Detailed Project Report on wpc (plastic composite) door frame (4 Tons/day)
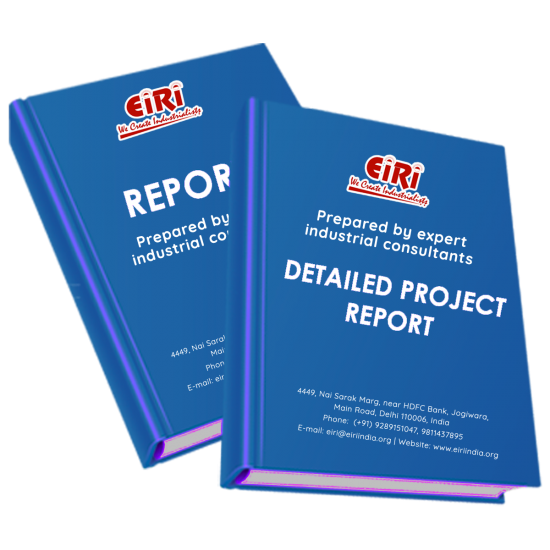
- More than 40 years of experience
- Managed by expert industrial consultants
- ISO 9001-2015 Certified
- Registered under MSME, UAM No: DL01E0012000
- 24/5 Research Support
Get your quesries resolved from an industry expert. Ask your queries before report or book purchase. - Custom Research Service
Speak to the our consultant to design an exclusive study to serve your research needs. - Quality Assurance
All reports are prepared by highly qualified consultants & verified by a panel of experts. - Information Security
Your personal & confidential information is safe & secure.
WPC (PLASTIC COMPOSITE) DOOR FRAME
[CODE NO.4323]
Wood–plastic composites (WPCs) are a form of composite combining wood-based elements with polymers. The processes for manufacturing WPCs include extrusion, injection molding, and compression molding or thermoforming (pressing). Newer manufacturing processes for WPCs include additive manufacturing via fused layer modeling and laser sintering. An important constraint for polymers used in WPCs is requiring process conditions (melt temperature, pressure) that will not thermally degrade the wood filler. Wood degrades around 220°C; thus, general-purpose polymers like polyethylene and poly vinyl chloride are typically used for manufacturing WPCs. Wood fibers are inherently hydrophilic because of the hydroxyl groups contained in the cellulose and hemicellulose molecular chains. Thus, modification of the wood fiber via chemical or physical treatments is very critical to making improved WPCs. The most abundant profiles made from wood–plastic composites are boards or lumber used in outdoor decking applications. Although early WPC products were mainly extruded for profiled sections, nowadays, many injected parts made of WPC are being introduced for various industries, including electrical casings, packaging, daily living supplies, and civil engineering applications. Mold and mildew and color fading of WPCs tend to be the durability issues of prime importance for WPCs.
An important constraint for polymers used in WPCs is requiring process conditions (melt temperature, pressure) that will not thermally degrade the wood filler. Wood degrades around 220°C; thus, general-purpose polymers like polyethylene and poly vinyl chloride are typically used for manufacturing WPCs. Wood fibers are inherently hydrophilic because of the hydroxyl groups contained in the cellulose and hemicellulose molecular chains. Thus, modification of the wood fiber via chemical or physical treatments is very critical to making improved WPCs. The most abundant profiles made from wood–plastic composites are boards or lumber used in outdoor decking applications. Although early WPC products were mainly extruded for profiled sections, nowadays, many injected parts made of WPC are being introduced for various industries, including electrical casings, packaging, daily living supplies, and civil engineering applications. Mold and mildew and color fading of WPCs tend to be the durability issues of prime importance
for WPCs. Most recent research on WPC durability focuses on studies to better understand the mechanisms contributing to various degradation issues as well as methods to improve durability. the area of nano additives for WPCs including nanocellulose. Recently, the trend of patent registrations for WPCs has shifted to new products or applications instead of the materials itself.
Wood plastic composites (WPCs) are roughly 50:50 mixtures of thermoplastic polymers and small wood particles. The wood and thermoplastics are usually compounded above the melting temperature of the thermoplastic polymers and then further processed to make various WPC products. WPC can be manufactured in a variety of colors, shapes and sizes, and with different surface textures. Depending on the processing method, WPCs can be formed into almost any shape and thus are used for a wide variety of applications, including windows, door frames, interior panels in cars, railings, fences, landscaping timbers, cladding and siding, park benches, molding and furniture. One commonly available example of WPCs is the decking lumber that is often better known by its various brand names – e.g., Trex™, ChoiceDek™, Eon™ or SmartDeck™ – or as the generic term “composite lumber.”
