Detailed Project Report on Alloy Wheels Manufacturing Plant
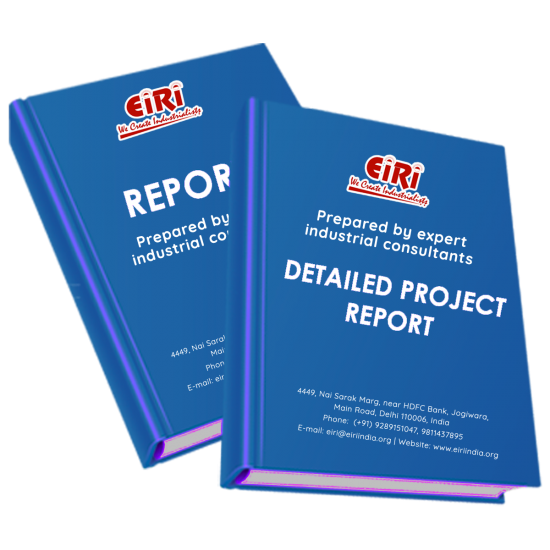
- More than 40 years of experience
- Managed by expert industrial consultants
- ISO 9001-2015 Certified
- Registered under MSME, UAM No: DL01E0012000
- 24/5 Research Support
Get your quesries resolved from an industry expert. Ask your queries before report or book purchase. - Custom Research Service
Speak to the our consultant to design an exclusive study to serve your research needs. - Quality Assurance
All reports are prepared by highly qualified consultants & verified by a panel of experts. - Information Security
Your personal & confidential information is safe & secure.
ALLOY WHEELS MANUFACTURING PLANT
[EIRI/EDPR/1455] J.C. 242,234
INTRODUCTION
The wheel is a mechanical device, which provides rotary motion by means of a disk or circular frame revolving on an axis. The steel wheel can be used in heavy load and traction services. The size and contour of a specific wheel design is based on the load it must carry and the space limitation of the equipment on which it is used. The contour of the wheel is normally composed compose of five parts: the hub, plate, rim, tread and flange. Classifications based on the service to which the wheels are applied are defined as: 1. Industrial car wheels for use on various cars such as those used in mining, railroads and transfer cars; 2. Crane truck wheels, for use in traveling, gantry, bridge cranes and floor-type changing and drawing machines; 3. Railroad freight car wheels, used according to their capacity and application, and 4. Heavy duty wheels, for use under railroad and electric railway cars, rapid transit passenger cars and locomotives. Most wheels for railway or industrial services are manufactured either by forming a solid block of metal by a sequence of hot forging and rolling operation, or by casting them directly from liquid metal into their final shapes. Mechanically speaking, steel castings are considered inferior to hot forging and rolling products. The casting of steel is, however, the most direct method of producing a given shape. For this reason, this method provides the basis for a key industry.
Today, the steel wheel has been partially replaced by the aluminum alloy wheel on vehicles, and this trend is expected to continue and become more popular in the near future. The changeover has already been introduced in General Motors and Ford in the USA, where new vehicles with aluminum alloy wheels are now rolling off production lines. There are at least four good reasons why wheel industries now prefer to use aluminum alloy to replace wrought steel: 1. Aluminum alloy wheels are more loads worthy. As 1kg of unsparing weight is generally equivalent to 10-15kgs of spring weight, and each 14’ aluminum alloy wheel is less than 2.5kgs., the four wheels under a typical car can handle loads of about 100-150kgs of extra weight (Unsprung weight means the weight put on the tire wheel, suspension or wheel area); 2. Excellent brake system. Aluminum thermal conductivity is about three times higher than that of steel This physical property gives the wheel better brake reliability and longer life than the steel wheel; 3. It is fuel-efficient. Basically, a 1kg loads decrease on a car will raise mileage 5-8 meters for every liter of gas used. In other words, fuel-efficiency is raised about 8.5% for every 10% reduction in car weight. The one-third to one-fifth work saved will surely prolong the service life of the car engine, and; 4. Suspension improvements. The suspension system of aluminum alloy wheels is capable of responding much more quickly to changing surfaces and road conditions. This increased traction can improve vehicle acceleration, maneuverability and brake performance. It is particularly noticeable while driving at high speeds or on rough roads.
