. FLOOD AND FIRE CONTROL:
- EXPLANATION OF TERMS USED IN THE PROJECT REPORT
- 1. DEPRECIATION:
- 2. FIXED ASSETS:
- 3. WORKING CAPITAL:
- 4. BREAK-EVEN POINT:
- 5. OTHER FIXED EXPENSES:
- 6. MARGIN MONEY:
- 7. TOTAL LOAD:
- 8. LAND AREA/MAN POWER RATIO:
- PROJECT IMPLEMENTATION SCHEDULES
- INTRODUCTION
- PROJECT HANDLING
- PROJECT SCHEDULING
- PROJECT CONSTRUCTION SCHEDULE
- TIME SCHEDULE
- SUPPLIERS OF VACUUM THERMO FORMING PRODUCT
- SUPPLIERS OF RAW MATERIALS
- SUPPLIERS OF SOLID SURFACE MATERIAL
- SUPPLIERS OF PLANT MACHINES
- SUPPLIERS OF VACUUME THERMO FORMING MACHINES
- FOREIGN SUPPLIERS
- SUPPLIERS OF DG SETS
- SUPPLIERS OF EOT CRANE
- SUPPLIERS OF POWER TRANSFORMERS
- SUPPLIERS OF ELECTRICAL PANEL
- SUPPLIERS OF ELECTRIC MOTOR
- SUPPLIERS OF COOLING TOWER
- SUPPLIERS OF EFFULENT TREATMENT PLANT (ETP PLANT)
- SUPPLIERS OF AIR POLLUTION CONTROL EQUIPMENTS
- SUPPLIERS OF AIR CONDITIONING EQUIPMENTS
- SUPPLIERS OF AIR COMPRESSORS
- SUPPLIERS OF PLATFORM WEIGHING MACHINE
- SUPPLIERS OF MATERIAL HANDLING EQUIPMENTS
- SUPPLIERS OF FIRE FIGHTING EQUIPMENTS
- SUPPLIERS OF SHOT BLASTING MACHINE
- SUPPLIERS OF JIGS AND FIXTURE
- SUPPLIERS OF SUBMERSIBLE WATER PUMP
APPENDIX – A:
01. PLANT ECONOMICS
02. LAND & BUILDING
03. PLANT AND MACHINERY
04. OTHER FIXED ASSESTS
05. FIXED CAPITAL
06. RAW MATERIAL
07. SALARY AND WAGES
08. UTILITIES AND OVERHEADS
09. TOTAL WORKING CAPITAL
10. TOTAL CAPITAL INVESTMENT
11. COST OF PRODUCTION
12. TURN OVER/ANNUM
13. BREAK EVEN POINT
14. RESOURCES FOR FINANCE
15. INSTALMENT PAYABLE IN 5 YEARS
16. DEPRECIATION CHART FOR 5 YEARS
17. PROFIT ANALYSIS FOR 5 YEARS
18. PROJECTED BALANCE SHEET FOR (5 YEARS)
How to Make Project Report?
Detailed Project Report (DPR) includes Present Market Position and Expected Future Demand, Technology, Manufacturing Process, Investment Opportunity, Plant Economics and Project Financials. comprehensive analysis from industry covering detailed reporting and evaluates the position of the industry by providing insights to the SWOT analysis of the industry.
Each report include Plant Capacity, requirement of Land & Building, Plant & Machinery, Flow Sheet Diagram, Raw Materials detail with suppliers list, Total Capital Investment along with detailed calculation on Rate of Return, Break-Even Analysis and Profitability Analysis. The report also provides a birds eye view of the global industry with details on projected market size and then progresses to evaluate the industry in detail.
We can prepare detailed project report on any industry as per your requirement.
We can also modify the project capacity and project cost as per your requirement. If you are planning to start a business, contact us today.
