Detailed Project Report on manufacturing of flax (lainen yarn) from imported flax
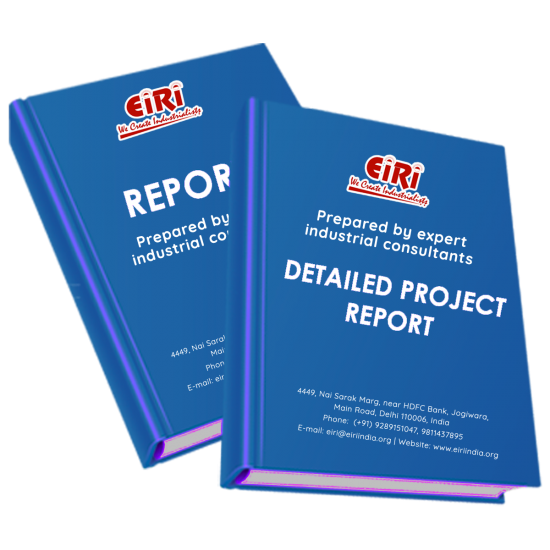
- More than 40 years of experience
- Managed by expert industrial consultants
- ISO 9001-2015 Certified
- Registered under MSME, UAM No: DL01E0012000
- 24/5 Research Support
Get your quesries resolved from an industry expert. Ask your queries before report or book purchase. - Custom Research Service
Speak to the our consultant to design an exclusive study to serve your research needs. - Quality Assurance
All reports are prepared by highly qualified consultants & verified by a panel of experts. - Information Security
Your personal & confidential information is safe & secure.
MANUFACTURING OF FLAX (LAINEN YARN) FROM IMPORTED FLAX [3644]
Linen yarn is spun from the long fibers found just behind the bark in the multi-layer stem of the flax plant (Linum usitatissimum). In order to retrieve the fibers from the plant, the woody stem and the inner pith (called pectin), which holds the fibers together in a clump, must be rotted away. The cellulose fiber from the stem is spinnable and is used in the production of linen thread, cordage, and twine. From linen thread or yarn, fine toweling and dress fabrics may be woven. Linen fabric is a popular choice for warm-weather clothing. It feels cool in the summer but appears crisp and fresh even in hot weather. Household linens truly made of linen become more supple and soft to the touch with use; thus, linen was once the bedsheet of choice. While the flax plant is not difficult to grow, it flourishes best in cool, humid climates and within moist, well-plowed soil. The process for separating the flax fibers from the plant's woody stock is laborious and painstaking and must be done in an area where labor is plentiful and relatively inexpensive. It is remarkable that while there is some mechanization to parts of the fiber preparation, some fiber preparation is still done by hand as it has been for centuries. This may be due to the care that must be taken with the fragile flax fibers inside the woody stalk, which might be adversely affected by mechanized processing. Flax remains under cultivation for linen fiber in a number of countries including Poland, Austria, Belgium, France, Germany, Denmark, the Netherlands, Italy, Spain, Switzerland, and the British Isles. However, the grade of fiber the plants yield in different parts of the world varies. Many believe that Belgium grows the finest-quality flax fibers in the world, with Scottish and Irish linen not far behind. There is no commercial production of linen fabric in any significant quantity in the United States except, perhaps, by individual hand spinners and hand weavers. Thus, the linen fabrics Americans use and wear are nearly all imported into the country from one of these flax-growing and weaving countries. Flax has been cultivated for its remarkable fiber, linen, for at least five millennia. The spinning and weaving of linen is depicted on wall paintings of ancient Egypt. As early as 3,000 B.C. , the fiber was processed into fine white fabric (540 threads to the inch—finer than anything woven today) and wrapped around the mummies of the ancient Egyptian pharaohs. Mentioned several times in the Bible, it has been used as a cool, comfortable fiber in the Middle East for centuries as well. Ancient Greeks and Romans greatly valued it as a commodity. Finnish traders are believed to have introduced flax to Northern Europe where it has been under cultivation for centuries. Both wool and linen were tremendously important fibers in the New World. Relatively easy to grow, American settlers were urged to plant a small plot of flax as early as the seventeenth century. While flax is easy to grow, settlers knew all too well the tedious chore of processing the woody stalks for its supple linen. Before the industrial revolution much sturdy, homemade clothing was woven from linen cultivated, processed, spun, dyed, woven, and sewn by hand. It may be argued that until the eighteenth