It is apparent that more and more traction services and transportation industries are catching on to the idea of using aluminum alloy wheels to increase the quality of their products so as to seize more market share, Therefore, the establishment of a Taiwan supplied aluminum alloy wheel plant in any country would prove to be a wise investment.
The three basic elements of a wheel are the hub, the spokes and the rim. Sometimes these components will be one piece, sometimes two or three. The hub is the centre portion of the wheel and is the part where the wheel is attached to the suspension through the wheel carrier (or knuckle). The spokes radiate out from the hub and attach to the rim. The rim is the outer part of the wheel that holds the tyre.
Steel wheels are usually pressed from sheet metal and then welded together. They are still found on many cars since they are inexpensive, durable and flexible, but also heavy. In the beginning, aluminium wheels were generally marketed as optional add-ons or as part of a more expensive trim package. Today, however, aluminum wheels are found on more and more car models as standard equipment.
The use of aluminium wheels on passenger cars did not start primarily as a lightweighting measure. Aluminium wheels were introduced for styling reasons, to give upper class or flagships models a distinctive personal touch. The forged aluminium wheel was invented by ALCOA in 1948. In Europe, the success story of the aluminium wheel began with the development of the Porsche 911 in 1962. Porsche looked for a special wheel which should have outstanding qualities and present new dimensions, also visually. The forged aluminium wheel from OTTO FUCHS offered an attractive appearance. In addition, its low weight and thus the resulting reduction in the unsprung mass ensured also a superior ride quality. In the 1970s, cast aluminium wheels started to be factory-fitted to mass-produced cars.
Aluminium penetration in wheels was in the year 2000 for European vehicles about 30 to 35%, compared to largely more than 50% in USA and Japan. Today, about 50% of the vehicles produced on a worldwide basis use aluminium wheels, i.e. wheels are representing nearly 15% of the average aluminium content in passenger cars and light trucks. Some car manufacturers furnish over 80% of their production with aluminium wheels. In North America, the market penetration of aluminium wheels approaches 70%, in Japan about 60% and in Europe about 50%. Nowadays, the growth rate of the aluminium wheel market has slowed down, but the market volume is still increasing. The development of new, high strength steel grades and sophisticated manufacturing methods have enabled significant weight reductions for steel wheels and also allowed to meet the intricate aluminium wheel designs.
Wheels have to provide critical safety functions and must meet high standards of design, engineering and workmanship. Almost all modern aluminium wheels are made by one of two processes: casting and forging. Their performance is a direct result of the employed manufacturing technique. Whereas styling has been the main motivation for cast solutions, forged wheels are usually lighter and stronger, but also more expensive than cast wheels. Nevertheless, with proper attention to material quality and process control, cast aluminium wheels can be made to a high standard and provide many years of good service.
Today, cast aluminium wheels are most common with a market share of more than 80% in North America, more than 90% in Europe and close to 100% in Japan. In North America, the share of forged wheels is about 15%, in Europe only 5%. Increasing weight reduction requirements present a good chance for the further growth of forged aluminium wheels, despite their higher price. On the other hand, the light weighting trend has also led to the development and application of more sophisticated casting methods as well as the consideration of fabricated solutions made using sheets and/or extrusions. Many new developments are on the way to further reduce the weight of present aluminium wheels without sacrificing the styling advantages. An attractive compromise could consist of cast or forged central discs and subsequently assembled (mainly by welding) to extruded or rolled rims.
COST ESTIMATION
Plant Capacity 533.00 Nos/Day
Land & Building (8000 Sq.Mtr) Rs. 5.81 Cr.
