Detailed Project Report on vinyl acetate monomer from ethylene, acetic acid and oxygen
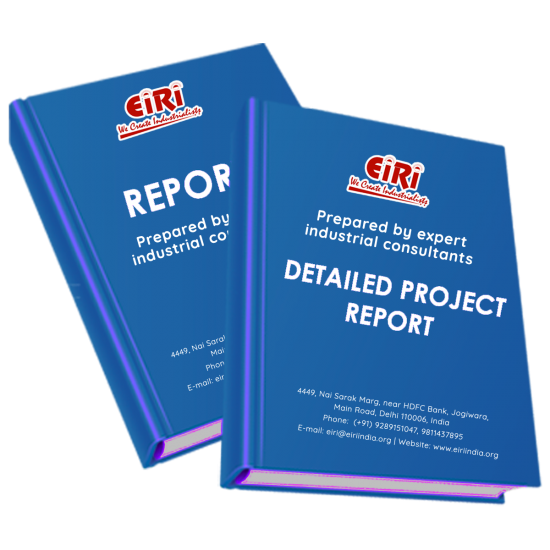
- More than 40 years of experience
- Managed by expert industrial consultants
- ISO 9001-2015 Certified
- Registered under MSME, UAM No: DL01E0012000
- 24/5 Research Support
Get your quesries resolved from an industry expert. Ask your queries before report or book purchase. - Custom Research Service
Speak to the our consultant to design an exclusive study to serve your research needs. - Quality Assurance
All reports are prepared by highly qualified consultants & verified by a panel of experts. - Information Security
Your personal & confidential information is safe & secure.
VINYL ACETATE MONOMER FROM ETHYLENE, ACETIC ACID AND OXYGEN
[CODE NO.4342]
Vinyl Acetate Monomer (also known as acetic acid ethenyl ester, acetic acid ethylene ether, acetoxyethene, 1-acetoxyethylene, ethenyl ethanoate, ethenyl acetate, and acetic acid vinyl ester) is a colourless mobile liquid with a pungent odour. It has the formula CH3COOCH=CH2 and is a key raw material in the production of chemicals which are then used to manufacture a wide variety of consumer and industrial products.
The main production method for vinyl acetate monomer is the reaction of ethylene and acetic acid with oxygen, in the presence of a palladium catalyst. The VAM is recovered by condensation and scrubbing and is then purified by distillation. A new manufacturing process, dubbed Leap, could offer large capital cost savings as a more efficient fluidised bed system replaces the fixed bed reactors currently in use.
The oldest means of manufacturing VAM is the addition of acetic acid to acetylene and this process is still used but not on a large scale.
Vinyl acetate monomer is stored in mild steel storage tanks and/or new or reconditioned steel drums and can be transported by bulk vessels or tank trucks. It has a specific gravity of 0.933 and a flash point of -8° C (closed cup) and is highly flammable. It should therefore be stored in a cool, dry, well-ventilated area that is free from the risk of ignition. For transportation purposes, it is classified as packing group II and hazard class 3 and it is an irritant.
Vinyl acetate is a colorless, flammable liquid that also has a characteristic smell that can quickly become irritating. This monomer is used principally in the production of polyvinyl acetate (PVAc) and other vinyl acetate co-polymers. Polyvinyl acetate is a precursor of polyvinilyc alcohol and polyvinyl acetate resins (PVA). Vinyl acetate is also copolymerized as a minor raw material for vinyl chloride and ethylene to form commercial polymers and acrylic fibers.
Vinyl acetate is completely soluble in organic liquids but not in water. At 20ºC a saturated solution of the monomer in water can contain between 2-2.4% of vinyl acetate, while a saturated water solution in vinyl acetate contains 1% of water. At 50ºC the solubility of the monomer in water increases in 0.1% in regards to 20ºC, while the solubility of water in vinyl acetate doubles at 50ºC.