century, linen was the most important textile in the world. By the late eighteenth century, cotton became the fiber that was most easily and inexpensively processed and woven in the mechanized British and New England textile mills. By the 1850s, linen production had virtually been abandoned in the United States because it was so much cheaper to buy the factory-made cotton. Some New Englanders of Scot or Irish background continued to cultivate some flax for processing into linen used for fancy domestic linens such as bedsheets, toweling, and decorative tableclothes as their ancestors had for centuries. However, most Americans abandoned the cultivation of the plant in this country and instead chose cheap cotton that was carded, spun, woven, and roller-printed for just pennies a yard. Thereafter and until recently, a different variety of flax plant was raised in this country not for its linen fibers but for its seeds which exude a useful vegetable oil known as linseed oil when pressed. All that is needed to turn flax fiber into linen, and then spin and weave the linen fibers into linen fabric is the cellulose flax fiber from the stem of the flax plant. The process for separating the fibers from the woody stalk can use either water or chemicals, but these are ultimately washed away and are not part of the finished material. The manufacture of linen yarn requires no special design processes. All that has to be determined prior to manufacturing is the thickness of the yarn to be spun. That will depend on the grade of linen in production and the demands of the customer. This is a European "flax wheel" used to spin flax into linen thread within the home. Folklore tells us that it was brought by Henry Ford's Irish grandmother to the New World; it was one of the few family keepsakes Ford had from his Irish ancestors. In fact, it was not unusual for the Scots or Irish to bring such wheels to this country. The British Isles have a long and proud linen tradition, and even decades after others abandoned linen production for cotton in the New World the Irish and Scots here tenaciously clung to their linen-making traditions. Ford's grandmother placed unspun flax on the tall, vertical, turned distaff and then push the treadle with her foot to power the wheel. The bobbin and flyer mounted horizontally in the center of the wheel would spin the flax and wind it on the bobbin at the same time. The rather small wheel below the bobbin required the spinner to treadle rafher fast to keep it moving and because of the small wheel this spinning wheel was not a popular style. It is lovely to look at, though, as this flax wheel is rather fancy, with inlaid bone or ivory set within the wheel. Some refer to this type of European spinning wheel as a "castle" or "parlor" wheel because of its lovely inlays and turnings.
COST ESTIMATION
Plant Capacity 6 MT/Day
Land & Building (5 Acre) Rs. 2.69 Cr
Plant & Machinery Rs. 5.50 Cr
Working Capital for 1 Month Rs. 9.51 Cr
Total Capital Investment Rs. 17.82 Cr
Rate of Return 35%
Break Even Point 41%
INTRODUCTION
PROPERTIES AND VARIETIES OF FLAX
FLAX IS OF TWO TYPES:-
FIBRE QUALITY CHARACTERISTICS
PHYSICAL PROPERTIES OF FLAX/LINEN FIBERS
CHEMICAL PROPERTIES OF FLAX/LINEN FIBERS
THE CHEMICAL COMPOSITION OF FLAX/LINEN FIBERS
CHARACTERISTICS OF FLAX/LINEN FIBER/FABRICS
PERFORMANCE SUMMARY OF FLAX/LINEN IN APPAREL FABRICS
CHARACTERISTICS OF FLAX FIBERS
FLAX/LINEN CLOTHING
USES AND APPLICATION
USES AND APPLICATION OF LINEN
OVERVIEW OF TEXTILE INDUSTRY IN INDIA
MARKET POSITION OF LINEN
LINEN YARN AND ITS ADVANTAGE
MANUFACTURING PROCESS OF FLAX (LINEN YARN)
FLAX SPINNING
TOW SPINNING
PROCESS FLOW DIAGRAM OF FLAX (LINEN YARN)
PRODUCTION METHOD OF LINEN
PROCESSING DETAILS OF LINEN FIBRE TO YARN
CERTAIN PRECAUTION TO BE OBSERVED WHILE SPINNING LINEN
IN ROTOR SPINNING
RESULTS AND DISCUSSION
PRODUCTION METHOD OF NATURAL FABRIC – LINEN
WET SPINNING OF FLAX YARN
PRINCIPLES OF PLANT LAYOUT
MAJOR PROVISIONS IN ROAD PLANNING FOR MULTIPURPOSE SERVICE ARE:
PLANT LOCATION FACTORS