Plant & Machinery Rs. 2.63 Cr.
W.C. for 2 Months Rs. 4.61 Cr
Total Capital Investment Rs. 13.54 Cr
Rate of Return 29%
Break Even Point 58%
CONTENTS
INTRODUCTION
PROPERTIES
B.I.S. SPECIFICATIONS
MARKET SURVEY
GLOBAL AUTOMOTIVE ALUMINIUM WHEEL INDUSTRY (2014-2016)
ALUMINUM WHEEL INDUSTRY TRANSFER TO ASIA ESPECIALLY TO CHINA
CHINA WHEEL-HISTORY AND DEVELOPMENT
MOST VALUABLE CLIENTS GROUP IN THE WORLD
PRODUCTION OF ALUMINUM ALLOY WHEEL IN INDIA
IMPORT AND EXPORT OF ALUMINUM ALLOY WHEEL
ALUMINUM WHEEL EXPORT DATA & EXPORT SHIPMENT
DATA OF INDIA (SEP 13 TO NOV 13)
ALUMINUM WHEEL IMPORT DATA & IMPORT STATISTICS IN INDIA (OCT 13 TO NOV 13)
INSTALLED CAPACITY, PRODUCTION & CAPACITY UTILIZATION OF ALUMINUM ALLOY WHEELS UPTO 2013
APPARENT CONSUMPTION OF ALUMINUM ALLOY WHEEL 2008 TO 2013
ESTIMATED DEMAND UPTO 2019-2020
DEMAND SUPPLY GAP 2019-2020
MANUFACTURING PROCESS
PROCESS FLOW DIAGRAM
PLANT LAYOUT
PRESENT MANUFACTURERS/ SUPPLIERS/ EXPORTERS/ DEALERS OF ALLOY WHEELS
SUPPLIERS OF RAW MATERIALS
SUPPLIERS OF PLANT & MACHINERY
SUPPLIERS/MANUFACTURERS OF ALLOY WHEEL
APPENDIX – A:
01. PLANT ECONOMICS
02. LAND & BUILDING
03. PLANT AND MACHINERY
04. OTHER FIXED ASSESTS
05. FIXED CAPITAL
06. RAW MATERIAL
07. SALARY AND WAGES
08. UTILITIES AND OVERHEADS
09. TOTAL WORKING CAPITAL
10. TOTAL CAPITAL INVESTMENT
11. COST OF PRODUCTION
12. TURN OVER/ANNUM
13. BREAK EVEN POINT
14. RESOURCES FOR FINANCE
15. INSTALMENT PAYABLE IN 5 YEARS
16. DEPRECIATION CHART FOR 5 YEARS
17. PROFIT ANALYSIS FOR 5 YEARS
18. PROJECTED BALANCE SHEET FOR (5 YEARS)
How to Make Project Report?
Detailed Project Report (DPR) includes Present Market Position and Expected Future Demand, Technology, Manufacturing Process, Investment Opportunity, Plant Economics and Project Financials. comprehensive analysis from industry covering detailed reporting and evaluates the position of the industry by providing insights to the SWOT analysis of the industry.
Each report include Plant Capacity, requirement of Land & Building, Plant & Machinery, Flow Sheet Diagram, Raw Materials detail with suppliers list, Total Capital Investment along with detailed calculation on Rate of Return, Break-Even Analysis and Profitability Analysis. The report also provides a birds eye view of the global industry with details on projected market size and then progresses to evaluate the industry in detail.
We can prepare detailed project report on any industry as per your requirement.
We can also modify the project capacity and project cost as per your requirement. If you are planning to start a business, contact us today.
Detailed Project Report (DPR) gives you access to decisive data such as:
- Market growth drivers
- Factors limiting market growth
- Current market trends
- Market structure
- Key highlights
Overview of key market forces propelling and restraining market growth:
- Up-to-date analyses of market trends and technological improvements
- Pin-point analyses of market competition dynamics to offer you a competitive edge major competitors
- An array of graphics, BEP analysis of major industry segments
- Detailed analyses of industry trends
- A well-defined technological growth with an impact-analysis
- A clear understanding of the competitive landscape and key product segments
Need Customized Project Report?