WPCs offer a number of potential benefits. The presence of wood in a plastic matrix can result in a stiffer and lower-cost material than if plastic alone was used. Also, the compression properties (resistance to crushing) for most WPCs are superior to that of wood loaded perpendicular to the grain. The plastic in the product is not subject to water absorption or biological attack, so the WPC can have lower maintenance requirements than solid wood. WPC lumber will not warp, splinter or check.
WPCs offer great flexibility in the shapes and colors of the materials produced. Materials usage can be also be reduced through the engineering of special shapes – e.g., hollow-core decking boards.
The wood component within WPCs does impart some positive attributes compared to plastic; however, the inherent problems with wood (moisture sorption and susceptibility to mold and decay) remain. Water can penetrate into WPCs, albeit at a much lower rate and level compared to solid wood or other wood composites. The resulting sorption of water can promote the growth of mold and decay fungi; however, aesthetics - not structural issues - dominate consumer callbacks. Color fade from sunlight is also accelerated when wood is added to thermoplastics, causing a whitening or graying of the surface of the composite.
WPCs can be produced in almost any color and shape. Hollow decking boards can reduce material usage.
WPCs are also usually quite heavy and not as stiff as solid wood. This limits the potential use of WPCs in many structural applications and creates the potential creep or sagging problems, especially in a warm environment. On the other hand, this flexibility can be an advantage: WPC can be bent on-site to make attractive patterns.
WPC is touted as having environmental benefits, because it is made from residues (wood) or recycled materials (plastic). However, virgin plastics are commonly supplemented in WPC operations to maintain tighter quality control and offset highly fluctuating recycled plastic inventories. WPC also requires large amounts of energy to produce. WPC is theoretically recyclable; it could be re-melted and reformed into new decking lumber. However, no recycling of this new product is currently underway, with exception of recycling of off-specification material during manufacture. The collection, cleaning and transportation of old WPC to a recycling center for remanufacture are likely to be prohibitively expensive.
As mentioned, the reasons for using WPC are many; however, there are other causes that men forced many countries to tend for using alternative sources to virgin materials. In the United States, for example, the U.S. Environmental Protection Agency, by the beginning of 2004, has phased out the usage of wood treated with chemicals such as the chromate copper arsenate (CCA) to prevent environmental and microbial degradation. As this type of wood was used in the building products' market concerned with residential applications such as decking, the need for the alternative survived the WPC market. In Europe, environmental concerns are focused on limiting the use of finite resources and the need to manage waste disposal; therefore, the tendency to recycle materials at the end of their useful life has increased tremendously. Recycling polymers in Europe was less preferred than other types of materials such as metal; however, illegality of land filling and waste management priority in many European countries were the motive to do so. In addition to the enforced environmental policies, the growth of environmental awareness led to a new orientation to use wasted natural materials for different applications and industries such as the automotive, packaging and construction industries.
COST ESTIMATION
Plant Capacity 4 Ton/Day
Land & Building (2000 sq.mt.) Rs. 1.14 Cr
Plant & Machinery Rs. 1.43 Cr
Working Capital for 1 Month Rs. 1.38 Cr
Total Capital Investment Rs. 4.15 Cr
Rate of Return 29%
Break Even Point 72%
- INTRODUCTION
- WPCS CAN BE PRODUCED IN ALMOST ANY COLOR AND SHAPE.
- HOLLOW DECKING BOARDS CAN REDUCE MATERIAL USAGE
- ADVANTAGE OF PVC/WPC DOOR FRAME
- USES & APPLICATIONS OF WPC
- OURDOOR APPLICATION OF WPC
- RAW MATERIALS
- WOOD
- PARTICLE GEOMETRY
- ANY SPECIES CAN BE INCORPORATED INTO WPCS. NON-WOOD
- FIBERS CAN ALSO BE USED.
