Modern Technology of Rolling Mill, Billets, Steel Wire, Galvanized Sheet, Forging and Castings (E-Book)

- More than 40 years of experience
- Managed by expert industrial consultants
- ISO 9001-2015 Certified
- Registered under MSME, UAM No: DL01E0012000
- 24/5 Research Support
Get your quesries resolved from an industry expert. Ask your queries before report or book purchase. - Custom Research Service
Speak to the our consultant to design an exclusive study to serve your research needs. - Quality Assurance
All reports are prepared by highly qualified consultants & verified by a panel of experts. - Information Security
Your personal & confidential information is safe & secure.
In metalworking, rolling is a metal forming process in which metal stock is passed through a pair of rolls. Rolling is classified according to the temperature of the metal rolled. If the temperature of the metal is above its recrystallization temperature, then the process is termed as hot rolling. If the temperature of the metal is below its recrystallization temperature, the process is termed as cold rolling. In terms of usage, hot rolling processes more tonnage than any other manufacturing process and cold rolling processes the most tonnage out of all cold working processes. There are many types of rolling processes, including flat rolling, foil rolling, ring rolling, roll bending, roll forming, profile rolling, and controlled
rolling.
Originally, a “billet” (from the French) was a note, commonly used in the 18th and early 19th centuries as a “billet of invitation.” A particular use of the word in this sense is to denote an order issued to a soldier entitling him to quarters with a certain person. From this meaning, the word billet came to be loosely used of the quarters thus obtained. Repeated petitions against the practice of billeting, starting in the 16th century, culminated in its outlawing in 1689 as an extension of a section of the Petition of Right 1628. During wartime, civilians who have been evacuated from a city in danger of attack are billetted in communal shelters or in the homes of individuals. The practice of billetting evacuees was widespread in Britain during World War II, particularly during the Blitz, when children and other non-essential persons in major cities were sent to rural areas for safety. In European countries since the formation of regular forces the Quartermaster was an occupation and a rank of the individuals responsible for provision of sleeping quarters as well as other provisions for regular time troops.
In general, galvanized sheet metal is mild (carbon) steel that is used for a ton of different things. This material is tough and strong, and it can be fairly easily worked (bent or formed) in a number of different ways to produce useful products (like HVAC ductwork, to name just one application). It lasts a long time, too, because the zinc coating (the galvanizing) inhibits corrosion quite well.
Forging or cold forming are metalforming processes. There is no melting and consequent solidification involved. Plastic deformation produces an increase in the number of dislocations resulting in a higher state of internal stress. Indeed, strain hardening is attributed to the interaction of dislocations with other dislocations and other barriers (such as grain boundaries). Simultaneously, the shape of primary crystals (dendrites) changes after plastic working of the metal. Dendrites are stretched in the direction of metal flow and
thus form fibers of increased strength along the direction of flow. Casting is a solidification process. Therefore, the microstructure can be finely tuned, such as grain structure, phase
transformations and precipitation. However, defects such as shrinkage porosity, cracks and segregation are also intimately linked to solidification. These defects can lead to lower mechanical properties. A subsequent heat treatment is often required to reduce residual stresses and optimize mechanical properties. The book cover various aspects on Rolling Mill, Billets, Steel Wire, Galvanised Sheet, Forging and Castings.
