Detailed Project Report on cast iron casting manufacturing
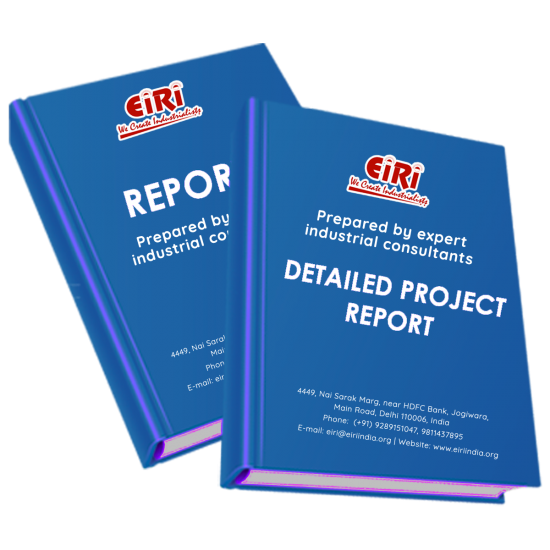
- More than 40 years of experience
- Managed by expert industrial consultants
- ISO 9001-2015 Certified
- Registered under MSME, UAM No: DL01E0012000
- 24/5 Research Support
Get your quesries resolved from an industry expert. Ask your queries before report or book purchase. - Custom Research Service
Speak to the our consultant to design an exclusive study to serve your research needs. - Quality Assurance
All reports are prepared by highly qualified consultants & verified by a panel of experts. - Information Security
Your personal & confidential information is safe & secure.
CAST IRON CASTING MANUFACTURING [3545]
Casting as an old technique is the quickest link between engineering drawing 2nd manufacturing. It provides us with the possibility of forming wide range of shapes with wide range of materials. Sand Casting is simply melting the metal and pouring it into a preformed cavity, called mold, allowing (the metal to solidify and then breaking up the mold to remove casting. In sand casting expandable molds are used. So for each casting operation you have to form a new mold. Basic Requirements for metal casting: 1. A mold cavity, 2. Melting process, 3. Pouring technique, 4. Solidification process, 5. Removal of casting, 6. Finishing draft allowance. Sand Casting is the most important and mostly used casting technique. To perform sand casting we have to form a pattern (a full sized model of the part), enlarged to account for shrinkage and machining allowances in the final casting. Materials used to make patterns include wood, plastics, aluminum, fiberglass, cast iron and some other metals. Wood is a common pattern material because it is easily worked into shape. Its disadvantages are that it tends to warp and the sand being compacted around it abrades it, thus limiting the number of times it can be reused (used for a small number castings). Metal patterns are more expensive to make, but they last much longer. For example aluminum is the most common metal to be used if" many castings are to be made by the same pattern. So selection of the appropriate pattern material depends to a large extent on the total quality of castings to be made. The size of the pattern depends upon the shrinkage during cooling and the Finishing allowance. Some special coating to prevent their destruction should coat patterns. Patterns have also some identifiers such as colors on them, each of which has different meaning that represent different treatments and requirements for the patterns. The color-coding for patterns in sand casting is as follows: 1) Red indicates that the surface of the material should be left as it is after casting. 2) Black indicates that the surface needs core and shows the position of the sand core. 3) Yellow indicates that the surface needs machining. The casting will be missing. To ensure that cores retain the correct arrangement core prints are placed into the mold. Some metal springs called densiments are placed into the mold Io provide uniform solidification of the metal throughout the mold. Nails are inserted into thin parts of the mold to reinforce them. After forming the mold cavity, an alcoholic liquid is sprayed aver the cope (The upper part of the mold) and heated with flames to harden and to dry the surface. Filling a metal box having two halves, which is called the flask forms mold. So mold is also made up of two halves, which is separated by a parting line. The reason for this is to remove the tasted part easier from the mold. The upper part of the mold is called the cope and the lower