The first available process for the synthesis of vinyl acetate was the acetoxilation of acetylene in gaseous form over a zinc acetate catalyst supported on carbon. This process consisted in the reaction of acetylene with acetic anhydride in a catalyzed medium and high temperature to form dietilene diacetate. This product passed through a cracking tower which in result gave as products acetic acid and vinyl acetate. 2 This type of reaction had a high production percentage (92-98%), but due to the increasing value of acetylene, new technologies and methodologies needed to be research in the 60's.
The process was modified until acetoxilation in a gaseous phase of ethylene over palladium and gold catalyst supported on silica gel was capable. The catalyst used potassium acetate to help the reaction in a temperature range of 423 ñ 463 K and a pressure range of 600 to 1,000 kPa. This is how ethylene acetoxilation with oxygen, acetic acid and Pd as a catalyst was developed. This process consists of two parts: a process in a homogeneous liquid phase that is used to produce 25% of the production of vinyl acetate, and another heterogeneous gaseous phase process used to produce the last 75% of the product.
The synthesis of vinyl acetate from ethylene, acetic acid and oxygen over a Palladium catalyst is a very important industrial process, but its selectivity is affected by the production of CO2 due to the combustion of the ethylene. Various factors affect the synthesis of vinyl acetate, like for example, the dispersion of Pd, partial pressures from the reactives that are the catalyst additives (near 80% if it is Pd/SiO2 and greater to 94% if it is Pd-Au/SiO2) and contact time. The investigation done by Han, H. F., et al. shows that the ethylene is the principal cause for the production of CO2 due to the fact that combustion kinetic does not change if the acetic acid is taken out of the medium.
The process that involves ethylene, acetic acid, oxygen over a Pd catalyst medium proves to be the best option to develop
Currently, the manufacturing process most widely used to produce vinyl acetate is the vapor phase ethylene process, an oxidative reaction in which ethylene is bubbled through acetic acid at 120°C in the presence of palladium chloride catalyst. Impurities found in the reaction have been reported at less than 1% (for one manufacturer) and have included the following: acetaldehyde, ethyl acetate, and methyl acetate. The vapor phase ethylene process was developed in 1967 to take advantage of ethylene as a cheaper feedstock than acetylene, and came into widespread use in the 1970s. By 1981, the vapor phase ethylene process accounted for 92% of U.S. production and the vapor phase acetylene process accounted for the remainder. Various firms in the United States, Japan, West Germany, and the United Kingdom have independently and/or jointly modified the vapor phase ethylene process by using different types of catalysts in the reaction. The catalyst is usually palladium or its salt, although salts of rhodium, gold, pla
tinum, ruthenium, vanadium, and iridium have also been used. The advantage of these processes is that the catalyst lasts longer and undergoes less corrosion.
A less important commercial manufacturing process for vinyl acetate involves the reaction between acetaldehyde and acetic anhydride. The intermediate species, ethylidene diacetate, undergoes pyrolytic cleavage to vinyl acetate and acetic acid. This process was used in the United States until the 1960s, and may still be in use at small plants in China, India, and Mexico. Vinyl. acetate can also be synthesized in high yields by reacting vinyl chloride with sodium acetate in solution at 50°-75°C, using palladium chloride as a catalyst.