Chapter 1
Technology of Rolling Mills
- Types of Mills
- General Classification
- Arrangement of Mills
- Types of Roll Mountings
- Mill-Size Description
- Rolling-Mill Accessories
- Lead Spindle
- Mill Pinions
- The Bearings
- Roller Bearings
- Oil-Film Bearings
- Chock Bearings
- Arrangement of Chock Bearings
- Housings
- Guides and Guards
- Rolling-Mill Roll Design and Manufacture
- Principal Parts of Rolls
- Procedure in Designing
- Elements of Good Roll Design
- Casting of Rolling-Mill Rolls
- Steel Rolls
- Iron-Base Rolls
- Chill Rolls
- Grain-Iron Rolls
- Composite or Overflowed Rolls
- Ductile-Iron Rolls
- Mill Drives and Power Requirements
- Development of Main
- Mill Drives
- Power Requirements for Various Operations in
- the Production of Steel
- Factors Affecting Size and
- Type of Main-Drive Motors
- Types of Motors for Main Drives
- Synchronous Motors
- Squirrel-Cage Motors
- Wound-Rotor Induction Motors
- Direct-Current Motors
- Principle and Application of Flywheels
- Energy Stored in a Flywheel
- Amount of Energy Available for Regulation
- Acceleration and Retardation of the
- Wheel
- Induction-Motor
- Characteristics
- Motor Load Curves Various Means for
- Obtaining Adjustable
- Speeds
- Control of Two-Speed AC Motors
- AC-Motor Speed Control by Secondary
- Resistance
- Variable-Speed Controls for AC Motors
- Variable-Speed Controls for DC Motors
- Ward-Leonard Control
- Relay and Continuous-Feedback Systems
- Reversing-Mill Drives
- The Flywheel Motor-Generator Set
- Three-High Mill Drives
- Continuous-Mill Drives
- Wide-Hot-Strip Mills
- Tandem Cold-Reduction Mills
- Continuous Billet Mills
- Continuous Bar Mills
- Continuous Rod Mills
- Continuous Seamless Tube Mill
- Motor-Room Ventilation
- Auxiliary Drives
- Table Rollers
- Screw-Downs
- Manipulators and Side-Guards
- Blooming-Mill Shears
- Future Drives
- Automatic Control of Rolling Operations
- Principles of Process Control Systems
- Process Equations
- Instrumentation
- Control of Primary Rolling
- Plate-Mill Control
- Hot-Strip Mill Control
- Roughing
- Finishing
- Computer Control
- Control of Cold-Reduction Mills
- Reversing Mills
- Tandem Mills
- Computer Control
Chapter 2
Heating Steel for Hot Working
- Principles of Furnace Design
- Objectives and General Metallurgical Requirements
- Basic Elements of Furnaces
- Furnace Size and Capacity
- Furnace Type and Shape
- Thermal Efficiency
- Materials of Construction
- Soaking-Pit Furnaces
- Introductory Types of Soaking-Pit Furnaces
- Auxiliary Facilities
- Ingot Pit Cranes
- Cinder-Removal Facilities
- Objectives in Modern Soaking Pit Design
- Modern Heating Practices
- Operating Statistics
- Reheating Furnaces
- Furnace Types
- Pusher-Type Furnaces
- Walking-Beam-Type Furnaces
- Roller-Hearth Reheating Furnaces
- General Considerations in Furnace-Type Selection
- Batch-Type Furnaces
- Pusher-Type Furnaces
- Rotary-Hearth Furnaces
- Walking-Beam Furnaces
- Roller-Hearth Furnaces
- Operating Statistics
Chapter 3
Production of Steel Blooms, Slabs and Billets
- Introductory
- Production of Blooms and Slabs by Rolling
- General Features of Blooming and Slabbing Mills
- Primary-Mill Activities
- Two-High Reversing Mill
- Two-High Tandem Mill
- Three-High Mill
- Operating Units Comprising a Blooming Mill
- Rolling
- Shearing
- Combinations of Conventional-Type Mills for Special Purposes
- Two Two-High Reversing Mills in Tandem
- Tandem and Three-high Mill in Tandem
- Four-Stand and Five-Stand Tandem
- Mills in Tandem
- Design of Blooming-Slabbing Mill Roll Stands
- Stand Design
- Roll Design and Rolling Procedures
- Roll Design
- Effect of Pass Design on Rolling Procedures
- Convexity of Passes
- Depth of Passes Bearings
- Roll-Opening Indicators
- Roll-Changing Devices
- Cooling Water
- Manipulators
- Production of Billets by Rolling
- Development of the Billet Mill
- Types of Billet Mills
- Three-High Billet Mills
- Cross-Country Billet Mills