part called the drag. The cope and drag are prepared separately and when they are ready they unites and metal is poured into it through a canal called sprue, which transmits the molten metal via runner into the mold cavity. The runner should not be big because it will increase the amount of the waste metal. It should not be small because this enhances rapid solidification in the runner causing a blockage. At the bottom of the sprue there is a gap called well for the collection of the unwanted sand, which comes with the flowing metal. There is also a riser system, which acts as an inventory of molten metal when the mold cavity is fulfilled with the metal and feeds automatically the cavity of the part that we want to get. This system is essential because as the molten metal cools down it shrinks so the amount needed to replace the shrinked metal comes fom the riser itself eliminating shrinkage cavities. A casting may show microporosity. This can be eliminated with directional solidification either by incorporating a metal chill into the mold or by tapering the thinnest section of the runner. Chills are also used around thicker parts of the casting to provide uniform cooling of these parts with the thinner parts to prevent cracks. Chills, by this way, preserve the mechanical properties of the whole casting. The steel is melted in electric-arc furnaces. The advantage of electrical furnace, the scrap steel, which was used before (metal left In risers and runners) can be melted in these furnaces and used again. When the furnace reaches the suitable temperature, it is turned off. The molten metal is filed into the portable reservoir called table and then table is moved to just above of the mold and metal is poured into the mold's pouring basin. A powder is added to the mold's surface to prevent metal's rapid cooling during pouring. Another powder is sprayed aver the mold to form a blanket of inert gas to prevent the oxidation of the molten metal. The steel is melted in electric-arc furnaces. The advantage of electrical furnace, the scrap steel, which was used before (metal left in risers and runners) can be melted in these furnaces and used again. When the furnace reaches the suitable temperature, it is turned off. The molten metal is filed into the portable reservoir called label and then table is moved to just above of the mold and metal is poured into the mold's pouring basin. A powder is added to the mold's surface to prevent metal's rapid cooling during pouring. Another powder is sprayed aver the mold to form a blanket of Inert gas to prevent the oxidation of the molten metal. The completed casting is left for cooling and when it completely cools down the whole flask is taken to a vibrating platform to remove the casting from the mold. Excess parts are cut either by oxygen if the casting is of steel (hard), or by hammering if the casting is of cast iron (brittle).
COST ESTIMATION
Plant Capacity 25 MT/Day
Land & Building (96000 sq.ft.) Rs. 3.87 Cr
Plant & Machinery Rs. 3.24 Cr
Working Capital for 2 Months Rs. 5.23 Cr
Total Capital Investment Rs. 13 Cr
Rate of Return 23%
Break Even Point 60%
INTRODUCTION
SAND CASTING
BASIC REQUIREMENTS FOR METAL CASTING
AUTOMATED SAND CASTING IN FOUNDRIES
CAST IRON
TYPES OF CAST IRON
THE VARIOUS TYPES OF CAST IRON IN USE ARE DISCUSSED AS FOLLOWS
EFFECT OF IMPURITIES ON CAST IRON
USES & APPLICATIONS
B.I.S. SPECIFICATION
PROCESS FLOW CHART
MANUFACTURING PROCESS
(A) PIG IRON
(B) FERRO-ALLOYS
(C) COKE
(D) CAST IRON SCRAP
(2) SAND CASTING
ADVANTAGES OF SAND CASTING:
DISADVANTAGES OF SAND CASTING:
(A) PATTERNMAKING
(B) CORE MAKING
(C) MOLDING
(D) CLAMPING
(E) MELTING & POURING