- Ask for FREE project related details with our consultant/industry expert.
- Share your specific research requirements for customized project report.
- Request for due diligence and consumer centric studies.
- Still haven't found what you're looking for? Speak to our Custom Research Team
About Engineers India Research Institute:
Note: We can also prepare project report on any subject based on your requirement and country. If you need, we can modify the project capacity and project cost based on your requirement.
Our Clients
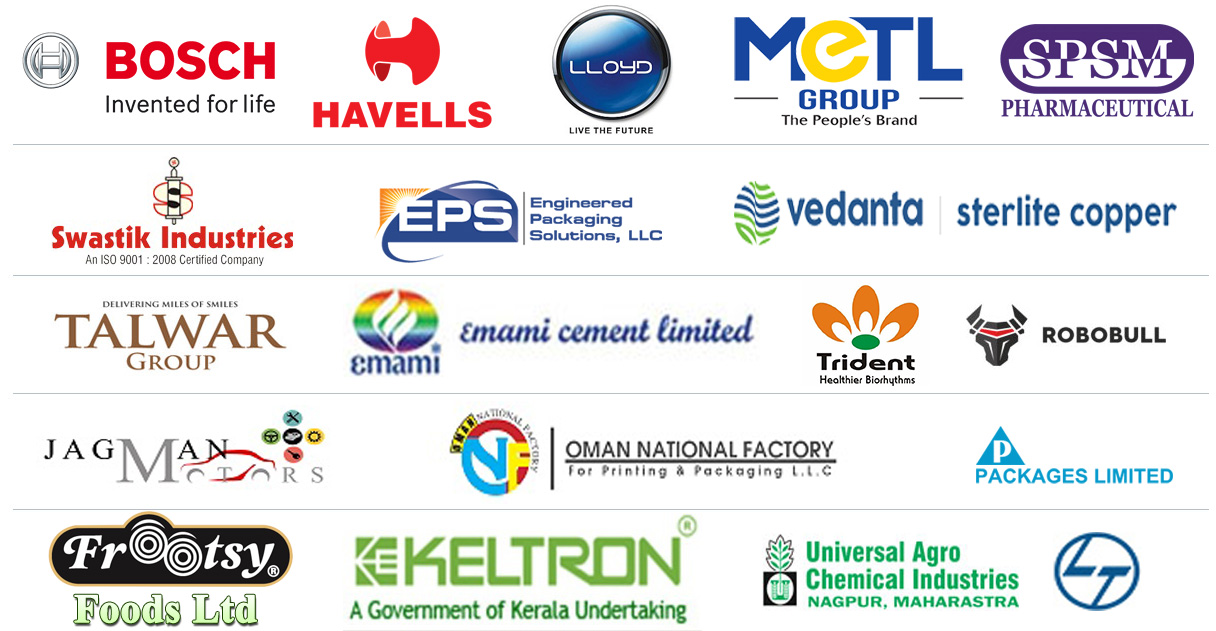
Our Approach
- Our research reports comprehensively cover Indian markets (can be modified as per your country), present investigation, standpoint and gauge for a time of five years*.
- The market conjectures are produced on the premise of optional research and are cross-accepted through associations with the business players
- We use dependable wellsprings of data and databases. What's more, data from such sources is handled by us and incorporated into the report
Why buy EIRI reports?
- Our project reports include detailed analysis that help to get industry Present Market Position and Expected Future Demand.
- Offer real analysis driving variables for the business and most recent business sector patterns in the business
- This report comprehends the present status of the business by clarifying a complete SWOT examination and investigation of the interest supply circumstance
- Report gives investigation and top to bottom money related correlation of real players/competitors
- The report gives gauges of key parameters which foresees the business execution