- Advantages of Cross-Country Mills
- Continuous Billet Mill
- Six-Stand Continuous Mill at Lorain Works
- The Four-Stand Continuous Mill at Lorain
- Hot-Scarfing Machines Roll Adjustment
- Shears
- Identification
- Continuous Casting of Blooms, Slabs and Billets
- Principles of Continuous Casting
- The Continuous Slab Caster at Gary Works
- Sequence of Operations
- Process Control
Chapter 4
Steel Plates Manufacture
- Plate-Mill Products
- Plate-Mill Operations
- Heating Slabs for Rolling
- Batch-Type Heating Furnaces
- Continuous-type Heating Furnaces
- Furnace Control
- Descaling
- Plate Rolling
- Plate Rolling Variables
- Bending of Rolls
- Roll Wear
- Temperature Variation
- Levelling (Flattening) Cooling
- Shearing and Cutting
- Identification, Inspection and Loading
- General Types of Plate Mills
- Two-High Pull-Over, Two-High Single-Stand
- Reversing and Three-High Plate Mills
- Three-High Plate Mills
- Four-High Reversing Plate Mills
- 160/210-Inch Plate Mill
- Slab Yard
- Slab-Reheating Furnaces
- Scalebreaker
- Slab Turnaround
- Four-High Reversing Stand Tables
- Transfer Tables and Cooling
- Levelers
- Plate-Inspection Turnovers
- Plate Marking Crop Shear
- Side Shears
- Dividing Shear
- Scrap Shears
- Inspection and Piling
- Flame Cutting
- Heat-Treating Facilities
- Roll Shop
- Lubrication
- 160-Inch Four-High Plate Mill at Homestead Works
- Tandem Mills
- Semi-continuous and Continuous Mills
- The 100-inch Semi-Continuous Plate Mill at Homestead Works
- No. 3 Shear Unit
- No. 4 Shear Unit
- Rotary Shear Line—No. 1 Shear Unit
- Continuous Normalizing Furnace
- No. 2 Shear Unit
- The 96-inch Four-High
- Continuous Plate Mill at South Works
- Universal Plate Mills
- The 30-Inch Universal Plate Mill
- Reheating Furnaces
- 30-Inch Universal Plate Mill Stand
- Rolling
- Hot Bed
- Finishing
- Heat-Treating Facilities for Steel Plates
- Types of Heat Treatment
- Furnaces for Heat Treating Plates
- Plate Heat-Treating
- Equipment at Homestead Works
- 160-Inch Mill Heat-Treating Facilities
- 100-Inch Mill Hardening-Tempering Furnace
- Car-Bottom Heat-Treating Furnaces
- Plate Heat-Treating Equipment
Chapter 5
Technology of Steel Wire and Steel Wire Products
- Principle Uses of Steel Wire Early Method of Manufacture Classification of Steel Wire
- Bases for Classification
- Kinds and Composition of Steel Used for Wire
- Wire Shapes
- Sizes of Wire
- Classification of Common Round Wire According to Size
- Surface Finishes of Wire
- Temper of Wire
- Rolling the Wire Rod
- The Wire Rod
- Types of Rod Mills
- The Continuous Rod Mill
- The Morgan Mill
- Modern Continuous Rod Mills
- Layouts for Rolling Small Billets
- The Looping Continuous Mill
- Layouts for Rolling 4-lnch by 4-lnch Billets
- Operation of Continuous Mills
- Outline of Wire-Drawing Processes
- Preparing the Rod for Drawing
- Drawing the Rod
- Draft, Drawing and Process Wire
- Dry Drawing and Wet Drawing
- Types of Wire
- Processes and Equipment for Preparing Rods
- and Wire for Drawing
- Importance of Cleaning
- Method of Cleaning
- Manner of Handling the Material
- Types of Cranes
- Construction of Tanks
- Arrangement of Tanks
- Concentration of Acid
- Temperature for Cleaning
- Time of Cleaning
- Rinsing
- Coatings
- Process for Lime Coating
- Coatings for Dry Drawing
- Phosphate Coatings
- Baking
- Wire-Drawing Equipment
- Dies
- Die Holes
- Diamond Dies
- The Block
- Drawing Machines
- Drawbench
- Bull Blocks
- Motor Blocks
- Continuous Machines
- Intermediate Machines
- Terminal Equipment
- Fine-Wire Machines
- Drawing Frames
- Auxiliary Equipment
- Pay-Off Reels
- Welders
- Safety Stop
- Pointers
- “Turks-Head” Shaped-Wire Drawing Machine
- Heating Effect in Wire Drawing
- Wire-Drawing Processes and Operations
- Effect of Drawing Upon Mechanical Properties
- The Cause of These Changes
- Limitations of Drawing
- Dry Drawing
- Uses of Low-Carbon Wire
- High-Carbon and Specialty Wire