Detailed Project Report (DPR) gives you access to decisive data such as:
- Market growth drivers
- Factors limiting market growth
- Current market trends
- Market structure
- Key highlights
Overview of key market forces propelling and restraining market growth:
- Up-to-date analyses of market trends and technological improvements
- Pin-point analyses of market competition dynamics to offer you a competitive edge major competitors
- An array of graphics, BEP analysis of major industry segments
- Detailed analyses of industry trends
- A well-defined technological growth with an impact-analysis
- A clear understanding of the competitive landscape and key product segments
Need Customized Project Report?
- Ask for FREE project related details with our consultant/industry expert.
- Share your specific research requirements for customized project report.
- Request for due diligence and consumer centric studies.
- Still haven't found what you're looking for? Speak to our Custom Research Team
About Engineers India Research Institute:
Note: We can also prepare project report on any subject based on your requirement and country. If you need, we can modify the project capacity and project cost based on your requirement.
Our Clients
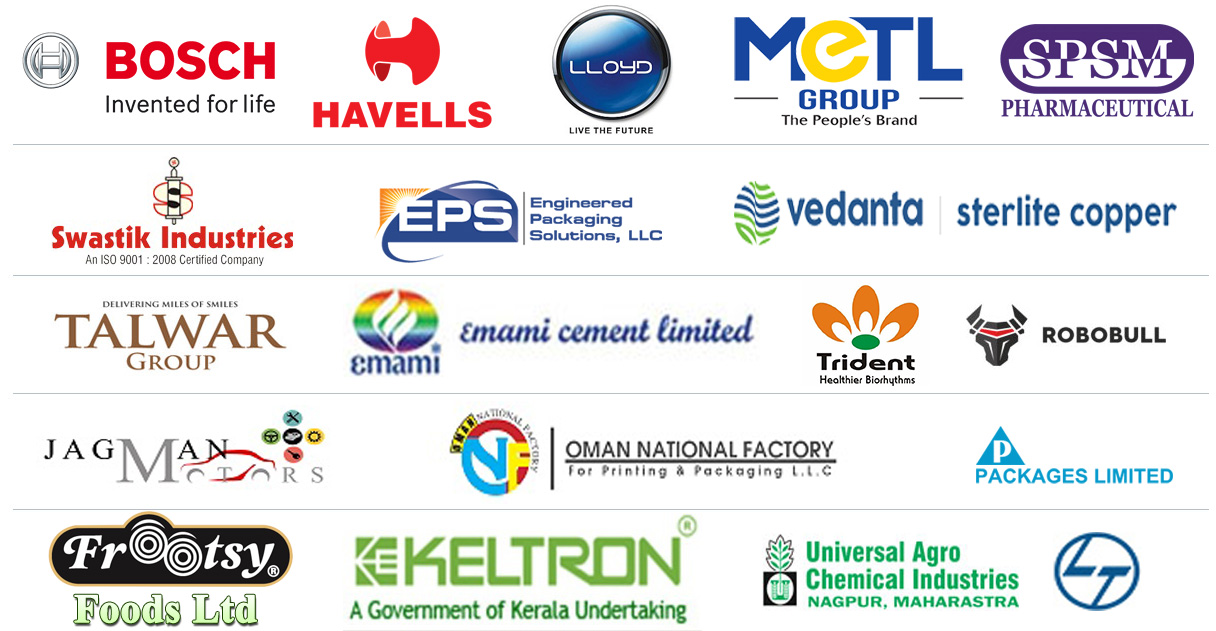
Our Approach
- Our research reports comprehensively cover Indian markets (can be modified as per your country), present investigation, standpoint and gauge for a time of five years*.
- The market conjectures are produced on the premise of optional research and are cross-accepted through associations with the business players
- We use dependable wellsprings of data and databases. What's more, data from such sources is handled by us and incorporated into the report
Why buy EIRI reports?
- Our project reports include detailed analysis that help to get industry Present Market Position and Expected Future Demand.
- Offer real analysis driving variables for the business and most recent business sector patterns in the business
- This report comprehends the present status of the business by clarifying a complete SWOT examination and investigation of the interest supply circumstance
- Report gives investigation and top to bottom money related correlation of real players/competitors
- The report gives gauges of key parameters which foresees the business execution