(F) COOLING
(G) REMOVAL
(H) TRIMMING
(I) CLEANING
(J) QUALITY CONTROL
CASTING DEFECTS:
DEFECTS RELATED WITH SAND MOLDS:
INSPECTION METHODS:
CUPOLA FURNACE
STRUCTURE OF CUPOLA FURNACE:
(I) SHELL:
(II) FOUNDATION:
(III) CHARGING DOOR:
(IV) CHARGING PLATFORM:
(V) AIR BLOWER:
(VI) TUYERES:
(VII) VOLUME METER:
(VIII) TAP HOLE (MOLTEN METAL HOLE):
(IX) SLAG HOLE:
(X) CHIMNEY:
OPERATION OF CUPOLA FURNACE:
(I) PREPARATION OF CUPOLA:
(II) FIRING OF CUPOLA:
(III) CHARGING THE CUPOLA:
(IV) SOAKING OF IRON:
(V) STARTING THE AIR BLAST:
(VI) CLOSING THE CUPOLA:
ZONES OF CUPOLA FURNACE:
THE FOLLOWING ARE THE SIX IMPORTANT ZONES:
(I) WELL OR CRUCIBLE ZONE:
(II) COMBINATION ZONE:
(III) REDUCING ZONE:
(IV) MELTING ZONE:
(V) PREHEATING ZONE:
(VI) STACK ZONE:
CAPACITY OF CUPOLA FURNACE:
ADVANTAGES OF CUPOLA FURNACE:
LIMITATIONS OF CUPOLA FURNACE:
MARKET POSITION
GENERAL ECONOMIC SCENARIO
FORECASTS OF GROWTH BY LEADING INSTITUTIONS:
MAJOR FOUNDRY CLUSTERS:
MANPOWER:
AUTO SECTOR:
TOTAL PRODUCTION OF TRACTORS IN INDIA:
GLOBAL SCENARIO:
ROLE IN MANUFACTURING SECTOR:
PRODUCTION IN MILLION TONES:
EXPORTS IMPORT TRENDS:
SECTORWISE CONSUMPTION OF CASTING
IFMET 2018: INDIAN FOUNDRY INDUSTRY EXPECTS US 3 BN INVESTMENT
THE BRIGHT FUTURE OF CASTING IN INDIA
1. THE ‘MAKE IN INDIA’ CAMPAIGN
2. FOCUSING ON STRUCTURAL CHANGE SINCE 2015
3. THE BOOMING GROWTH OF THE AUTO INDUSTRY
4. MISCELLANEOUS OPPORTUNITIES
METAL CASTING MARKET
PLANT LAYOUT
MANUFACTURERS/SUPPLIERS OF CAST IRON CASTING
SUPPLIERS OF RAW MATERIALS
PIG IRON
CAST IRON SCRAP
FERRO SILICON
FERRO MANGANESE
SUPPLIERS OF COKE
FIRE CLAY
BENTONITE POWDER
COAL DUST
FIRE BRICKS
SOAP STONE
GRAPHITE POWDER
SILICA SAND
SUPPLIERS OF LIME STONE
SUPPLIERS OF PLANT AND MACHINERIES
COUPLA FURNACE
ALUMINIUM PATTERNS
INTENSIVE SAND MIXTURE AND MULLER
SAND SIEVING MACHINE
SQUEEZE MOLDING MACHINE
SHAKEOUT MACHINE
CORE SHOOTER MACHINE
DRYING OVEN
FOUNDRY TOOLS
MOLDING BOXES
METAL TESTING MACHINE
PRECISION MEASURING TOOLS
NDT INSPECTION EQUIPMENT
DRILLING, LATHE, TAPING MACHINES
GRINDING MACHINE
EOT CRANE
POWER TRANSFORMER
ELECTRICAL PANEL
ELECTRIC MOTOR
COOLING TOWER
EFFLUENT TREATMENT PLANT (ETP PLANT)
AIR POLLUTION CONTROL EQUIPMENTS
AIR CONDITIONING EQUIPMENTS
AIR COMPRESSORS
PLATFORM WEIGHING MACHINE
MATERIAL HANDLING EQUIPMENTS
FIRE FIGHTING EQUIPMENTS
SHOT BLASTING MACHINE
JIGS AND FIXTURE
SUBMERSIBLE WATER PUMP
APPENDIX –
01. PLANT ECONOMICS
02. LAND & BUILDING
03. PLANT AND MACHINERY
04. OTHER FIXED ASSESTS
05. FIXED CAPITAL
06. RAW MATERIAL
07. SALARY AND WAGES
08. UTILITIES AND OVERHEADS
09. TOTAL WORKING CAPITAL
10. TOTAL CAPITAL INVESTMENT
11. COST OF PRODUCTION
12. TURN OVER/ANNUM
13. BREAK EVEN POINT
14. RESOURCES FOR FINANCE
15. INSTALMENT PAYABLE IN 5 YEARS
16. DEPRECIATION CHART FOR 5 YEARS
17. PROFIT ANALYSIS FOR 5 YEARS
18. PROJECTED BALANCE SHEET FOR (5 YEARS)
How to Make Project Report?
Detailed Project Report (DPR) includes Present Market Position and Expected Future Demand, Technology, Manufacturing Process, Investment Opportunity, Plant Economics and Project Financials. comprehensive analysis from industry covering detailed reporting and evaluates the position of the industry by providing insights to the SWOT analysis of the industry.
Each report include Plant Capacity, requirement of Land & Building, Plant & Machinery, Flow Sheet Diagram, Raw Materials detail with suppliers list, Total Capital Investment along with detailed calculation on Rate of Return, Break-Even Analysis and Profitability Analysis. The report also provides a birds eye view of the global industry with details on projected market size and then progresses to evaluate the industry in detail.