- Wet Drawing
- Wet Drawing-Multiple Drafts
- Drawing Limits and Tolerances
- Special Finishing Operations
- Straightening and Cutting Wire Whirls
- Roll Straighteners
- Inspection and Testing
- Importance of Inspection
- Final Tests on Wires
- Defects in Wire
- Size and Shape
- Internal Defects
- Surface Defects
- Mechanical Properties
- Heat Treatment of Wire
- Importance and Purposes of Annealing
- Annealing for Definite Structures
- Sizes of Grains
- Time and Temperature for Annealing
- Methods of Annealing Wire
- Controlled-Atmosphere Annealing
- Salt-Bath Annealing Patenting
- Metals of Patenting
- Properties of Patented Wire
- Hardening and Tempering
- Methods of Hardening and Tempering Wire
- Protective Metallic Coatings
- Kinds of Coatings
- Wire Galvanizing
- Advantages of Galvanizing
- Methods of Galvanizing
- Processes Preliminary to Hot Galvanizing
- Apparatus for Hot Galvanizing
- Wiping the Wire
- Cooling the Coated Wire
- Coiling the Wire
- Some Features of the Operations for Hot Galvanizing
- The Structure of the Zinc Coat Electrogalvanizing
- Operation of the Process
- Factors in Controlling the Thickness of the Coat
- Tests for Galvanized Coatings
- Wire Tinning
- Aluminum Coatings
- Typical Finished Wires for Manufacturing Purposes
- Common Wires
- Bright Basic Wire or Bright Hard Basic Wire Medium Classifications
- Annealed Wires
- Cold-Heading Wire
- Liquor-Finished Fine and Weaving Wire
- Welding Wire
- Brush Wire
- High-Carbon or Special Wires
- Rope Wire
- Music Wire
- Piano Wire
- Bronze Finish Tire
- Bead Wire
- Valve Spring Wire
- Tempered Wire
- Other Special Wires
- Stainless-Steel Wire
- Flat Wire
- Some Fabricated Steel-Wire Products
- Importance of Fabricated Wire Products
- Wire Nails
- Nail Machines
- Feeding
- Pinching
- Cutting
- Expelling
- Cleaning and Packing
- Wire Fence
- Woven-Wire Fence
- Barbed-Wire Fence
- Concrete Reinforcement
- Prestressed Concrete
- Bale Ties
- Wire Rope
- Fabrication of Wire Rope
- Stranding
- Laying or Closing
- Types of Wire Rope
- Wire Springs
- Spring Terms
- Bluing
- Tested Spring
- Scale Testing
- Pitch
- Active and Inactive Coils
- Initial Tension
- Bridge Wire
Chapter 6
Manufacturing Technology of Hot-Strip Mill Products
- Classification of Flat-Rolled Steel Products
- Sources and Types of Steel for Sheet, Strip and Tin Plates
- Chemical Compositions
- Steelmaking Processes Slabs
- Rolling Slabs from Ingots
- Continuous Casting of Slabs
- Bottom-Pressure Pouring of Slabs
- Continuous Hot-Strip Mills
- Development and Output
- General Arrangement of Modern Mills
- Control of Finished Product Quality
- An 84-inch Continuous Hot-Strip Mill
- Slab Conditioning and Storage Areas
- Slab-Heating Furnaces
- Runout Table
- Coilers
- Lubricating Systems
- Motor Room
- Metallurgy of Hot-Rolled Strip
- Hand Hot Mills
- Development
- Process
- Oxide Removal (Pickling and Shot Blasting)
- Necessity for Removal
- Types of Oxide
- Principles of Pickling Inhibitors
- Hydrochloric-Acid Pickling
- Spent Hydrochloric-Acid Disposal
- Continuous Pickling Lines
- Batch Pickling
- Shot Blasting
- Finishing of Hot-Strip Mill Products
- Temper Rolling (Skin Passing)
- Levelling (Flattening)
- Slitting
- Shearing
- Heat Treating
Chapter 7
Production Process of Cold-Reduced Flat-Rolled Products
- Cold-Finished Flat-Rolled Products
- Cold-Finished Flat Bars
- Cold-Rolled Carbon- Steel Strip Temper
- Stainless Cold-rolled Strip Steel Finishes
- Cold Rolled Carbon Spring Steel
- Temper
- Cold-Rolled Carbon-Steel Sheets
- Black Plate
- Principles of Cold Reduction
- Sequence of Operations in Cold Reduction
- Roll Arrangement for Cold Reduction
- Mill Layouts
- Four-High Tandem Mills
- Four-High Reversing Mills
- Two-High Cold Mills
- Disposition of Product
- Cold-Reduced Product for Strip
- Cold-Reduced Product for Sheets
- Cold-Reduced Product for Tin Plate
- Cleaning of Cold-Reduced Steel
