Detailed Project Report on Prefabricated Steel Framed Building Manufacturing Plant
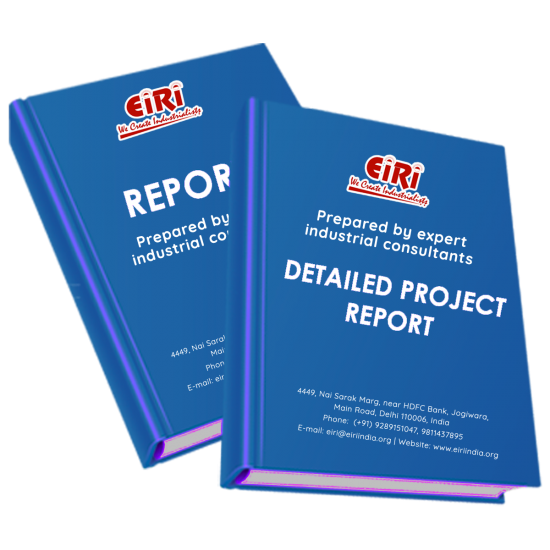
- More than 40 years of experience
- Managed by expert industrial consultants
- ISO 9001-2015 Certified
- Registered under MSME, UAM No: DL01E0012000
- 24/5 Research Support
Get your quesries resolved from an industry expert. Ask your queries before report or book purchase. - Custom Research Service
Speak to the our consultant to design an exclusive study to serve your research needs. - Quality Assurance
All reports are prepared by highly qualified consultants & verified by a panel of experts. - Information Security
Your personal & confidential information is safe & secure.
PREFABRICATED STEEL FRAMED BUILDING MANUFACTURING PLANT
[EIRI/EDPR/1392] J.C. 170US$,168INR
INTRODUCTION
There are many advantages to using prefabricated steel buildings. In comparison to conventional buildings, building time is cut in half by not only price but erection time and labor costs. They are also a sturdier alternative to most materials that are used in conventional building. Pre-fabricated steel buildings are also beneficial to those who have a limited amount of space to use. These buildings omit the space needed for conventional buildings properties like cement, bricks, timber and sand. These materials have to be purchased separately and cost more.
Pre-fabricated steel buildings do not require a high amount of maintenance. They also are made of corrosion resistant metals and will keep moisture away from important items stored within. Some purposes for these buildings include farm equipment storage or other mechanical equipment. Since pre-fabricated steel buildings can shield items from moisture but allow light into the internal area, they are preferred for nursery construction and protection of some foods that require dry areas to stay fresh.
These metal buildings come in either a modulated or manufactured version. Modular steel buildings are paralleled to building codes, whereas a manufactured fabricated metal building can be altered to the purchasers specifications. The pieces made by the manufacturer are pre-fabricated, pre-cut and pre-finished before shipment to the site at which the pieces will be constructed. Since there is so much pre-fabrication done by machines, the developers and purchasers can work together to make desired innovative changes to the steel buildings as they see fit. Picking the appropriate building is easy for not only the purchaser but for the manufacturer as well. It’s a simple process, utilized by various people looking an alternative to conventional buildings.
Before a manufacturer starts a steel building project, there are different factors to consider in the design of each metal building. A manufacturer will often times contact your county to confirm building codes and loads although as a purchaser you should always double check these loads before approving your building to be fabricated. Some of the general pieces that are included in a pre-fabricated building include pillars, a roof, door columns and headers. Upon completion, these larger pieces are transported to the site and then constructed using cranes, bolts and erection crews.
Pre-fabricated buildings will sometimes implement a metal clad roof, which can be removed if needed. Since all of these specific pieces are made of thick steel, firmly bolted together they are helpful in taking preventative measures in case of earthquakes and high winds. Since steel pieces used in the creation of these steel buildings are both quake and abrasion resistant, it makes for a secure structure that does what it’s created to do without concern from the owner or workers working inside it.
As a portion of modern architecture, these pre-fabricated metal businesses bring positive economic changes to the construction business. It also allows buyers to erect buildings cheaper and quicker for general use.
COST ESTIMATION
Plant Capacity 100 MT/Day
Land & Building (8000 sq.mt.) Rs. 7.70 Cr
Plant & Machinery Rs. 1.46 Cr
Working Capital for 2 Months Rs. 24.44 Cr
Total Capital Investment Rs. 33.92 Cr
Rate of Return 39%
Break Even Point 34%
CONTENTS
INTRODUCTION
USES AND APPLICATIONS
MARKET POSITION
PRE-ENGINEERED STEEL BUILDINGS MKT TO GROW AT 11% BY 2016
THE BUSINESS OF PREFABRICATED STRUCTURES
B.I.S. SPECIFICATIONS
PRESENT MANUFACTURE OF PRE FABRICATED BUILDING
FABRICATION PROCESS
STANDARD SPECIFICATIONS FOR PRE-FABRICATED METAL BUILDINGS
PROCESS FLOW CHART
PLANT LAYOUT
SPPPLIERS OF RAW MATERIALS
SUPPLIERS OF PLANT AND MACHINERY
APPENDIX – A:
01. PLANT ECONOMICS
02. LAND & BUILDING
03. PLANT AND MACHINERY
04. OTHER FIXED ASSESTS
05. FIXED CAPITAL
06. RAW MATERIAL
07. SALARY AND WAGES
08. UTILITIES AND OVERHEADS
09. TOTAL WORKING CAPITAL
10. TOTAL CAPITAL INVESTMENT
11. COST OF PRODUCTION
12. TURN OVER/ANNUM
13. BREAK EVEN POINT
14. RESOURCES FOR FINANCE
15. INSTALMENT PAYABLE IN 5 YEARS
16. DEPRECIATION CHART FOR 5 YEARS
17. PROFIT ANALYSIS FOR 5 YEARS
18. PROJECTED BALANCE SHEET FOR (5 YEARS)
How to Make Project Report?