- MOISTURE CONTENT:
- ADDITIVES
- POLYMERS
- FIGURE: TRENDS IN THE POLYMER PROPERTIES OF THERMOPLASTICS
- AS A FUNCTION OF TEMPERATURE
- FIGURE: TYPICAL ROOM TEMPERATURE PROPERTIES OF COMMON POLYMERS
- WOOD
- ADVANTAGE AND DISADVANTAGE OF WPC
- ADVANCE MATERIALS FOR WPC
- WOOD MODIFICATION
- ADDITIVES
- PROFILES
- ASPECT OF WPC DURABILITY
- STRUCTURAL
- WEATHERING STUDIES
- COMPOUNDED FORMULATION OF WPC DOOR FRAME
- FORMULATION OF WPC
- FIGURE: POLYETHYLENE (PE) – BASED COMPOSITE
- MANUFACTURING TECHNIQUE FOR WPC
- COMPOUNDING:
- FORMING:
- DIFFERENT PROCESSES FOR PLASTIC COMPOSITES
- EXTRUSION PROCESSING
- SINGLE-SCREW EXTRUDER
- COUNTER-ROTATING TWIN-SCREW EXTRUSION
- COMPOSITE SYSTEM
- MISCELLANEOUS POST-EXTRUDER UNIT OPERATIONS
- MARKET OVERVIEW OF WPC
- APPLICATION FIELDS OF WPC IN EUROPE
- MAIN COUNTRIES OF EUROPEAN WPC PRODUCTION OF DECKING,FENCING AND OTHER CONSTRUCTION APPLICATIONS
- MARKET TRENDS IN WOOD PLASTIC COMPOSITE
- PRESENT MANUFACTURERS OF WOOD PLASTIC COMPOSITE
- RICE HUSKS PLASTICS COMPOSITE AND IT’S ADVANTAGE
- WORKING WITH RH-PVC COMPOSITE MATERIALS
- HOW RH-PVC PRODUCTS CAN BE CUSTOMIZED FOR VALUE ADDITION?
- THE ABOVE PROCESSES ARE EXPLAINED IN BRIEF BELOW
- A) FORMULATING RH-PVCS FOR SPECIFIC PERFORMANCE REQUIREMENTS
- (I) FOAMING TO PRODUCE A CELLULAR MATERIAL
- FOAMING OF RH-PVC PROVIDES OTHER ADVANTAGES BESIDES WEIGHT REDUCTION
- (II) COUPLING FOR STRENGTH
- (III) COLORANTS FOR WOOD-LIKE APPEARANCE
- (IV) LUBRICANTS FOR HIGH THROUGHPUT
- (V) COMBATING WEATHERING, COLOR FADING, MOLD & AMP; MILDEW
- (VI) FLAME RETARDANT & MINERAL FILLERS
- B) PHYSICAL PROCESSES FOR SURFACE MODIFICATIONS
- C) CO-EXTRUDING A CAP LAYER
- D) SURFACE LAMINATION, COATING AND PRINTING
- ADVANTAGE OF FOAMED RH PVC PRODUCTS OVER SOLID RH PVC
- FIGURE 1
- FIGURE 2
- PROCESS FLOW DIAGRAM FOR PLASTIC COMPOSITE
- THE WPC (PLASTIC COMPOSITE) MANUFACTURING PROCESS WITH EXTRUSION FORMING
- TABLE 2.0: FUNCTIONS OF ADDITIVES USED IN THERMOPLASTIC COMPOSITES
- PROCESS DESCRIPTION OF WPC USING RICE HUSK
- A PRE-PROCESSING
- B EXTRUSION AND FORMING THE END PRODUCT
- C POST PROCESSING
- PRODUCTION PROCESS FLOWCHART
- TYPICAL RH-PVC DOOR FRAME PRODUCTION PROCESS
- FIGURE 01
- TYPICAL TWO STEP MANUFACTURING PROCESS
- FIGURE 02
- TYPICAL IN-LINE MANUFACTURING PROCESS
- TYPICAL RICE-HUSK PLASTIC COMPOSITE PRODUCTION EQUIPMENT
- TYPES OF EXTRUDERS USED IN RH-PVC PRODUCTION
- FIGURE 03
- FIGURE 04
- ADVANTAGES OF TWIN-SCREW EXTRUDER VERSUS SINGLE SEXTRUDER
- ADVANTAGES OF CONICAL TWIN SCREW EXTRUDER
- DETAILS OF ADDITIVE
- POLLUTION CONTROL NORMS AND ENVIRONMENTAL IMPACT
- MANUFACTURING PROCESS OF WPC
- EXTRUSION PROCESSING
- SINGLE-SCREW EXTRUDER
- COUNTER-ROTATING TWIN-SCREW EXTRUSION
- CO-ROTATING TWIN-SCREW AND HOT MELT SINGLE-SCREW WOODCOMPOSITE SYSTEM
- WOOD TRUDER
- MISCELLANEOUS POST-EXTRUDER UNIT OPERATIONS
- INJECTION MOLDING
- COMPRESSION MOLDING OR THERMOFORMING
- CODES AND STANDARD
- INDICATIVE PROPERTIES OF GENERIC RH-PVC COMPOSITE
- TECHNICAL/TURNKEY CONSULTANT FOR SETTING UP WPC PLANT
- SUPPLIERS OF PLANT & MACHINERIES (IMPORTED)
- SUPPLIERS OF PLANT & MACHINERIES (INDIAN)
- SUPPLIERS OF BOILER
- SUPPLIERS OF GENERATOR SET (D.G. SET)
- SUPPLIERS OF EXTRUDERS
- SUPPLIERS OF PRESSING MACHINE
- SUPPLIERS OF COOLING TOWERS
- SUPPLIERS OF GENERATOR SET (D.G. SET)
- MANUFACTURERS/SUPPLIERS OF RAW MATERIALS
- SUPPLIERS OF RICE HUSK
- SUPPLIERS OF PLASTIC POLYMERS
- SUPPLIERS OF COUPLING AGENT
- SUPPLIERS OF ADDITIVES
APPENDIX – A:
01. PLANT ECONOMICS
02. LAND & BUILDING
03. PLANT AND MACHINERY