- Heat Treatment of Cold-Reduced Steel
- Purposes and Types of Heat Treatment
- Effects of Heat
- Treatment on
- Microstructure
- Box Annealing
- Normalizing
- Continuous Annealing
- Heat-Treating Equipment
- and Practices
- Box Annealing
- Equipment
- Box Annealing
- Practices
- Open-Coil Annealing
- Normalizing
- Continuous Annealing
- Temper Rolling
- Shearing, Side Trimming, Slitting and Leveling
- Shearing to Length
- Side Trimming and Slitting
Chapter 8
Manufacture of Galvanized Sheet and Strip Uses of Galvanized Sheet and Strip
- Factors Influencing Effectiveness of Galvanized Coatings
- Coating Weight and Gage Requirements
- Metallurgical Features of the Hot-Dip Galvanizing Processes
- Coating Metal Used In Hot-Dip Galvanizing
- Steels Used for Hot-Dip Galvanizing
- Mill Treatment of Steel Prior to Hot-Dip Galvanizing
- Special Finishes
- Hot-Dip Sheet Galvanizing
- Pickling for Sheet Galvanizing
- Equipment for Sheet Galvanizing
- General Arrangement and Operation of a Sheet-Galvanizing Line
- Continuous (Strip) Hot-Dip Galvanizing
- General Arrangement and Operation of Continuous
- Galvanizing Lines
- Testing Galvanized Sheets
Chapter 9
Manufacture of Heavy Press Forgings
- Heating for Forging
- Rate of Heating
- Forging Temperature
- Handling Equipment
- Open Dies for Forging
- Principal Forging Operations
- Examples of Forging Procedure
- Cooling after Forging
- Heat Treatment of Forgings
- Car-Bottom Furnaces
- Vertical Furnaces
- Quenching Facilities
Chapter 10
Castings - Steel and Iron
- Steel Castings
- Casting Compared with Other Forms of Shaping Steel
- Composition and Mechanical Properties of Cast Steels
- Making Steel for Castings
- Molding for Casting Steel
- Patterns and Molds for Steel Castings
- Making the Mold
- Machine Molding
- Cored Molds for Hollow Castings
- Gates, Risers and Vents
- Steel Casting & Finishing Operations Casting
- Shaking Out, Cleaning, Finishing and Testing
- Heat Treatment of Steel Castings
- Annealing
- Normalizing
- Quenching and Tempering
- Flame Hardening
- Heat- And Corrosion- Resistant Steel Castings
- Highly Alloyed Steels
- Typical Applications
- Melting
- Casting
- Molding
- Finishing Operations
- Methods of Sampling and Testing
- Precision Steel Castings
- Iron Castings
- Pig Iron for Castings
- Iron Composition vs.Properties
- Forms of Carbon in Pig Iron
- Influence of Silicon
- Effects of Manganese
- Influence of Sulphur
- Influence of Phosphorus
- Effects of Chromium
- Influence of Nickel
- Influence of Copper
- Effects of Molybdenum
- Effects of Titanium and Aluminum
- Influence of Vanadium
- Effects of Special Additives
- Iron-Foundry Melting
- Methods
- The Cupola
- The Electric Furnace
- Kinds and Uses of Iron Castings
- Alloyed Castings
- Iron-Foundry Molding and Casting Practice
- Testing of Cast Iron
Chapter 11
Project Profiles
- M.S. Billet casting with induction furnace from steel scrap & sponge iron
- Mini steel plant (3t-induction furnace)
- Steel rolling mill (by induction furnace) from steel scrap and sponge iron
- Rolling mill (by induction furnace) & manufacturing of bars, angles, squares, tubes and others
- Hot rolling mill of narrow steel strip plant economics
- Rolling mill & manufacturing of bars, angles, squares, tubes & others
- Cold rolling mill
- Steel rolling mill (reinforcement bars)
- Re-rolling mill (reinforcement and structural members)
- Sodium aluminate
- Super enamelled copper wire (from copper scrap)
- Super enamelled copper wire (from copper cathode rod)
- Copper rod wire drawing and pvc wire & cables
- G.I. wire
- Stainless steel cold rolling mill from coil
- Cold roll forming of z-section and other section
- Aluminium hot and cold rolling mill
- Forging plant steel casting
An extract from the book
TYPES OF MILLS
General Classification