PRIMARY FACTORS
EXPLANATION OF TERMS USED
IN THE PROJECT REPORT
PROJECT IMPLEMENTATION SCHEDULES
INTRODUCTION
PROJECT HANDLING
PROJECT SCHEDULING
PROJECT CONSTRUCTION SCHEDULE
TIME SCHEDULE
PLANT LAYOUT
SUPPLIERS OF RAW MATERIALS
SUPPLIERS OF PLANT AND MACHINERY
SUPPLIERS OF PLANT AND MACHINERY (INDIA)
SUPPLIERS OF LABORATORY EQUIPMENTS
SUPPLIERS OF D.G. SETS
SUPPLIERS OF INSTRUMENTATION & PROCESS CONTROL EQUIPMENTS
APPENDIX – A:
01. PLANT ECONOMICS
02. LAND & BUILDING
03. PLANT AND MACHINERY
04. OTHER FIXED ASSESTS
05. FIXED CAPITAL
06. RAW MATERIAL
07. SALARY AND WAGES
08. UTILITIES AND OVERHEADS
09. TOTAL WORKING CAPITAL
10. TOTAL CAPITAL INVESTMENT
11. COST OF PRODUCTION
12. TURN OVER/ANNUM
13. BREAK EVEN POINT
14. RESOURCES FOR FINANCE
15. INSTALMENT PAYABLE IN 5 YEARS
16. DEPRECIATION CHART FOR 5 YEARS
17. PROFIT ANALYSIS FOR 5 YEARS
18. PROJECTED BALANCE SHEET FOR (5 YEARS)
How to Make Project Report?
Detailed Project Report (DPR) includes Present Market Position and Expected Future Demand, Technology, Manufacturing Process, Investment Opportunity, Plant Economics and Project Financials. comprehensive analysis from industry covering detailed reporting and evaluates the position of the industry by providing insights to the SWOT analysis of the industry.
Each report include Plant Capacity, requirement of Land & Building, Plant & Machinery, Flow Sheet Diagram, Raw Materials detail with suppliers list, Total Capital Investment along with detailed calculation on Rate of Return, Break-Even Analysis and Profitability Analysis. The report also provides a birds eye view of the global industry with details on projected market size and then progresses to evaluate the industry in detail.
We can prepare detailed project report on any industry as per your requirement.
We can also modify the project capacity and project cost as per your requirement. If you are planning to start a business, contact us today.
Detailed Project Report (DPR) gives you access to decisive data such as:
- Market growth drivers
- Factors limiting market growth
- Current market trends
- Market structure
- Key highlights
Overview of key market forces propelling and restraining market growth:
- Up-to-date analyses of market trends and technological improvements
- Pin-point analyses of market competition dynamics to offer you a competitive edge major competitors
- An array of graphics, BEP analysis of major industry segments
- Detailed analyses of industry trends
- A well-defined technological growth with an impact-analysis
- A clear understanding of the competitive landscape and key product segments
Need Customized Project Report?
- Ask for FREE project related details with our consultant/industry expert.
- Share your specific research requirements for customized project report.
- Request for due diligence and consumer centric studies.
- Still haven't found what you're looking for? Speak to our Custom Research Team
About Engineers India Research Institute:
Our Approach
- Our research reports comprehensively cover Indian markets (can be modified as per your country), present investigation, standpoint and gauge for a time of five years*.
- The market conjectures are produced on the premise of optional research and are cross-accepted through associations with the business players
- We use dependable wellsprings of data and databases. What's more, data from such sources is handled by us and incorporated into the report
Why buy EIRI reports?
- Our project reports include detailed analysis that help to get industry Present Market Position and Expected Future Demand.
- Offer real analysis driving variables for the business and most recent business sector patterns in the business
- This report comprehends the present status of the business by clarifying a complete SWOT examination and investigation of the interest supply circumstance
- Report gives investigation and top to bottom money related correlation of real players/competitors
- The report gives gauges of key parameters which foresees the business execution