04. OTHER FIXED ASSESTS
05. FIXED CAPITAL
06. RAW MATERIAL
07. SALARY AND WAGES
08. UTILITIES AND OVERHEADS
09. TOTAL WORKING CAPITAL
10. TOTAL CAPITAL INVESTMENT
11. COST OF PRODUCTION
12. TURN OVER/ANNUM
13. BREAK EVEN POINT
14. RESOURCES FOR FINANCE
15. INSTALMENT PAYABLE IN 5 YEARS
16. DEPRECIATION CHART FOR 5 YEARS
17. PROFIT ANALYSIS FOR 5 YEARS
18. PROJECTED BALANCE SHEET FOR (5 YEARS)
How to Make Project Report?
Detailed Project Report (DPR) includes Present Market Position and Expected Future Demand, Technology, Manufacturing Process, Investment Opportunity, Plant Economics and Project Financials. comprehensive analysis from industry covering detailed reporting and evaluates the position of the industry by providing insights to the SWOT analysis of the industry.
Each report include Plant Capacity, requirement of Land & Building, Plant & Machinery, Flow Sheet Diagram, Raw Materials detail with suppliers list, Total Capital Investment along with detailed calculation on Rate of Return, Break-Even Analysis and Profitability Analysis. The report also provides a birds eye view of the global industry with details on projected market size and then progresses to evaluate the industry in detail.
We can prepare detailed project report on any industry as per your requirement.
We can also modify the project capacity and project cost as per your requirement. If you are planning to start a business, contact us today.
Detailed Project Report (DPR) gives you access to decisive data such as:
- Market growth drivers
- Factors limiting market growth
- Current market trends
- Market structure
- Key highlights
Overview of key market forces propelling and restraining market growth:
- Up-to-date analyses of market trends and technological improvements
- Pin-point analyses of market competition dynamics to offer you a competitive edge major competitors
- An array of graphics, BEP analysis of major industry segments
- Detailed analyses of industry trends
- A well-defined technological growth with an impact-analysis
- A clear understanding of the competitive landscape and key product segments
Need Customized Project Report?
- Ask for FREE project related details with our consultant/industry expert.
- Share your specific research requirements for customized project report.
- Request for due diligence and consumer centric studies.
- Still haven't found what you're looking for? Speak to our Custom Research Team
About Engineers India Research Institute:
Our Approach
- Our research reports comprehensively cover Indian markets (can be modified as per your country), present investigation, standpoint and gauge for a time of five years*.
- The market conjectures are produced on the premise of optional research and are cross-accepted through associations with the business players
- We use dependable wellsprings of data and databases. What's more, data from such sources is handled by us and incorporated into the report
Why buy EIRI reports?
- Our project reports include detailed analysis that help to get industry Present Market Position and Expected Future Demand.
- Offer real analysis driving variables for the business and most recent business sector patterns in the business
- This report comprehends the present status of the business by clarifying a complete SWOT examination and investigation of the interest supply circumstance
- Report gives investigation and top to bottom money related correlation of real players/competitors
- The report gives gauges of key parameters which foresees the business execution