The three principal types of rolling mills used for the rolling of steel are referred to as two-high, three-high, and four-high mills, shown schematically in Fig. 1.1. As the names indicate, the classification is based on the manner of arranging the rolls in the housings, a two-high stand consisting of two rolls, one above the other; a three-high mill has three rolls, and a four-high mill has hour rolls, arranged similarly. When rolling is in one direction only on two-high mills, and the piece is returned over the top of the rolls to be rerolled in the next pass, the mill is known as a pullover or drag-over mill. This type of mill formerly was used mainly for production of light sheets and tin plate; it still is used by merchant mills for rolling of tool and high-alloy steels. On two high reversing mills, the direction of rotation of the rolls can be reversed, and rolling is alternately in opposite directions, with work done on the piece while traveling in each direction. The long mill tables of reversing mills make it possible to handle heavy pieces in long lengths that would be impractical to roll on ordinary twohigh mills, or to handle on the lift tables of a three-high mill (see below). The reversing two-high type of mill occupies an important position in the industry and, with the use of manipulators, it is possible to produce on it slabs, blooms, plates, billets, rounds, and partially-formed sections suitable for later rolling into finished shapes on other mills. In all three-high mills, each roll revolves continuously in one direction; the top and bottom rolls in the same direction and the middle roll in the opposite direction. The piece is lifted from the bottom pass to the return top pass by mechanicallyoperated lift tables, or by inclined approach tables. Usually the large top and bottom rolls are drive, while the smaller middle roll is friction driven.
This latter roll is about two-thirds the size of the other two rolls, in order to permit removal through the housing windows. Four-high mills are used for rolling flat material, like sheets and plates, and represent a special type of two-high mill for both hot and cold rolling, in which large backing-up rolls are employed to reinforce the smaller working rolls: either the working or back-up rolls may be driven. Four-high mills resist the tendency of long working rolls to deflect, and permit the use of smalldiameter working rolls for producing wide plates, and hot-or coldrolled strip and sheets of uniform gage. These mills often consist of a number of stands spaced closely together in one continuous line and are known then as tandem mills; the product passes in a straight line from one stand to the next. In cluster mills, each of the two small working rolls is supported by two (or more) backing-up rolls. This latter type of mill is used for the rolling of thin sheets.
Arrangement of Mills
A single stand mill, which may be either two-, three- or fourhigh, and either reversing or non-reversing, represents the most common arrangement for rolling a wide range of products, including blooms, slabs, plates, sheets, and various sections. Guide, loop, and cross-country mills are made up of several two- or three-high stands, or a combination of both, and are used for rolling of merchant-bar sections. Guide mills are small hand mills consisting of several stands of rolls in a train. Mills in train have the rolls of separate stands in the same line, the rolls of one mill being driven from the end of the rolls of an adjacent stand. Guide mills take their name from the metal guides which support the piece in the correct position during its passage through the grooves of the various passes. For example, it is possible to roll from an oval section to a round in one pass, provided the oval is supported by metal guides. In many guide mills it is the practice of the catchers, in order to save time, to start the piece through each of the passes before it is through the preceding one, thus forming a loop, resulting in this arrangement being called a looping mill.