COST ESTIMATION
Plant Capacity 667 MT/Day
Land & Building (15 Acres) Rs. 66.62 Cr
Plant & Machinery Rs. 399.35 Cr
Working Capital for 1 Month Rs. 108.12 Cr
Total Capital Investment Rs. 597.50 Cr
Rate of Return 62%
Break Even Point 33%
- INTRODUCTION
- PROPERTIES
- CONTAINERS & REGULATIONS:
- HAZARD:
- USES AND APPLICATION
- USE PATTERN:
- VINYL ACETATE MONOMER
- TECHNICAL DATA SHEET
- GENERAL DESCRIPTION
- TYPICAL PROPERTIES
- CRITICAL DATA
- TYPICAL PROPERTIES (1) (CONTINUED)
- GLOBAL MARKET POSITION OF VINYL ACETATE MONOMER
- MARKET OPPORTUNITY:
- MARKET TENDS
- MANUFACTURERS/SUPPLIERS OF VAM
- RAW MATERIAL
- TECHNOLOGY SOURCES:
- SEQUENCES IN VAM PROCESS
- ACETIC ACID EVAPORATION COLUMN
- REACTOR
- NON REACTIVE SUBSTANCE SEPARATOR
- ACETIC ACID RECOVERY COLUMN
- VAM REFINING COLUMN
- PROCESS FLOW DIAGRAM
- RAW MATERIAL CALCULATION
- REACTION
- RAW MATERIALS REQUIRED/MONTHS
- VAM PRODUCTION PROCESS
- PRODUCTION PROCESS USING ETHYLENE, ACETIC ACID AND OXYGEN
- REACTION SYSTEM
- THE REACTIONS THAT TAKE PLACE ARE:
- VAM DISTILLATION AND DEHYDRATION
- PRODUCTION DETAILS OF VINYL ACETATE MONOMER
- FIGURE: A SIMPLIFIED PROCESS SCHEME FOR THE PRODUCTION OF VINYL ACETATE MONOMER FROM A FATTY ACID OR TRIACYL
- GLYCERIDE-BASED OIL VIA NON-CATALYTIC CRACKING
- PROCESS DESCRIPTION OF VAM USING ETHYLENE, ACETIC ACID AND OXYGEN
- [MAIN REACTION]
- [SIDE REACTION]
- TABLE: MATERIALS IN THE VAM PLANT
- PROCESS CONSTRAINTS
- FIG.: PROCESS FLOW DIAGRAM OF THE VAM PLANT
- FIG.: START-UP OPERATION PROCEDURE OF THE VAM PLANT
- TECHNICAL ASPECT IN VAM MANUFACTURE
- FIGURE: VAM PRODUCTION PROCESS FLOW DIAGRAM.
- REACTION SYSTEM
- THE REACTIONS THAT TAKE PLACE ARE:
- THE RATE LAW FOR THIS REACTION (1) IS GIVEN BY:
- VAM DISTILLATION AND DEHYDRATION
- UNIT OPERATION IN VAM MANUFACTURE
- THE FOLLOWING REACTIONS TAKE PLACE:
- FIGURE: VINYL ACETATE MONOMER PROCESS FLOWSHEET
- 1. CHEMICAL PRODUCT & MANUFACTURER’S DETAILS
- 2. CHEMICAL IDENTIFICATION
- 3. HAZARD IDENTIFICATION & HEALTH HAZARD
- 4. FIRST AID MEASURES
- EYE:
- SKIN:
- INHALATION:
- INGESTION:
- 5. FIRE FIGHTING MEASURES
- EXTINGUISHING MEDIA:
- SPECIAL FIRE FIGHTING PROCEDURE:
- UNUSUAL FIRE AND EXPLOSION HAZARD:
- 6. ACCIDENTAL RELEASE MEASURES
- 7. HANDLING AND STORAGE
- 8. EXPOSURE CONTROLS/PERSONAL PROTECTION
- 9. PHYSIOCHEMICAL PROPERTIES & FIRE/ EXPLOSION HAZARD DATA
- 10. STABILITY AND REACTIVITY
- 11. TOXICOLOGICAL INFORMATION
- • ACUTE EFFECTS:
- • TARGET ORGANS:
- • TOXICITY:
- • CARCINOGENICITY:
- 12. ECOLOGICAL INFORMATION
- ECOTOXICITY:
- ENVIRONMENTAL FATE: THIS PRODUCT IS READILY BIODEGRADABLE
- 13. DISPOSAL CONSIDERATION
- 14. TRANSPORT INFORMATION
- 15. REGULATORY INFORMATION
- EUROPEAN INFORMATION
- EC NO: 203-545-4
- US INFORMATION
- PRINCIPLES OF PLANT LAYOUT
- STORAGE LAYOUT:
- EQUIPMENT LAYOUT:
- SAFETY:
- PLANT EXPANSION:
- FLOOR SPACE:
- UTILITIES SERVICING:
- BUILDING:
- MATERIAL-HANDLING EQUIPMENT:
- RAILROADS AND ROADS:
- MAJOR PROVISIONS IN ROAD PLANNING FOR MULTIPURPOSE SERVICE ARE:
- PLANT LOCATION FACTORS
- PRIMARY FACTORS
- 1. RAW-MATERIAL SUPPLY:
- 2. MARKETS:
- 3. POWER AND FUEL SUPPLY:
- 4. WATER SUPPLY:
- 5. CLIMATE:
- SPECIFIC FACTORS
- 6. TRANSPORTATION:
- A. AVAILABILITY OF VARIOUS SERVICES AND PROJECTED RATES
- 7. WASTE DISPOSAL:
- 8. LABOR:
- 9. REGULATORY LAWS:
- 10. TAXES:
- 11. SITE CHARACTERISTICS:
- 12. COMMUNITY FACTORS:
- 13. VULNERABILITY TO WARTIME ATTACK:
- 14. FLOOD AND FIRE CONTROL:
- EXPLANATION OF TERMS USED IN THE PROJECT REPORT
- 1. DEPRECIATION:
- 2. FIXED ASSETS:
- 3. WORKING CAPITAL:
- 4. BREAK-EVEN POINT:
- 5. OTHER FIXED EXPENSES:
- 6. MARGIN MONEY:
- 7. TOTAL LOAD:
- 8. LAND AREA/MAN POWER RATIO:
- PROJECT IMPLEMENTATION SCHEDULES
- INTRODUCTION
- PROJECT HANDLING
- PROJECT SCHEDULING
- PROJECT CONSTRUCTION SCHEDULE
- TIME SCHEDULE
- LICENCED CHEMICAL TECHNOLOGY AND SERVICES
- SUPPLIERS OF PLANT AND MACHINERY
- SUPPLIERS OF REACTORS
- SUPPLIERS OF CONDENSER
- SUPPLIERS OF BOILERS
- SUPPLIERS OF STORAGE TANK
- SUPPLIERS OF LABORATORY EQUIPMENTS
- SUPPLIERS OF HEAT EXCHANGER
- SUPPLIERS OF RAW MATERIALS
APPENDIX – A:
01. PLANT ECONOMICS
02. LAND & BUILDING
03. PLANT AND MACHINERY
04. OTHER FIXED ASSESTS
05. FIXED CAPITAL
06. RAW MATERIAL
07. SALARY AND WAGES
08. UTILITIES AND OVERHEADS
09. TOTAL WORKING CAPITAL
10. TOTAL CAPITAL INVESTMENT
11. COST OF PRODUCTION
12. TURN OVER/ANNUM
13. BREAK EVEN POINT
14. RESOURCES FOR FINANCE
15. INSTALMENT PAYABLE IN 5 YEARS
16. DEPRECIATION CHART FOR 5 YEARS
17. PROFIT ANALYSIS FOR 5 YEARS
18. PROJECTED BALANCE SHEET FOR (5 YEARS)
How to Make Project Report?
Detailed Project Report (DPR) includes Present Market Position and Expected Future Demand, Technology, Manufacturing Process, Investment Opportunity, Plant Economics and Project Financials. comprehensive analysis from industry covering detailed reporting and evaluates the position of the industry by providing insights to the SWOT analysis of the industry.
Each report include Plant Capacity, requirement of Land & Building, Plant & Machinery, Flow Sheet Diagram, Raw Materials detail with suppliers list, Total Capital Investment along with detailed calculation on Rate of Return, Break-Even Analysis and Profitability Analysis. The report also provides a birds eye view of the global industry with details on projected market size and then progresses to evaluate the industry in detail.
We can prepare detailed project report on any industry as per your requirement.
We can also modify the project capacity and project cost as per your requirement. If you are planning to start a business, contact us today.