Detailed Project Report (DPR) includes Present Market Position and Expected Future Demand, Technology, Manufacturing Process, Investment Opportunity, Plant Economics and Project Financials. comprehensive analysis from industry covering detailed reporting and evaluates the position of the industry by providing insights to the SWOT analysis of the industry.
Each report include Plant Capacity, requirement of Land & Building, Plant & Machinery, Flow Sheet Diagram, Raw Materials detail with suppliers list, Total Capital Investment along with detailed calculation on Rate of Return, Break-Even Analysis and Profitability Analysis. The report also provides a birds eye view of the global industry with details on projected market size and then progresses to evaluate the industry in detail.
We can prepare detailed project report on any industry as per your requirement.
We can also modify the project capacity and project cost as per your requirement. If you are planning to start a business, contact us today.
Detailed Project Report (DPR) gives you access to decisive data such as:
- Market growth drivers
- Factors limiting market growth
- Current market trends
- Market structure
- Key highlights
Overview of key market forces propelling and restraining market growth:
- Up-to-date analyses of market trends and technological improvements
- Pin-point analyses of market competition dynamics to offer you a competitive edge major competitors
- An array of graphics, BEP analysis of major industry segments
- Detailed analyses of industry trends
- A well-defined technological growth with an impact-analysis
- A clear understanding of the competitive landscape and key product segments
Need Customized Project Report?
- Ask for FREE project related details with our consultant/industry expert.
- Share your specific research requirements for customized project report.
- Request for due diligence and consumer centric studies.
- Still haven't found what you're looking for? Speak to our Custom Research Team
About Engineers India Research Institute:
Note: We can also prepare project report on any subject based on your requirement and country. If you need, we can modify the project capacity and project cost based on your requirement.
Our Clients
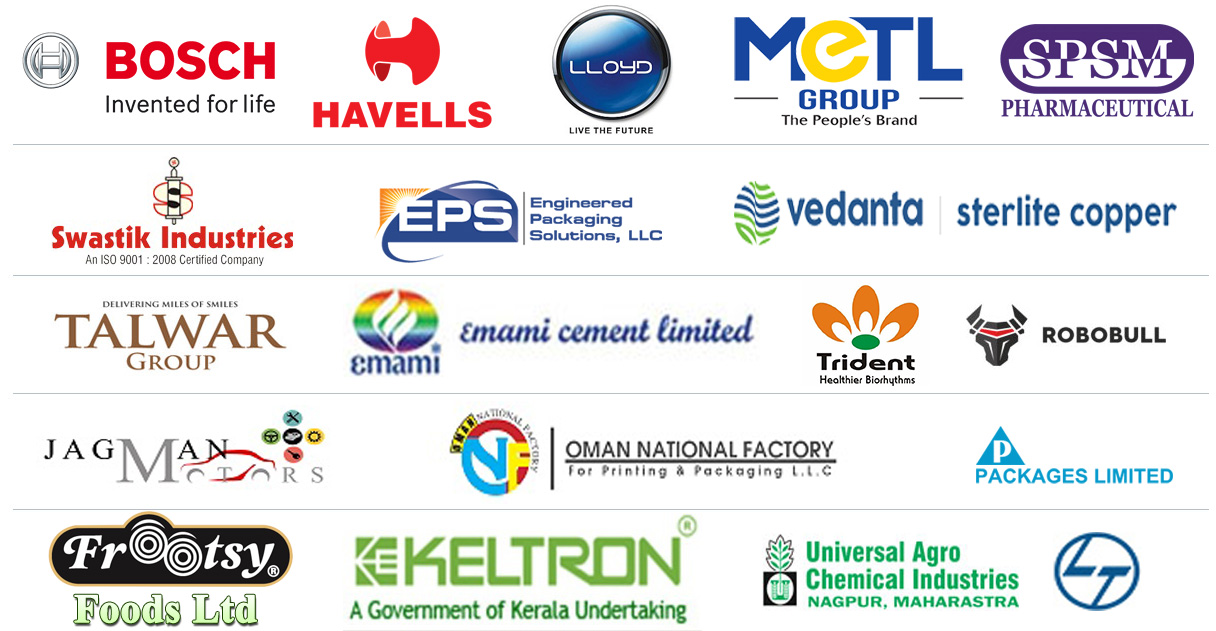
Our Approach
- Our research reports comprehensively cover Indian markets (can be modified as per your country), present investigation, standpoint and gauge for a time of five years*.
- The market conjectures are produced on the premise of optional research and are cross-accepted through associations with the business players
- We use dependable wellsprings of data and databases. What's more, data from such sources is handled by us and incorporated into the report
Why buy EIRI reports?
- Our project reports include detailed analysis that help to get industry Present Market Position and Expected Future Demand.
- Offer real analysis driving variables for the business and most recent business sector patterns in the business
- This report comprehends the present status of the business by clarifying a complete SWOT examination and investigation of the interest supply circumstance
- Report gives investigation and top to bottom money related correlation of real players/competitors
- The report gives gauges of key parameters which foresees the business execution