There originated in Belgium the plan for setting up an independent roughing stand preceding the finishing train of the looping mill. This arrangement became known as a Belgian mill. On looping mills, it was found that the loop could be made mechanically by a tube or house-shoe type trough, called a repeater, and thus dispense with the hand catchers. Prior to the looping mill, the piece was rolled throughout the entire length in one pass before it could be entered in the next pass. The looping arrangement eliminates the temperature difficulties encountered with long lengths. The shapes produced range from simple rounds and squares to intricate special country mill is so named because of the scattered location of its roll stands, and was developed for rolling sections that, due to size or shape, are not adaptable to loop rolling. These mills involve the continuous idea, but the stands are placed so far apart that the piece must leave one set of rolls before entering the next.
To save space and to avoid complicating the drives, the stands usually are arranged in two or more parallel lines, and the direction of travel of the piece is reversed during the rolling by employing transfer and skid tables. This arrangement results in a high production mill of great flexibility, which may be used for a wide range of products, including structural shapes, rails, and splice bars. A continuous mill consists of several stands of rolls arranged in a straight line (in tandem), with each succeeding stand operating with roll surface speed greater than its predecessor. Reduction takes place in several passes at the same time until the piece emerges as a finished shape for the last roll stand. This type of mill is in very common usage for rolling strip, sheet, billets, bars, rods, etc. A semi-continuous mill comprises also a reversing roughing stand for reducing the piece prior to entering the continuous mill for reduction to the finished shape. This arrangement gives moderately high production with lower first cost than a continuous mill. Combination mills are those in which the roughing or major part of the reduction is performed in a continuous mill, and the shaping in a guide or looping mill.
Speciality Mills
The universal mill is a combination of horizontal and vertical rolls, usually mounted in the same roll stand (Fig 1.1). The mill is made up of two-high (and occasionally three-high) horizontal rolls, with vertical roll sets on either or both sides of the horizontal stand. The vertical rolls also usually are driven. The direction of the piece is reversed after each pass in the mill. The universal mill is used to a limited extent also for plate product that requires rolled edges (see Fig 1.2). A special type of universal mill, known as the Gray mill is well adapted for rolling beams and H-sections of great width and depth without taper on flanges (see Fig 1.3). The horizontal rolls work on the web and flange thickness, while the idler vertical rolls in the same stand work simultaneously on flange thickness only. The roughing stands and intermediate stands are of the reversing type, and each has a separate stand of driven horizontal edging rolls which work on the flange height only. The finishing stand consists of the horizontal and vertical rolls in which the beams are given one pass only.
The Wenstrom mill is a similar modification of a universal plate mill, designed principally for rolling flats. Instead of acting upon the top and bottom and the two sides at different times, it does this simultaneously. The top roll can be adjusted vertically, and the bottom roll transversely, whereby peices of different thickness and width can be produced with the same set of rolls. The Sack universal mill, designed principally for rolling cruciform sections, has horizontal and vertical rolls which act upon the piece simultaneously, the general arrangement being much like that of the Wenstrom mill. A somewhat similar principle is employed in the Schoen mill for rolling of railroad car wheels, whereby the tread and flange are rolled simultaneously with the web, while rotating the forged wheel blank in a vertical position. This is accomplished by a pair of driven web rolls, and an idler tread roll in simultaneous contact with the wheel blank. A pair of idler rim rolls controls the width of rim.
How to Make Project Report?
Detailed Project Report (DPR) includes Present Market Position and Expected Future Demand, Technology, Manufacturing Process, Investment Opportunity, Plant Economics and Project Financials. comprehensive analysis from industry covering detailed reporting and evaluates the position of the industry by providing insights to the SWOT analysis of the industry.
Each report include Plant Capacity, requirement of Land & Building, Plant & Machinery, Flow Sheet Diagram, Raw Materials detail with suppliers list, Total Capital Investment along with detailed calculation on Rate of Return, Break-Even Analysis and Profitability Analysis. The report also provides a birds eye view of the global industry with details on projected market size and then progresses to evaluate the industry in detail.
We can prepare detailed project report on any industry as per your requirement.
We can also modify the project capacity and project cost as per your requirement. If you are planning to start a business, contact us today.