We can prepare detailed project report on any industry as per your requirement.
We can also modify the project capacity and project cost as per your requirement. If you are planning to start a business, contact us today.
Detailed Project Report (DPR) gives you access to decisive data such as:
- Market growth drivers
- Factors limiting market growth
- Current market trends
- Market structure
- Key highlights
Overview of key market forces propelling and restraining market growth:
- Up-to-date analyses of market trends and technological improvements
- Pin-point analyses of market competition dynamics to offer you a competitive edge major competitors
- An array of graphics, BEP analysis of major industry segments
- Detailed analyses of industry trends
- A well-defined technological growth with an impact-analysis
- A clear understanding of the competitive landscape and key product segments
Need Customized Project Report?
- Ask for FREE project related details with our consultant/industry expert.
- Share your specific research requirements for customized project report.
- Request for due diligence and consumer centric studies.
- Still haven't found what you're looking for? Speak to our Custom Research Team
About Engineers India Research Institute:
Note: We can also prepare project report on any subject based on your requirement and country. If you need, we can modify the project capacity and project cost based on your requirement.
Our Clients
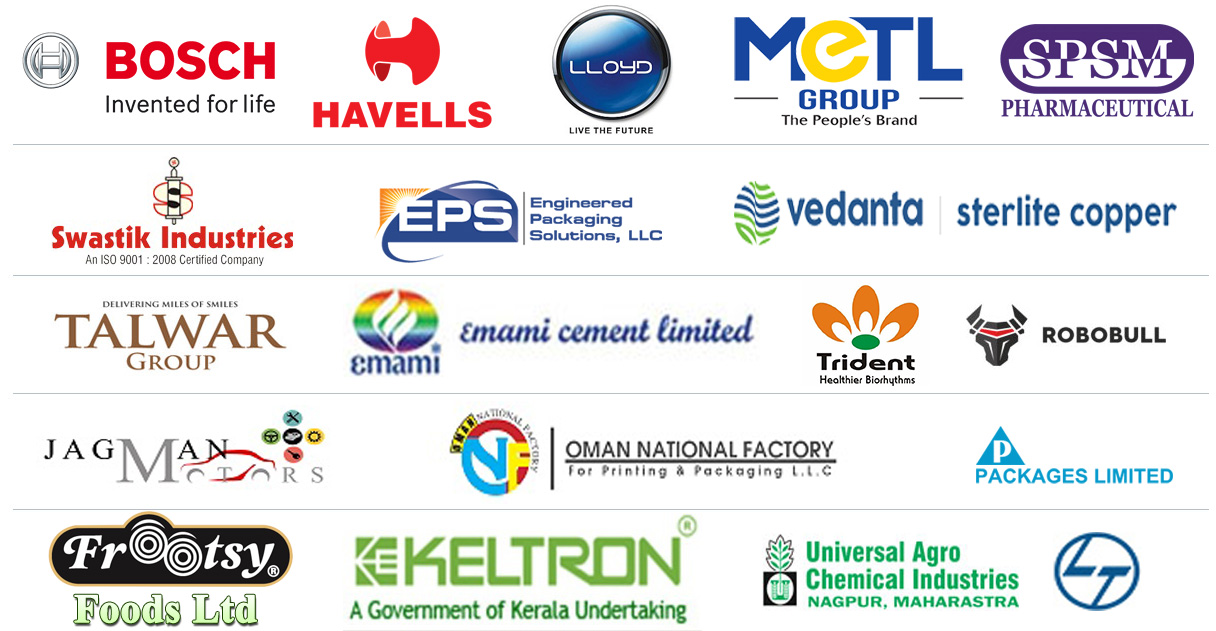
Our Approach
- Our research reports comprehensively cover Indian markets (can be modified as per your country), present investigation, standpoint and gauge for a time of five years*.
- The market conjectures are produced on the premise of optional research and are cross-accepted through associations with the business players
- We use dependable wellsprings of data and databases. What's more, data from such sources is handled by us and incorporated into the report
Why buy EIRI reports?
- Our project reports include detailed analysis that help to get industry Present Market Position and Expected Future Demand.
- Offer real analysis driving variables for the business and most recent business sector patterns in the business
- This report comprehends the present status of the business by clarifying a complete SWOT examination and investigation of the interest supply circumstance
- Report gives investigation and top to bottom money related correlation of real players/competitors
- The report gives gauges of key parameters which foresees the business execution