Detailed Project Report (DPR) gives you access to decisive data such as:
- Market growth drivers
- Factors limiting market growth
- Current market trends
- Market structure
- Key highlights
Overview of key market forces propelling and restraining market growth:
- Up-to-date analyses of market trends and technological improvements
- Pin-point analyses of market competition dynamics to offer you a competitive edge major competitors
- An array of graphics, BEP analysis of major industry segments
- Detailed analyses of industry trends
- A well-defined technological growth with an impact-analysis
- A clear understanding of the competitive landscape and key product segments
Need Customized Project Report?
- Ask for FREE project related details with our consultant/industry expert.
- Share your specific research requirements for customized project report.
- Request for due diligence and consumer centric studies.
- Still haven't found what you're looking for? Speak to our Custom Research Team
About Engineers India Research Institute:
Note: We can also prepare project report on any subject based on your requirement and country. If you need, we can modify the project capacity and project cost based on your requirement.
Our Clients
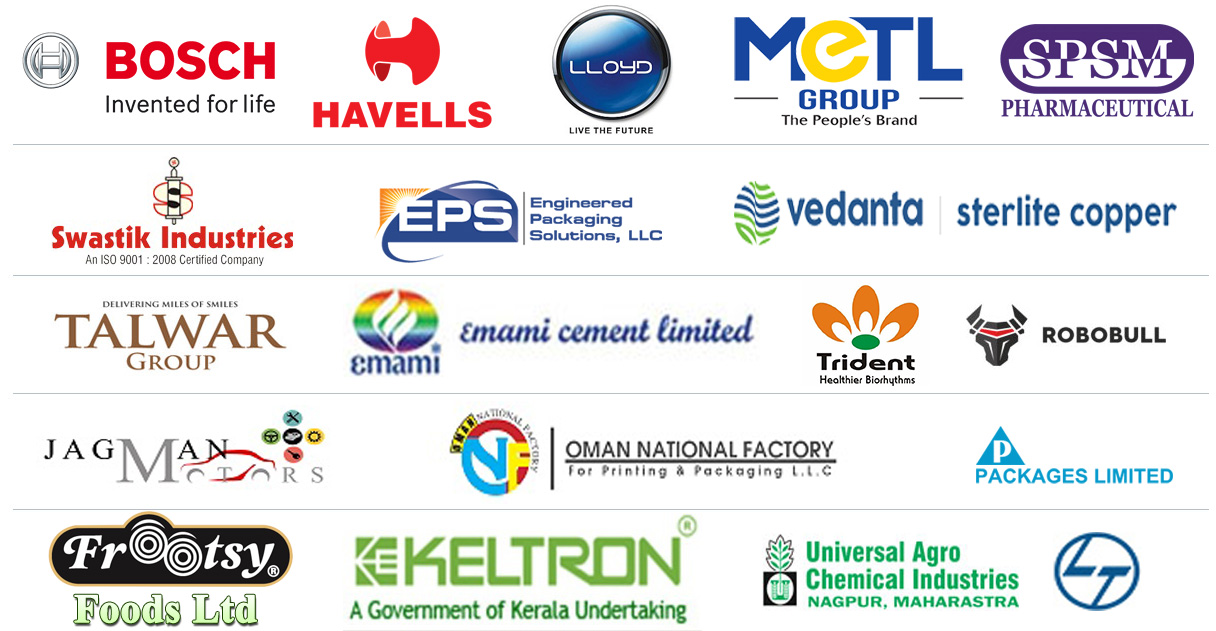
Our Approach
- Our research reports comprehensively cover Indian markets (can be modified as per your country), present investigation, standpoint and gauge for a time of five years*.
- The market conjectures are produced on the premise of optional research and are cross-accepted through associations with the business players
- We use dependable wellsprings of data and databases. What's more, data from such sources is handled by us and incorporated into the report
Why buy EIRI reports?
- Our project reports include detailed analysis that help to get industry Present Market Position and Expected Future Demand.
- Offer real analysis driving variables for the business and most recent business sector patterns in the business
- This report comprehends the present status of the business by clarifying a complete SWOT examination and investigation of the interest supply circumstance
- Report gives investigation and top to bottom money related correlation of real players/competitors
- The report gives gauges of key parameters which foresees the business execution