Detailed Project Report (DPR) gives you access to decisive data such as:
- Market growth drivers
- Factors limiting market growth
- Current market trends
- Market structure
- Key highlights
Overview of key market forces propelling and restraining market growth:
- Up-to-date analyses of market trends and technological improvements
- Pin-point analyses of market competition dynamics to offer you a competitive edge major competitors
- An array of graphics, BEP analysis of major industry segments
- Detailed analyses of industry trends
- A well-defined technological growth with an impact-analysis
- A clear understanding of the competitive landscape and key product segments
Need Customized Project Report?
- Ask for FREE project related details with our consultant/industry expert.
- Share your specific research requirements for customized project report.
- Request for due diligence and consumer centric studies.
- Still haven't found what you're looking for? Speak to our Custom Research Team
About Engineers India Research Institute:
Note: We can also prepare project report on any subject based on your requirement and country. If you need, we can modify the project capacity and project cost based on your requirement.
Our Clients
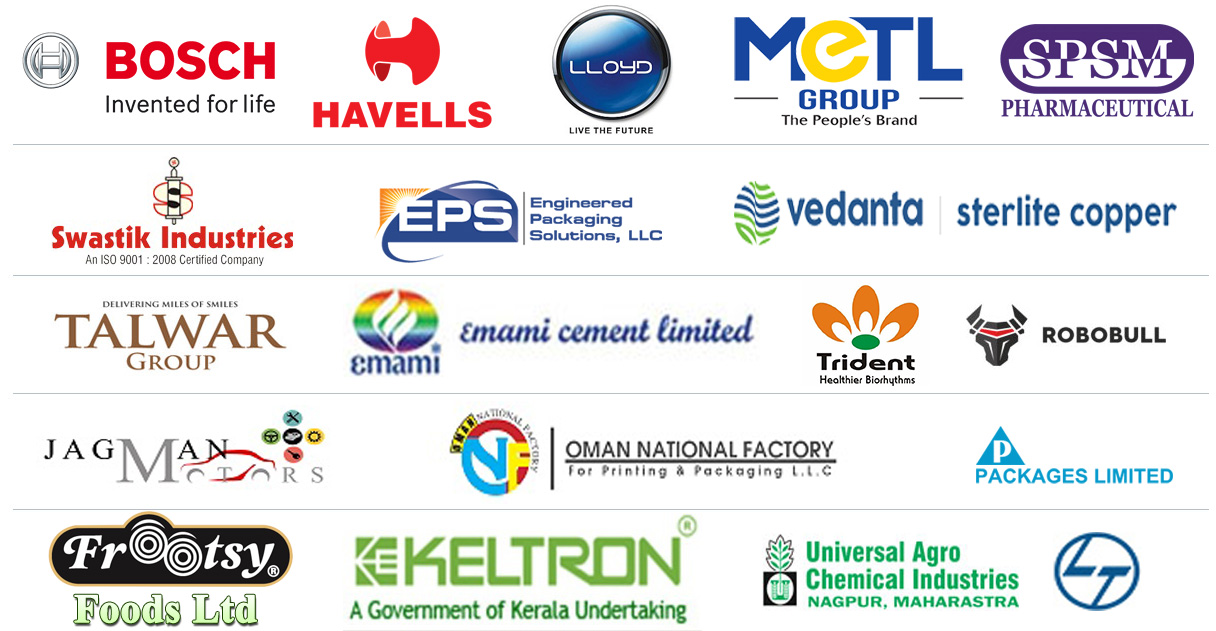
Our Approach
- Our research reports comprehensively cover Indian markets (can be modified as per your country), present investigation, standpoint and gauge for a time of five years*.
- The market conjectures are produced on the premise of optional research and are cross-accepted through associations with the business players
- We use dependable wellsprings of data and databases. What's more, data from such sources is handled by us and incorporated into the report
Why buy EIRI reports?
- Our project reports include detailed analysis that help to get industry Present Market Position and Expected Future Demand.
- Offer real analysis driving variables for the business and most recent business sector patterns in the business
- This report comprehends the present status of the business by clarifying a complete SWOT examination and investigation of the interest supply circumstance
- Report gives investigation and top to bottom money related correlation of real players/competitors
- The report gives gauges of key parameters which foresees the business execution